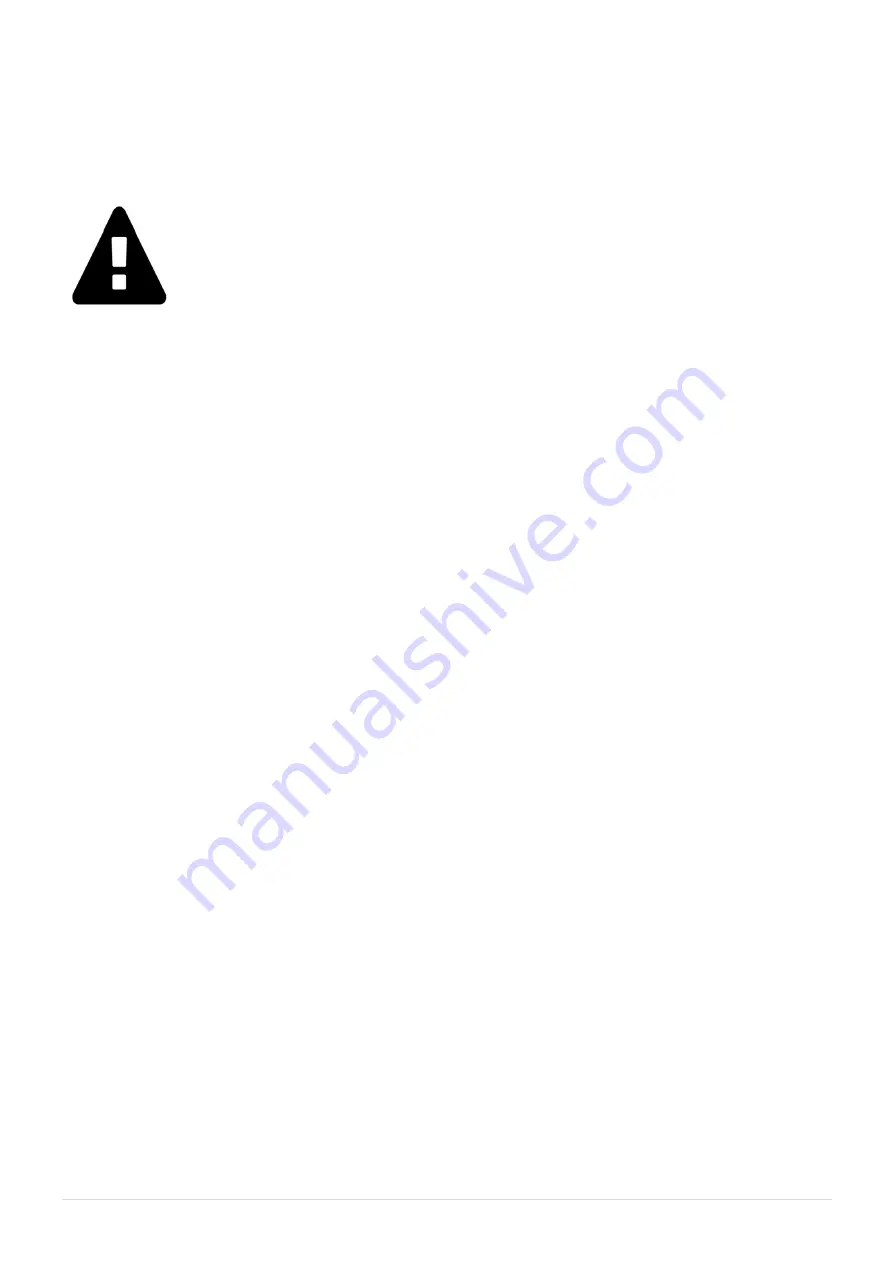
23 | P a g e
PATON
®
PSI STANDARD SERIES DC MIG/MAG TIG/MMA
5.4 FUNCTION OF INCREASES THE WIRE FEED SPEED
This function is intended for smooth transition into welding mode for a limited time
[
TIME UP SPEED
]
,
which reduces spill of the weld pool and splashes when the arc is ignited when the wire is cold. Increased
time of smooth transition is used for the initial formation of the lake.
ATTENTION!
The longer the rise time, the lower the initial penetration, which
is why the function is recommended when laying long or medium length joints.
When grafting material, do not increase the value higher than 0.1s.
5.5 FUNCTION OF BURNING OUT AT THE END OF WELDING
This function is designed for the smooth welding of a welding crater, which can be formed in the welding
pool due to electromagnetic blow forces generated by the welding arc. The crater so formed can be a
source of future welding defects. This function should be activated by releasing the corresponding button
on the welding torch at the end of the welding process. After this, the movement of the welding torch
should be terminated, and the welding crater should be welded in the welding voltage decay mode. The
default voltage modulated reduction period
[TIME DOWN VOLTAGE]
is 1.0 s and can be varied by the
operator at his option
(see Section 6.1).
5.6 FUNCTION OF POSTWELD GAS CLEANING
This function is intended to clean the shielding gas welding zone after the welding arc has expired. The
welded lake is exposed to the harmful effects of atmospheric air. By default, the purge time
[TIME POST
GAS]
is set to 1.5 seconds, this value can be changed at any time in its sole discretion.
5.7 INDUCTANCE CONTROL FUNCTION
Inductance control allows optimization of the arc characteristics according to the welded thickness
element and welding method and conditions. This function is necessary to change the slew rate of the
current when the arc voltage changes. The thinner the element to be welded with the met MIG/MAG the
inductance should be higher (soft arc - less fusion), for thick elements vice versa (hard arc - greater
embedding). As a result, the spatter decreases, but affects the droplet transfer process, which leads to a
slowdown of the welding process and a strong decrease in the droplet transfer frequency at high values of
inductance. Thus, changing this function, each user is given the opportunity to choose the optimal
welding process for himself. By default, the inductance is set to “OFF”, that is, it is set to zero.
Operations required to set these parameters for the current welding process are described in Section 6.1.
Содержание PSI 160 Standard
Страница 1: ......