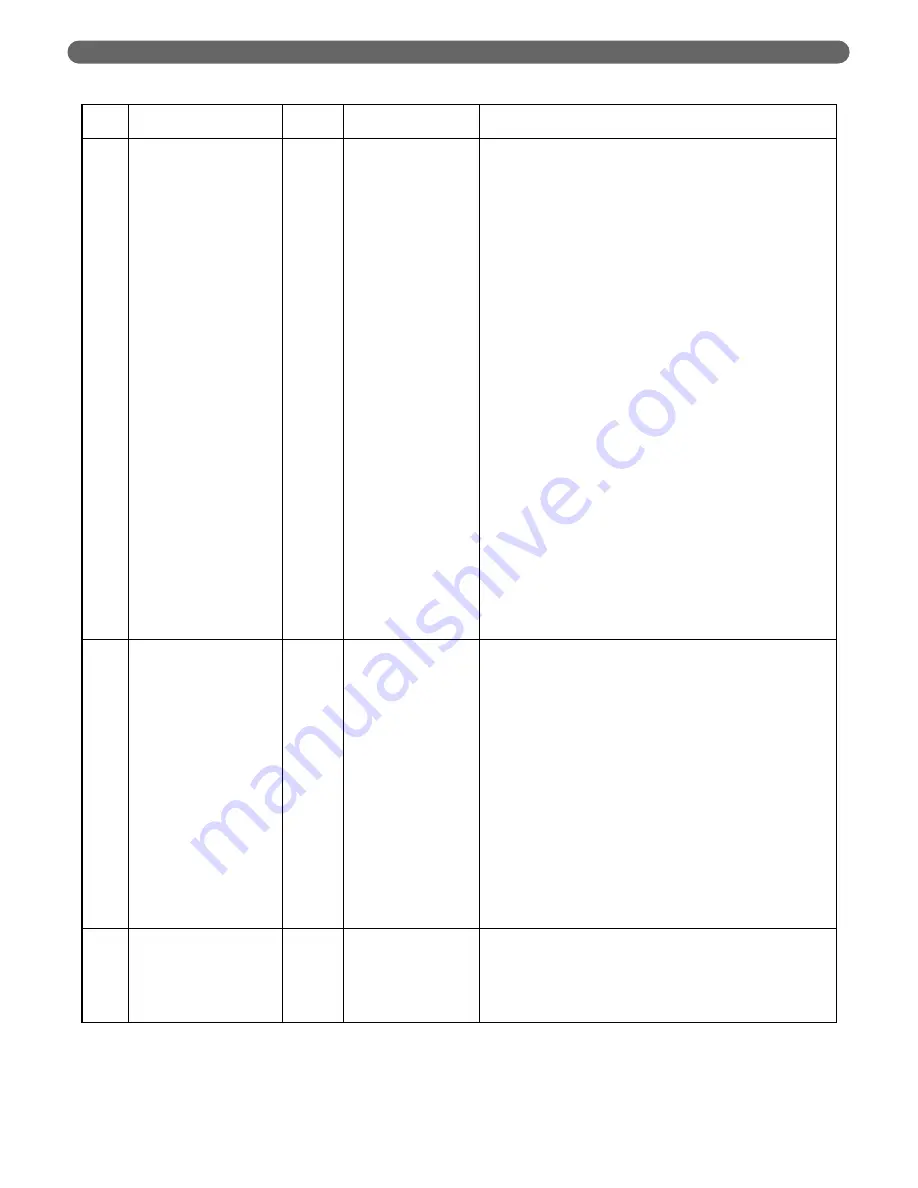
60
TROUBLESHOOTING
Table 10.2: Control Board Locking Error Codes (manual reset):
“A”
CODE
Error Display
Internal
No.
Error Description
Corrective Action
A01
IGNITION ERROR
1
Three consecutive
unsuccessful ignition
attempts.
1. Watch the igniter through the observation window.
2. If no spark is present, check the spark electrode for the proper
3/16" gap. (DO NOT try to bend the electrodes if they have been
operating for an extended period. Heat causes them to become
brittle and they may break.)
• Remove any corrosion from the spark electrode with abrasive.
3. If a spark is present but no flame results, check the gas supply to
the boiler.
• Check for either high or low gas pressure. (See table 5.3)
• Try restricting the air to the burner by covering the air inlet vanes
on the swirl plate. If ignition results, check the combustion
products using a combustion analyzer. If the combustion is out of
tolerance (see table 5.4) contact your PB Heat representative.
4. If a flame is present but the burner drops out, check the flame
sensor log in the Installer Menu (Meas. 1, 2, 3, 4).
• The flame Meas. Values are the flame signal at 1/2 second
intervals during the last 2 seconds of trial for ignition after the
spark has stopped but before proving ignition. If Meas. 4 is
below 3.1 µA, the control will not stay running.
