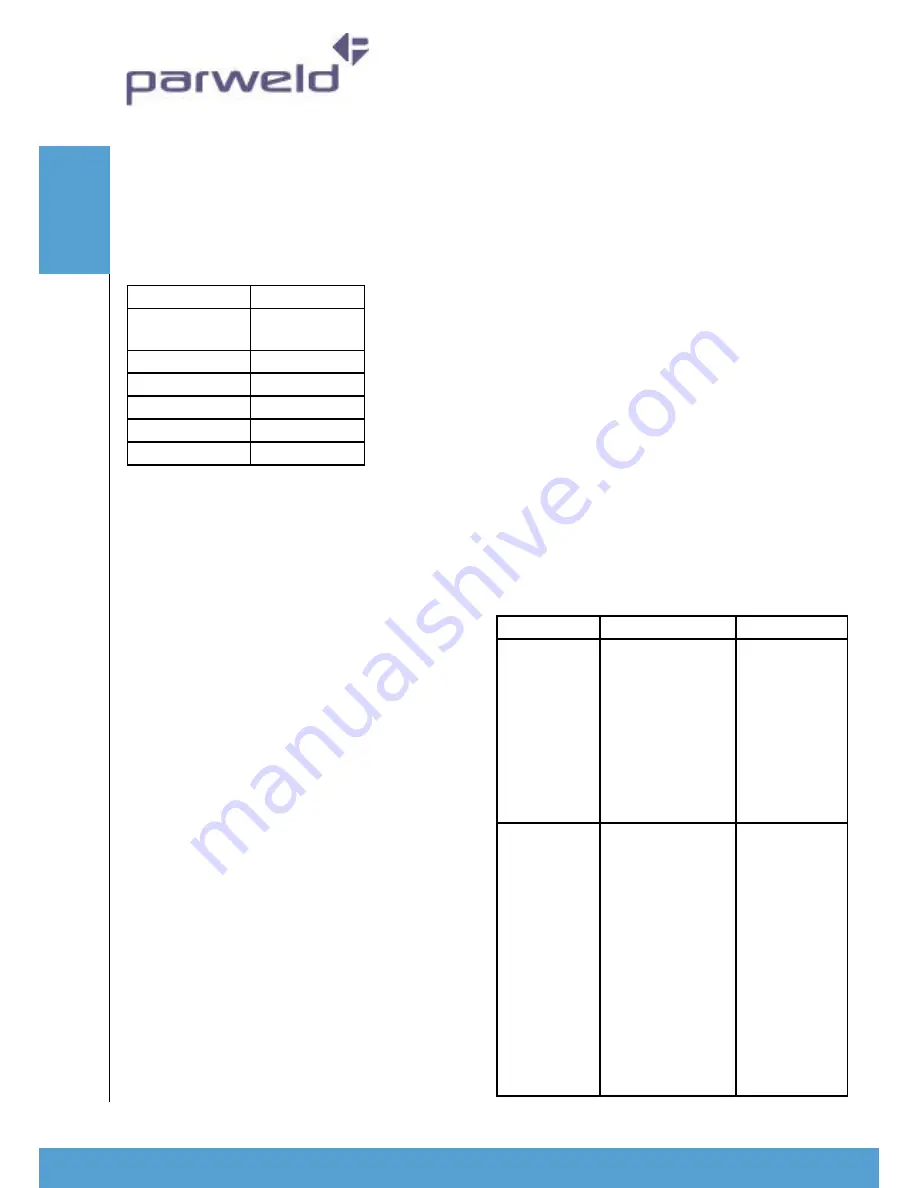
www.parweld.com
10
Faul
t
FI
n
DI
n
G
3) Select AC output from (centre position)
4) Dial up the welding amperage required
5) Set the starting amperage at 50%
6) Set the down slope at 5 seconds
7) Set the post gas at around 5 seconds
8) Set the cleaning control to 0.
You are now ready to weld. The above settings are
a guide and you should adjust to suit the job you are
welding if you are unfamiliar with the machine try to
adjust only one parameter at a time so you become
familiar with its effect. With AC TIG welding the
cleaning control is used to adjust the balance between
heating and cleaning the work, For speed an longevity
of the Tungsten it is best to minimise the cleaning
effect but how low this can be adjusted will depend
upon the condition of the base material
7.0 Fault Finding
MMA welding problem
Description
Possible cause
Remedy
Gas pockets
or voids in
weld metal
(porosity)
(a) Electrodes are
damp
(b) Welding current
is too high.
(c) Surface
impurities such as
oil, grease, paint,
etc
(a) Dry
electrodes
before use
(b) Reduce
welding current
(c) Clean joint
before welding
Crack occur-
ring in weld
metal soon
after solidifi-
cation.
(a) Rigidity of joint.
(b) Insufficient
throat thickness.
(c) Cooling rate is
too high.
(a) Redesign
to relieve weld
joint of severe
stresses or use
crack resistance
electrodes.
(b) Travel
slightly slower
to allow greater
build up in
throat.
(c) Preheat
plate and cool
slowly.
The filler wire diameter specified is a guide only, other
diameter wires may be used according to the welding
application.
Shielding gas selection
Alloy
Shielding gas
Aluminium &
alloys
Pure Argon
Carbon steel
Pure Argon
Stainless steel
Pure Argon
Nickel alloy
Pure Argon
Copper
Pure Argon
Titanium
Pure Argon
Machine setup for TIG welding
DC TIG welding
Connect the torch as detailed previously
1) Select HF start (bottom position)
2) Set the process mode to 2T or 4T if you prefer a
latching trigger action. (Note in 4T position you must
press and release to start the process and press and
release again to stop the process)
3) Select DC output from (top position)
4) Dial up the welding amperage required
5) Set the starting amperage at 50%
6) Set the down slope at 5 seconds
7) Set the post gas at around 5 seconds
You are now ready to weld. The above settings are a
guide and you should adjust to suit the job you are
welding if you are unfamiliar with the machine try to
adjust only one parameter at a time so you become
familiar with its effect.
AC TIG welding
Connect the torch as detailed previously
1) Select HF start (bottom position)
2) Set the process mode to 2T or 4T if you prefer a
latching trigger action. (Note in 4T position you must
press and release to start the process and press and
release again to stop the process)
Содержание XTI-303 AC/DC
Страница 1: ...INSTRUCTION MANUAL...
Страница 2: ...Operator Manual ISSUE 2 XTI 303 AC DC...