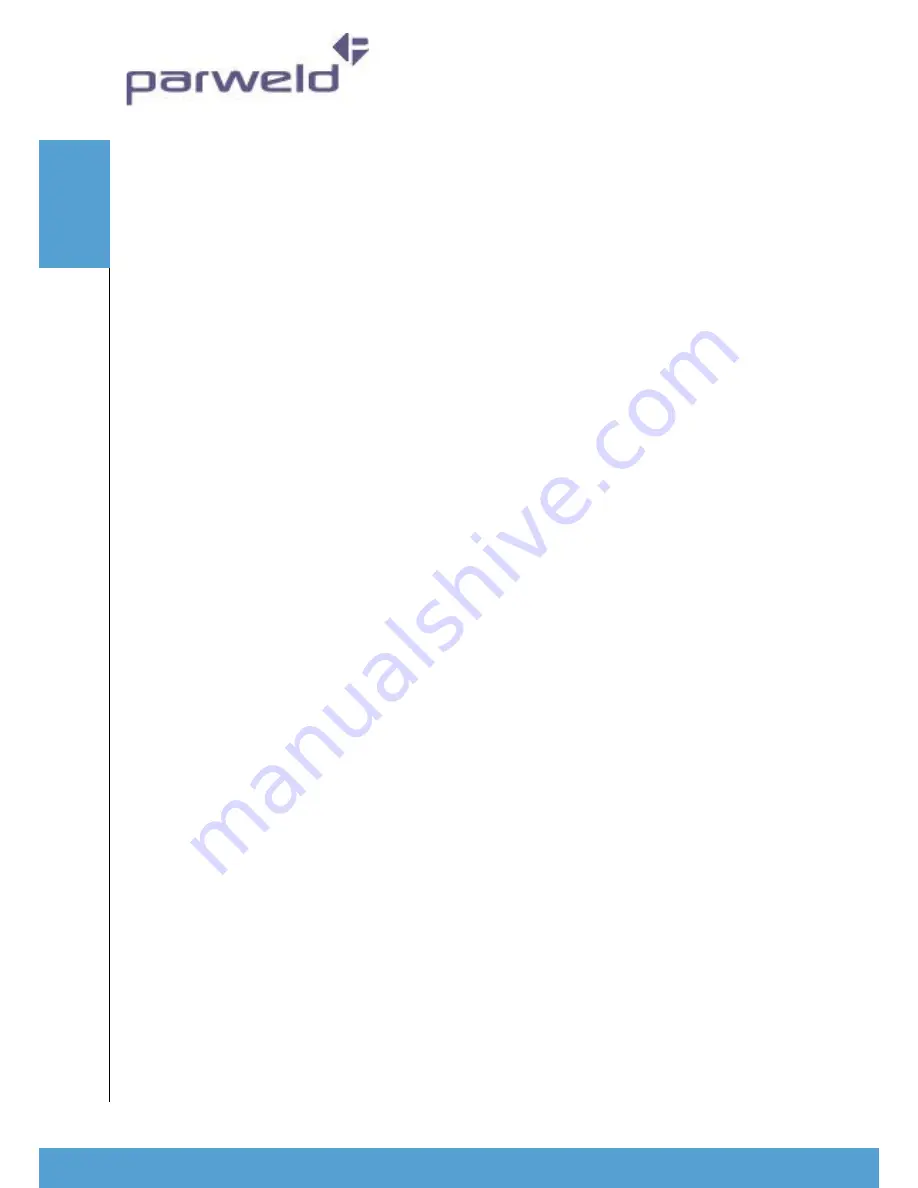
www.parweld.com
4
1.0 Safety Precautions
ELECTRIC SHOCK can kill.
Touching live electrical parts can cause fatal shocks
or severe burns. The electrode and work circuit is
electrically live whenever the output is on. The input
power circuit and machine internal circuits are also
live when power is on.
Do not touch live electrical parts.
Wear dry, sound insulating gloves and body
protection.
Insulate yourself from work and ground using dry
insulating mats or covers big enough to prevent any
physical contact with the work ground.
Additional safety precautions are required when any
of the following electrically hazardous conditions
are present: in damp locations or while wearing wet
clothing; on metal structures such as floors, gratings,
or scaffolds; when in cramped positions such as
sitting, kneeling, or lying; or when there is a high risk
of unavoidable or accidental contact with the work
piece or ground.
Disconnect input power before installing or servicing
this equipment. Lockout/tagout input power according
to Safety Standards.
Properly install and ground this equipment according
to national and local standards.
Always verify the supply ground - check and ensure
that input power cable ground wire is properly
connected to ground terminal in the receptacle outlet.
When making input connections, attach proper
grounding conductor first - double-check connections.
Frequently inspect input power cable for damage or
bare wiring - replace cable immediately if damaged -
bare wiring can kill.
Turn off all equipment when not in use.
Do not use worn, damaged, under sized, or poorly
spliced cables.
Do not drape cables over your body.
If earth grounding of the work piece is required,
ground it directly with a separate cable.
Do not touch electrode if you are in contact with the
work, ground, or another electrode from a different
machine.
Use only well-maintained equipment. Repair or
replace damaged parts at once. Maintain unit
according to manual.
Wear a safety harness if working above floor level.
Keep all panels and covers securely in place.
Clamp work cable with good metal-to-metal contact to
work piece or worktable as near the weld as practical.
Insulate work clamp when not connected to work
piece to prevent contact with any metal object.
Welding produces fumes and gases. Breathing these
fumes and gases can be hazardous to your health.
FUMES AND GASES can be hazardous.
Keep your head out of the fumes. Do not breathe the
fumes.
If inside, ventilate the area and/or use local forced
ventilation at the arc to remove welding fumes and
gases.
If ventilation is poor, wear an approved respirator.
Read and understand the Material Safety Data Sheets
(MSDS’s) and the manufacturer’s instructions for
metals, consumable, coatings, cleaners, and de-
greasers.
Work in a confined space only if it is well ventilated,
or while wearing an air-supplied respirator. Always
have a trained watch person nearby. Welding fumes
and gases can displace air and lower the oxygen level
causing injury or death. Be sure the breathing air is
safe.
Do not weld in locations near de-greasing, cleaning, or
spraying operations. The heat and rays of the arc can
react with vapours to form highly toxic and irritating
gases.
Do not weld on coated metals, such as galvanized,
lead, or cadmium plated steel, unless the coating
is removed from the weld area, the area is well
ventilated, and while wearing an air-supplied
respirator. The coatings and any metals containing
these elements can give off toxic fumes if welded.
ARC RAYS can burn eyes and skin.
Arc rays from the welding process produce intense,
visible and invisible (ultraviolet and infrared) rays that
can burn eyes and skin. Sparks fly off from the weld.
Wear an approved welding helmet fitted with a proper
shade of filter lense to protect your face and eyes
when welding or watching
Wear approved safety glasses with side shields under
your helmet.
Use protective screens or barriers to protect others
from flash, glare and sparks; warn others not to watch
the arc.
Wear protective clothing made from durable, flame
Sa
Fet
Y
Содержание XTI-303 AC/DC
Страница 1: ...INSTRUCTION MANUAL...
Страница 2: ...Operator Manual ISSUE 2 XTI 303 AC DC...