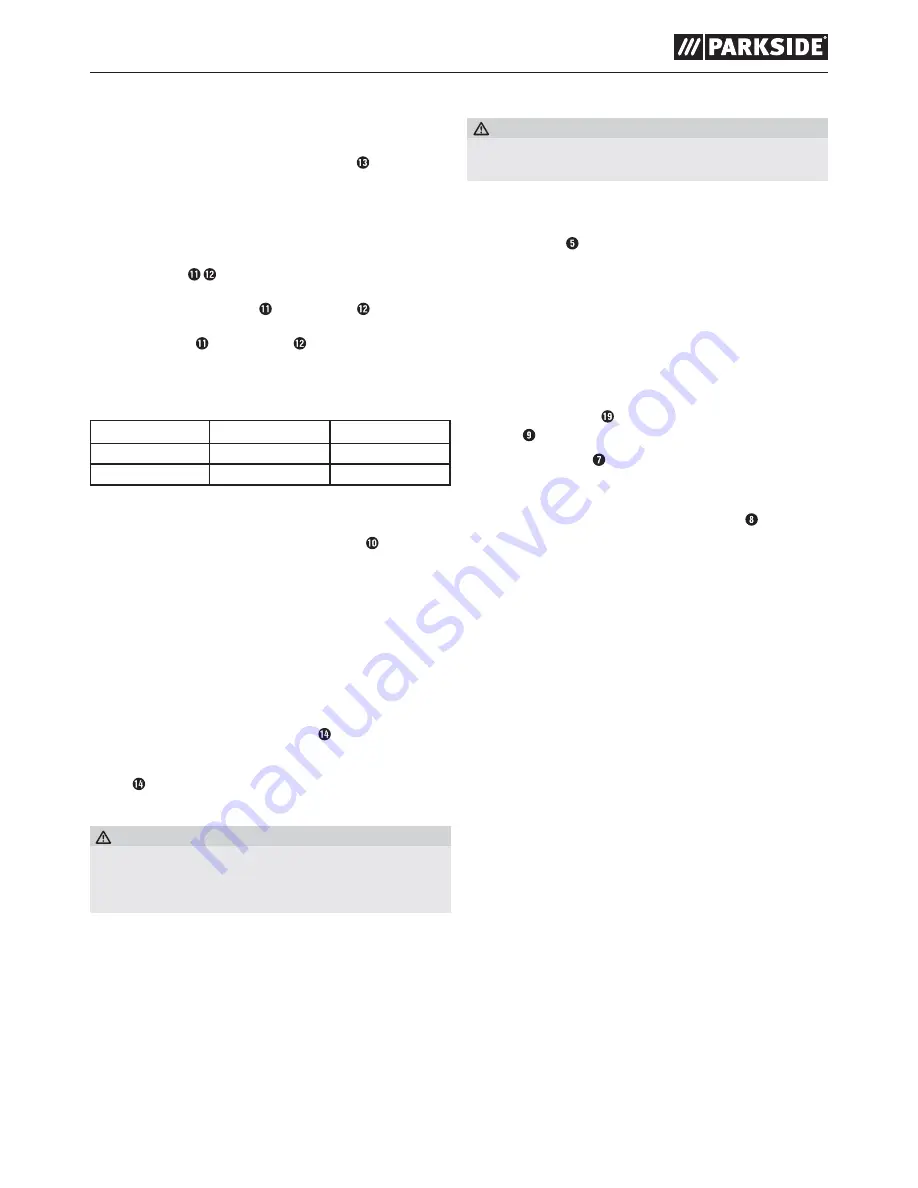
GB
│
IE
│
NI
│
11
■
PFDS 33 A1
Operation
Switching the appliance on and off
♦
Switch the welder on and off using the main switch .
If you do not intend to use the welder for an extended period, remove the
plug from the power socket. This is the only way to completely de-energise
the appliance.
Setting the welding current
■
Use the switches on the front of the welder to set the required
welding current.
■
If, for example, the
MIN
switch und the switch
1
are set to the
up position, the welding current is 48 A and the duty cycle is at 60%.
■
If the
MAX
switch und the switch
2
are set to the down position,
the welding current is 90 A and the duty cycle is at 10%.
■
The required welding current is dependent on the diameter of the welding
wire being used, the material thickness and the desired penetration
depth.
MIN
MAX
1
48 A
70 A
2
60 A
90 A
Adjusting the wire feed
■
To achieve a consistent weld result, you can make fine adjustments to
the wire feed using the setting wheel for the wire feed .
We recommend using a setting in the middle range to start with and
then increasing or reducing the speed as required.
■
The required welding flow is dependent on the diameter of the welding
wire being used, the material thickness and the desired penetration
depth as well as the bridging distance between the two pieces being
welded.
Overload protection
■
The welder is protected against overheating by an automatic protection
appliance (thermostat with automatic restart) metal clad. The protection
appliance interrupts the power supply in the event of an overload and
the yellow overload protection control lamp lights up.
■
If the protection appliance activates, allow the appliance to cool down
(approx. 15 minutes). As soon as the yellow overload protection control
lamp goes off, the appliance is again ready for use.
Welding mask
WARNING! HEALTH HAZARD!
►
If you do not use the welding mask, the harmful UV radiation and the
heat coming from the electric arc can damage your eyes.
–
Always use the welding mask when you weld.
Welding
WARNING! RISK OF BURNS!
►
Welded, hot workpieces are very hot so that you could burn yourself.
–
Always use pliers to move welded, hot workpieces.
After you have connected the welder to the power, proceed as follows:
♦
Connect the earth cable to the workpiece that is to be welded using
the earth clamp .
Ensure that there is a good electrical connection.
♦
The workpiece should be free of rust and paint where the weld is to
made.
♦
Select the desired welding current and the wire feed depending on
the welding wire diameter, material thickness and desired penetration
depth.
♦
Switch the appliance on.
♦
Hold the welding mask in front of your face and guide the torch
nozzle to the position on the workpiece where you want to weld.
♦
Press the torch button to generate an electric arc.
Once the electric arc is burning, the appliance feeds wire into the weld
pool.
♦
Once the weld nugget is big enough, guide the torch slowly along
the desired edge.
The distance between the torch nozzle and the workpiece should be
as small as possible (never more than 10 mm).
♦
If required, oscillate a little to increase the size of the weld pool.
For inexperienced welders, it is often difficult initially to create a decent
electric arc, i.e. in terms of the correct setting of welding current and wire
feed rate.
♦
You can work out the ideal settings for the welding current and the
wire feed rate by carrying out trial welds on a test piece.
A properly set electric arc has a mild, uniform buzzing tone.
The penetration depth should be as deep as possible, the weld pool,
however, should not be able to fall through the workpiece.
If you hear a raw or hard rattle, reduce the wire feed rate and switch
up to a higher load level (increase the welding current).
If the wire feed rate is too high and/or the welding current too low, the
welding wire cannot melt properly and dips repeatedly into the weld
bed as far as the workpiece.
A quiet dull sound with a guttering electric arc indicates that the wire
feed is insufficient.
♦
Increase the wire feed rate or switch to a lower welding current.
If the welding current is too high, the wire will melt before it even
reaches the weld bed. This leads to droplet formation on the welding
wire as well as splash and an irregular electric arc.
♦
The slag may not be removed until the weld has cooled down.
To resume a weld on an interrupted joint:
♦
Start by removing the slag at the starting point.
♦
Ignite the electric arc in the groove, guide it to the continuation point,
melt properly and then continue the weld joint.
Содержание PFDS 33 A1
Страница 3: ...A B ...
Страница 4: ...C D E F ...