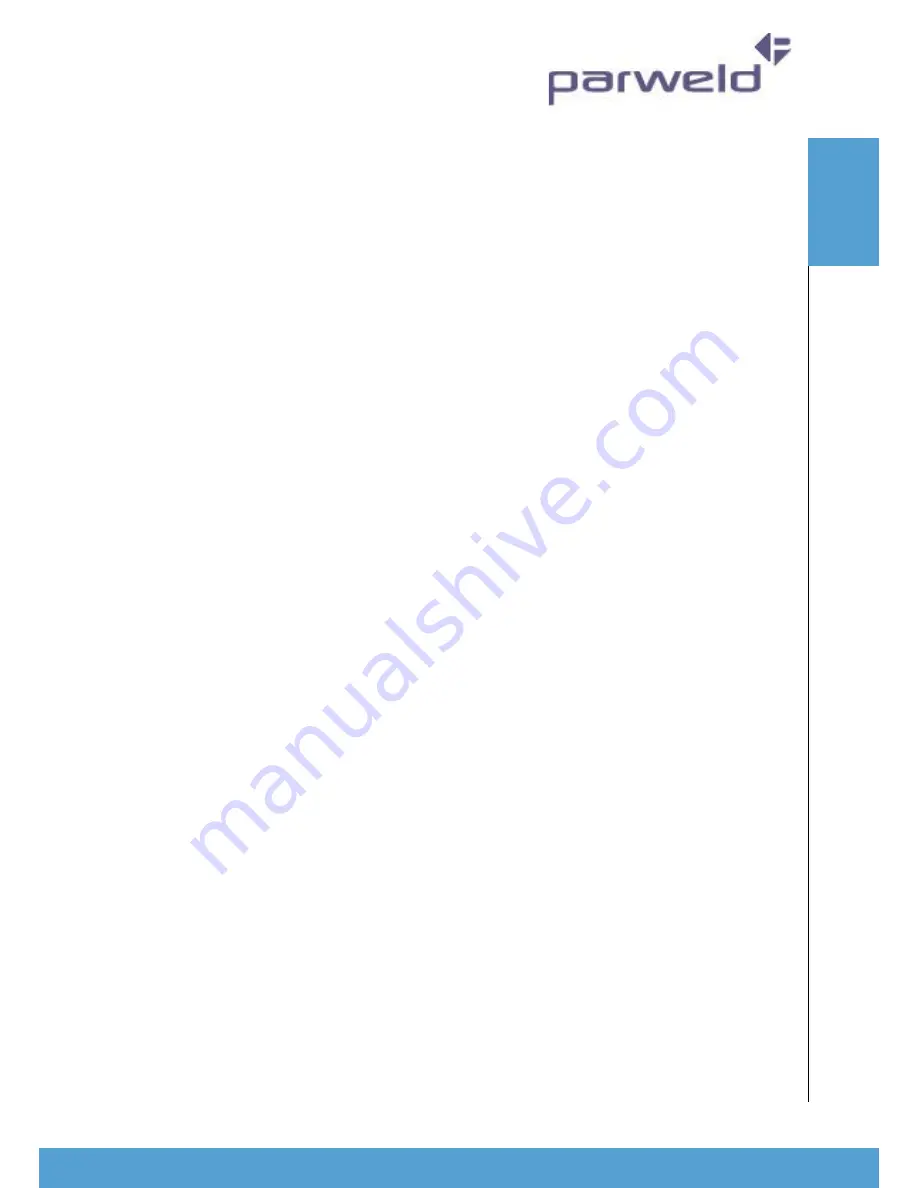
www.parweld.com
www.parweld.com
7
8) Output power switch.
This switch has 3 positions
the top position selects DC output in TIG or MMA
mode. The centre position selects AC output in MMA
or TIG mode and the bottom position allows a gas test
or purge to be performed when TIG welding.
