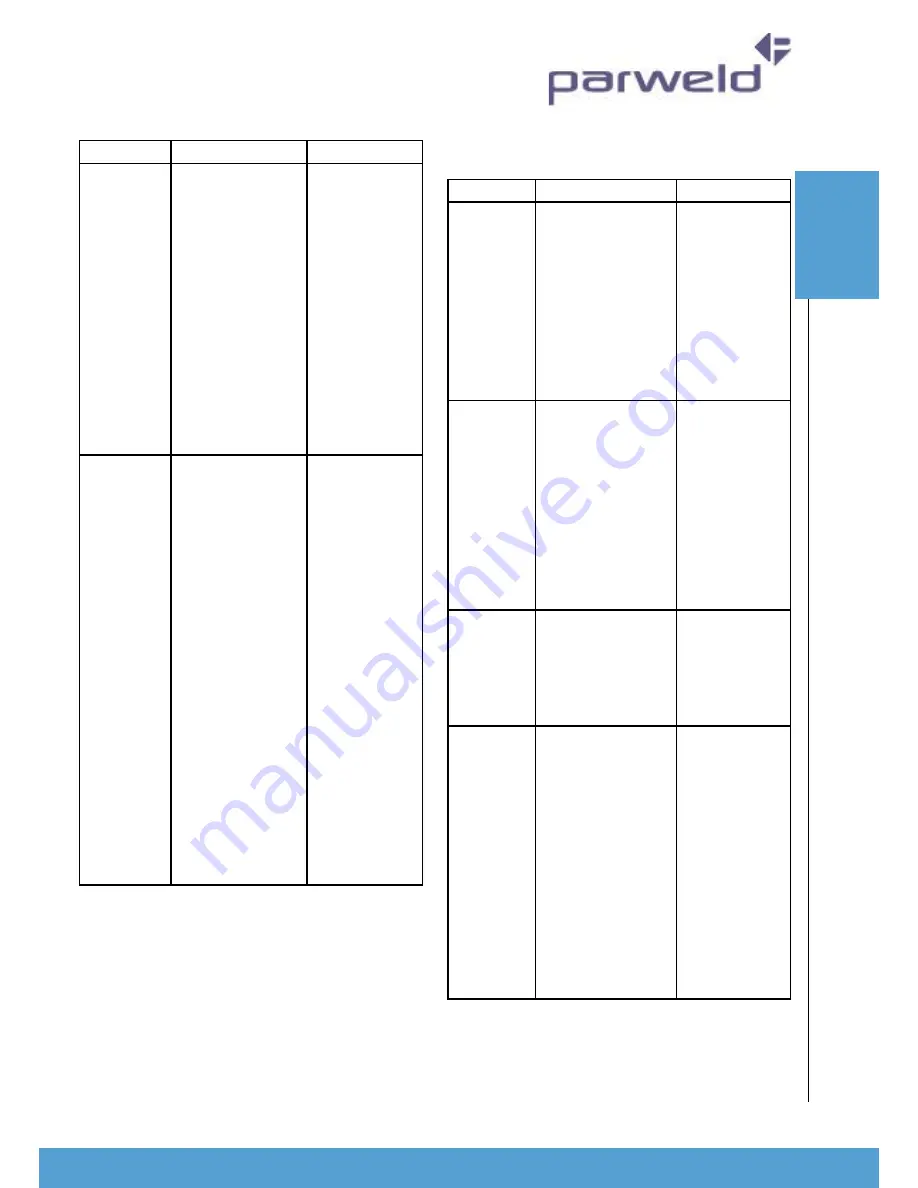
www.parweld.com
www.parweld.com
Description Possible Cause
Remedy
Welding arc
cannot be
established
(a) Work clamp is
not connected to
the work piece or
the work/torch
leads are not
connected to the
machine
(b) Torch lead is
disconnected
(c) Gas flow
incorrectly set,
cylinder empty or
the torch valve is
off
a) Connect the
work clamp to
the work piece
or connect the
work/torch
leads to the
right welding
terminals.
(b) Connect it to
the ‘.’ terminal.
(c) Select the
right flow
rate, change
cylinders or turn
torch valve on.
Arc start is
not smooth
(a) Tungsten
electrode is too
large for the
welding current .
(b) The wrong
electrode is being
used for the
welding job.
(c) Gas flow rate is
too high.
(d) Incorrect
shielding gas is
being used.
(e) Poor work
clamp connection
to work piece
(a) Select
the right size
electrode
(b) Select the
right electrode
type. Refer
to basic TIG
welding guide
(c) Select the
correct rate for
the welding job.
Refer to basic
TIG welding
guide
(d) Select the
right shielding
gas. Refer
to basic TIG
welding guide
(e) Improve
connection to
work piece
Power source problems
Description Possible cause
Remedy
The
welding arc
cannot be
established
(a) The primary
supply voltage has
not been switched
on
(b) The welding
power source switch
is switched off
(c) Loose
connections
internally
(a) Switch on
the primary
supply voltage
(b) Switch on
the welding
power source.
(c) Have a
qualified service
engineer repair
the connection
Maximum
output
welding
current
cannot be
achieved
with
nominal
mains
supply
voltage
Defective control
circuit
Have a qualified
service
engineer
inspect then
repair the
welder
Welding
current
reduces
when
welding
Poor work lead
connection to the
work piece
Ensure that
the work lead
has a reliable
electrical
connection to
the work piece
A total loss
of power,
pilot lamp
is off, no
output, the
fan is not
operating
(a) Failure of input
voltage
(b) Possible over
voltage
(c) Internal fault
with the machine
(a) Re-establish
mains supply
(b) Check
voltage and
if necessary
move machine
to alternative
supply
(c) Have a
qualified service
engineer
inspect then
repair the
welder
Faul
t
FI
n
DI
n
G
13
Содержание XTI-303 AC/DC
Страница 1: ...INSTRUCTION MANUAL...
Страница 2: ...Operator Manual ISSUE 2 XTI 303 AC DC...