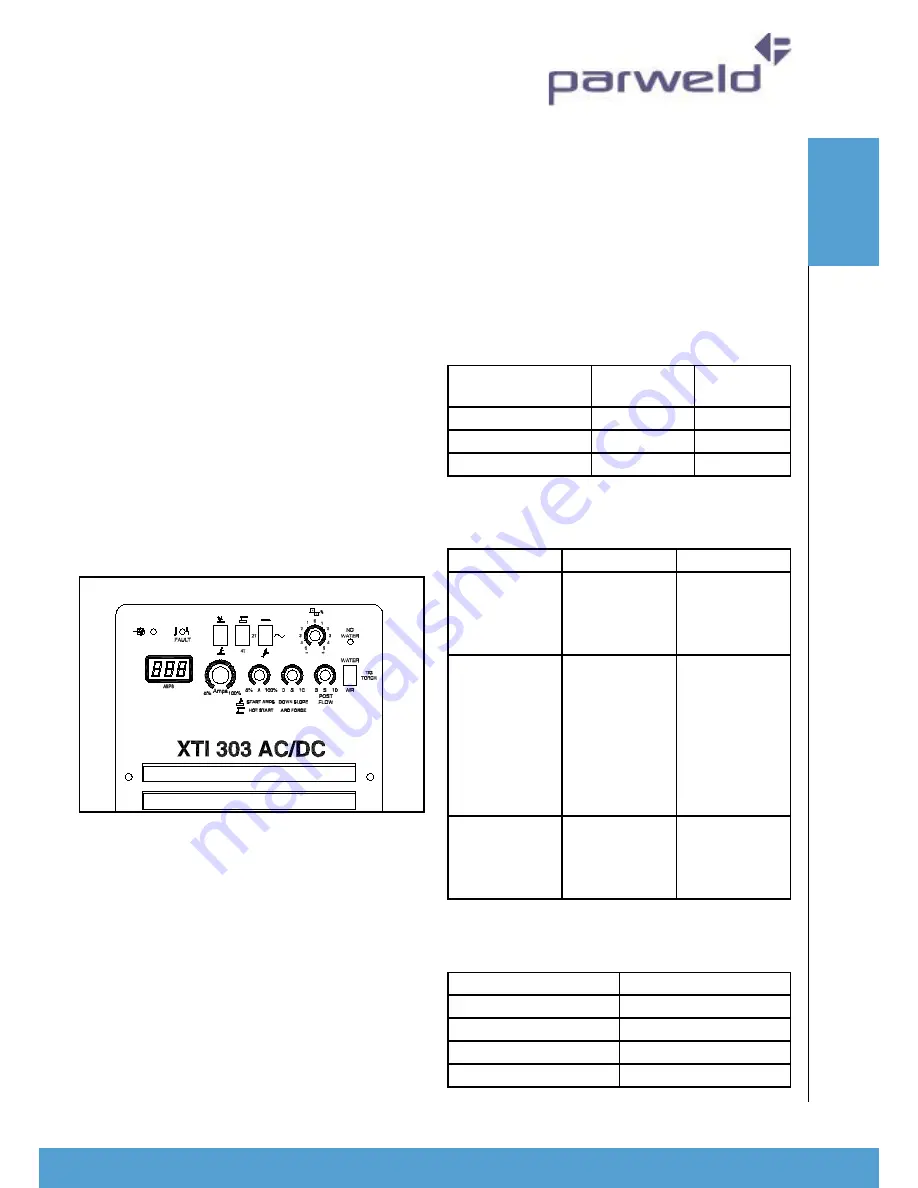
www.parweld.com
www.parweld.com
9
7014 all positional electrode for use on mild and
galvanized steel furniture, plates, fences, gates, pipes
and tanks etc. Especially suitable for vertical down
welding.
Cast iron
99% nickel suitable for joining all cast irons except
white cast iron
Stainless steel
318l-16 high corrosion resistance. Ideal for dairy work,
etc. On stainless steels.
6.2 TIG Welding guide
Tig welding cable connection
Connect the TIG torch to the - terminal and the work
lead to the + terminal for direct current straight
polarity. Direct current straight polarity is the most
widely used polarity for DC TIG welding. It allows
limited wear of the electrode since 70% of the heat is
concentrated at the work piece. Connect the gas hose
on the TIG torch to the gas outlet on the gas regulator.
O
pera
tIO
n
2
3
4
5
6
7
Torch starting in HF mode
Ensure the gas supply is switched on to the machine.
Select HF start on the front panel. Hold the torch with
the tip of the tungsten approx 2-3 mm from the job.
Depress the trigger to start the gas flow and switch on
the power. At the end of the weld release the torch
trigger and the power will slope down and switch off.
TIG welding guide ranges
Electrode diameter
AC current
(amps)
DC current
(amps)
0.040” (1.0mm)
15-30
20-60
1/16” (1.6mm)
60-120
75-150
3/32” (2.4mm)
100-180
150-250
Tungsten electrode types
Type
Application
Colour
Thoriated 2%
DC welding of
mild steel,
Stainless steel
and Copper
Red
Ceriated 2%
DC welding
of mild steel,
Stainless steel,
Copper
AC welding of
aluminium,
magnesium and
their alloys
Grey
Zirconiated
AC welding of
aluminium,
magnesium and
their alloys
White
Guide for selecting filler wire diameter
Filler wire diameter
Current range
1/16” (1.6 mm)
20 - 90
3/32” (2.4 mm)
65 - 115
1/8” (3.2 mm)
100 - 165
3/16” (4.8 mm)
200-350
1
Torch starting in Lift TIG mode
Ensure the gas supply is switched on to the machine.
Move the selector switch on the front panel of the
machine to the LIFT-TIG position. Briefly contact the
tip of the tungsten electrode down onto the work
piece with the torch at around 70
0
from vertical.
Depress the trigger to start the gas flow and switch
on the power, lift the torch up from the work piece to
draw out an arc. To prevent melting of the end of the
tungsten the machine will increase the output current
when it detects the rise in arc voltage as the tungsten
is lifted from the work piece. At the end of the weld
release the torch trigger and the power will slope
down and switch off.
8
Содержание XTI-303 AC/DC
Страница 1: ...INSTRUCTION MANUAL...
Страница 2: ...Operator Manual ISSUE 2 XTI 303 AC DC...