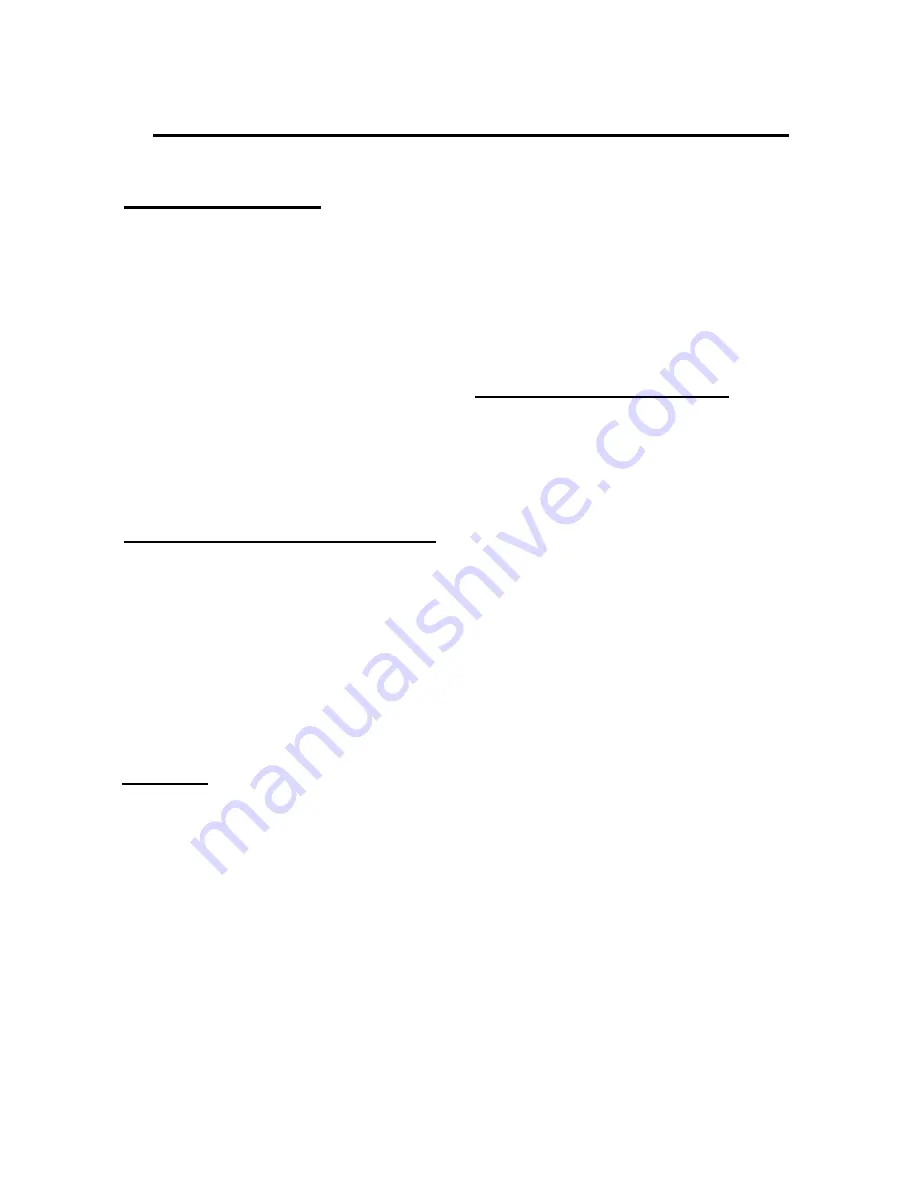
GP-M230-BX-010A
2300 / IO 210 Manual
RD: June 2006
R.L. 10A
KH
Start up - Heat Mode:
On a call for heat the Fenwal 35-60 control
will reset, perform a self check routine,
flash the diagnostic LED for up to four sec-
onds. The gas valve and spark are energized
commencing the trial for ignition period.
When flame is detected during the trial for
ignition, spark is shutoff immediately and
the gas valve remains energized. The ther-
mostat and main burner flame are con-
stantly monitored to assure the system con-
tinues to operate properly. When the ther-
mostat is satisfied and the demand for heat
ends, the gas valve is de-energized.
Flame Failure - Multi Trial Model:
Should the main burner fail to light, or the
flame is not detected during the first trial for
ignition period, the gas valve is deenergized
and the control goes through an interpurge
delay before another ignition attempt. The
control will attempt two additional ignition
trials before going into lockout and the
valve relay is de-energized.
15. SEQUENCE OF OPERATION FOR FENWAL 35-60 DSI CONTROL
(See page 13 for HONEYWELL control)
Recovery from lockout requires a manual re-
set by either resetting the thermostat or re-
moving 24 volts for a period of 5 seconds. If
the thermostat is still calling for heat after
one hour the control will automatically reset
and attempt to ignite the burner again.
Flame Failure - Re-Ignition:
If the established flame signal is lost while the
burner is operating, the control will respond
within 0.8 seconds. The HV spark will be ener-
gized for a trial ignition period in an attempt to
relight the burner.
If the burner does not light the control will
make two more attempts to relight the burner
before de-energizing the gas valve. If the
burner does not relight, the control will go into
lockout as noted above in “Failure to light”. If
flame is re-established, normal operation re-
sumes.
Multi-try models will allow three tries
for ignition including interpurges.
Cautions
:
1. Ceramic insulators should not be in or close to the flame.
2. Electrode assemblies should not be adjusted or disassembled. Electrodes should
have a gap spacing of 1/8”- 3/16” (3.12± 0.81 mm). If this spacing is not correct,
the assembly must be replaced. Electrodes are preset and NOT field adjustable.
3. Exceeding the temperature limits can cause nuisance lockouts and premature electrode
failure.
The control must be secured in an area that will experience a minimum of vibration and re-
main below the maximum operating temperature of 160°F.
Page 19
Содержание 2300 series
Страница 11: ...GP M230 BX 010A 2300 IO 210 Manual RD June 2006 R L 10A KH Diagram 4 2300 MOUNTING ARM TEMPLATE Page 7...
Страница 12: ...GP M230 BX 010A 2300 IO 210 Manual RD June 2006 R L 10A KH Diagram 5 2300 WALL BRACKET TEMPLATE Page 8...
Страница 14: ...GP M230 BX 010A 2300 IO 210 Manual RD June 2006 R L 10A KH Page 10 Diagram 7 SERVICING HEATER...
Страница 28: ...GP M230 BX 010A 2300 IO 210 Manual RD June 2006 R L 10A KH...