• If the flame signal is too low, remove the burner plate and check the
distance between the sensor and the burner. If it is greater than 1/4"
the flame sensor should be replaced and the new sensor should be
bent to be sure it is between 1/8" and 3/16" from the burner. (DO
NOT try to bend the electrode if it has been operating for an extended
period. Heat will cause it to become brittle and it may break.)
5. Determine if the gas valve is opening by monitoring gas pressure.
Also, listen for the solenoid valve to pull in.
• If the gas valve is not opening, check to be sure the harness
connections are not faulty.
• If the harness appears correct, replace the gas valve. (Before
beginning this replacement, connect the gas valve to be sure it
operates correctly before removing the old one. If it doesn’t
operate correctly, the existing valve may not be bad.
A02
FLAME FAILURE
24
Three consecutive
flame failures during
one demand.
1. If boiler sparks, lights briefly and then goes out:
a. Disconnect the flame sensor cable and then retry ignition.
b. If the flame stays lit, allow the boiler to run for several minutes
and then reattach the cable.
c. If the problem persists, remove the flame sensor and inspect
the burner through the sensor opening. If metal fibers are
protruding from the burner, use a blunt probe to move the
fibers away from the sensor.
d. If the problem is still present, replace the flame sensor.
2. If the unit locks out on flame failure during normal operation:
a. Check gas pressure at the inlet to the gas valve (See figure 5.2)
while the boiler is operating.
b. Check the flame signal in the Installer Menu under Status. This
will also show the total number of flame failures. If the flame
signal reads less than 2.8 µA, clean the sensor and igniter. Be
sure that the wiring harness is fully seated at the control.
c. If the flame signal is consistently low, check the signal with the
sensor disconnected. If the flame signal improves, replace the
flame sensor.
A03
OVERHEAT LIMIT OPEN
18
High Temperature Limit
Open (Set Temperature
205°F)
1. Check CH, DHW, General Pump Operation
2. Assure that there is adequate flow through the boiler by checking
the status menu and assuring less than 40°F temperature rise
across the boiler.
3. Check resistance reading on the supply thermistor. Replace it if
necessary. See Figure 8.3 for resistance values.
** If persistent locking errors, A04 through A18, occur, systematically disconnect all wires that were not supplied by the factory with the exception
of the power supply (CH T?stat, DHW T?stat, LWCO and Pumps). If the error code goes away, determine if there may be feedback from one of
the circuits. If the Error occurs with all of these disconnected, there is likely a problem with the control board.
Содержание PureFire PF-110
Страница 26: ...24 WATER PIPING AND CONTROLS Figure 4 7 Two Boilers Primary Secondary with Four Zones Zone Circulator ...
Страница 27: ...25 Figure 4 8 Three Boilers Primary Secondary with Five Zones Zone Circulator WATER PIPING AND CONTROLS ...
Страница 28: ...26 WATER PIPING AND CONTROLS Figure 4 9 Three Boilers Primary Secondary with Four Zones Zone Valves ...
Страница 37: ...35 ELECTRICAL CONNECTIONS Figure 7 5 Internal Wiring Schematic for PF 50 PF 80 PF 110 PF 140 boilers ...
Страница 38: ...36 Figure 7 6 Internal Wiring Schematic for PF 200 PF 210 PF 300 PF 399 boilers ELECTRICAL CONNECTIONS ...
Страница 75: ...73 REPAIR PARTS Figure 13 2 Heat Exchanger Burner Assembly Repair Parts PF 50 PF 80 PF 110 PF 140 ...
Страница 77: ...75 REPAIR PARTS Figure 13 3 General Repair Parts PF 200 PF 210 PF 300 PF 399 ...
Страница 79: ...77 Figure 13 4 Heat Exchanger Burner Assembly Repair Parts PF 200 PF 210 PF 300 PF 399 REPAIR PARTS ...
Страница 82: ...80 APPENDIX A STATUS SCREENS APPENDIX A STATUS SCREENS ...
Страница 83: ...81 APPENDIX A STATUS SCREENS ...
Страница 84: ...82 APPENDIX A STATUS SCREENS ...
Страница 85: ...83 APPENDIX A STATUS SCREENS ...
Страница 86: ...84 APPENDIX B USER MENU APPENDIX B USER MENU ...
Страница 87: ...85 APPENDIX C INSTALLER MENU APPENDIX C INSTALLER MENU ...
Страница 88: ...86 APPENDIX C INSTALLER MENU ...
Страница 89: ...87 APPENDIX C INSTALLER MENU ...
Страница 90: ...88 APPENDIX C INSTALLER MENU ...
Страница 91: ...89 APPENDIX C INSTALLER MENU ...