9) Initial Current/Hotstart
This control is dual function
in TIG mode it sets the start level for the welding
current as a percentage of the main welding current.
In MMA mode it allows adjustment of the welding
current surge on arc striking to give reliable arc
striking in all conditions.
10) Cleaning Control
. This control allows the balance
of the AC wave to be altered so increasing or reducing
the cleaning effect when AC TIG welding.
11) Water flow failure indicator
This light illuminates
when the water flow is to low when using a water
cooled.
12) Torch selector switch
, when using a water cooled
TIG torch this switch should be in the WATER position,
in this position if the water flow is to low then the
indicator light (11) will illuminate and the welding
power with be cut off in order to prevent damage to
the torch. For use with a air cooled torch the switch
should be in the AIR position or the machine will not
operate
13) Post Gas,
this allows control of the post gas flow
at the end of a weld when in TIG mode. It is adjustable
from 3 to 10 seconds.
14) Downslope/Arc force.
This control is dual
function.
in TIG mode it controls the downslope time for the
welding current after the trigger is released from 0 to
10 seconds.
In MMA mode it allows adjustment of the welding Arc
force so giving control of penetration.
15) Amperage Display
. Displays the welding
amperage.
16) Main amperage control.
This control is used to
control the welding current in TIG and MMA modes.
17) Gas Output connection
This is a 3/8 BSP connection for the gas
output used in TIG welding.
18) Negative connection.
This is used to connect
the earth lead in MMA welding or the torch in TIG
welding.
19) Control socket
This is used to control the machine
remotely using a trigger or amperage control
20) Posative connection
This is used to connect the
electrode holder in MMA or the earth lead in TIG
welding.
21) Water out connection
for a water cooled TIG torch
5.0 Installation
Read entire installation section before starting
installation.
SAFETY PRECAUTIONS
• ELECTRIC SHOCK can kill.
• Only qualified personnel should perform this
installation.
• Only personnel that have read and understood the
Operating Manual should install and operate this
equipment.
• Machine must be grounded per any national, local
or other applicable electrical regulations.
• The power switch is to be in the OFF position when
installing work cable and electrode cable and when
connecting other equipment.
5.1 Unpacking the Machine
Carefully remove the machine from the packaging,
we recommend you retain the packaging until the
machine has been fully installed and tested incase it
has been damaged in transit and has to be returned to
the re-seller.
5.2 Location
Be sure to locate the welder according to the following
guidelines:
In areas, free from moisture and dust.
Ambient temperature between 0-40
0
C.
In areas, free from oil, steam and corrosive gases.
In areas, not subjected to abnormal vibration or shock.
In areas not exposed to direct sunlight or rain.
Place at a distance of 12” (300 mm) or more from
walls or similar that could restrict natural airflow for
cooling.
5.3 Input and grounding connection
WARNING
Before starting the installation, check that your
power supply is adequate for the voltage, amperage,
phase, and frequency specified on the Machine
nameplate.
Operate the welding power source from a 3-phase
50/60 Hz, AC power supply. The input voltage must
match one of the electrical input voltages shown
on the input data label on the unit nameplate. The
XTI-303 ACDC machine should only be used on 400V
supply. Refer to the specifications table for voltage
tolerances.
Have a qualified electrician connect the input plug.
For long runs over 30m , larger copper wires should
be used. The green/yellow wire in the input cable
connects to the frame of the machine. This ensures
proper grounding of the machine when the machine
plug is inserted into the receptacle.
5.4 Output Polarity Connections
Electrode polarity
MMA electrodes are generally connected to the ‘+’
terminal and the work lead to the ‘-‘terminal
But if in doubt consult the electrode manufacturer’s
literature.
IF TIG welding the torch should always be connected
to the ‘-’ terminal.
O
pera
tIO
n
Содержание XTI-303 AC/DC
Страница 1: ...INSTRUCTION MANUAL...
Страница 2: ...Operator Manual ISSUE 2 XTI 303 AC DC...