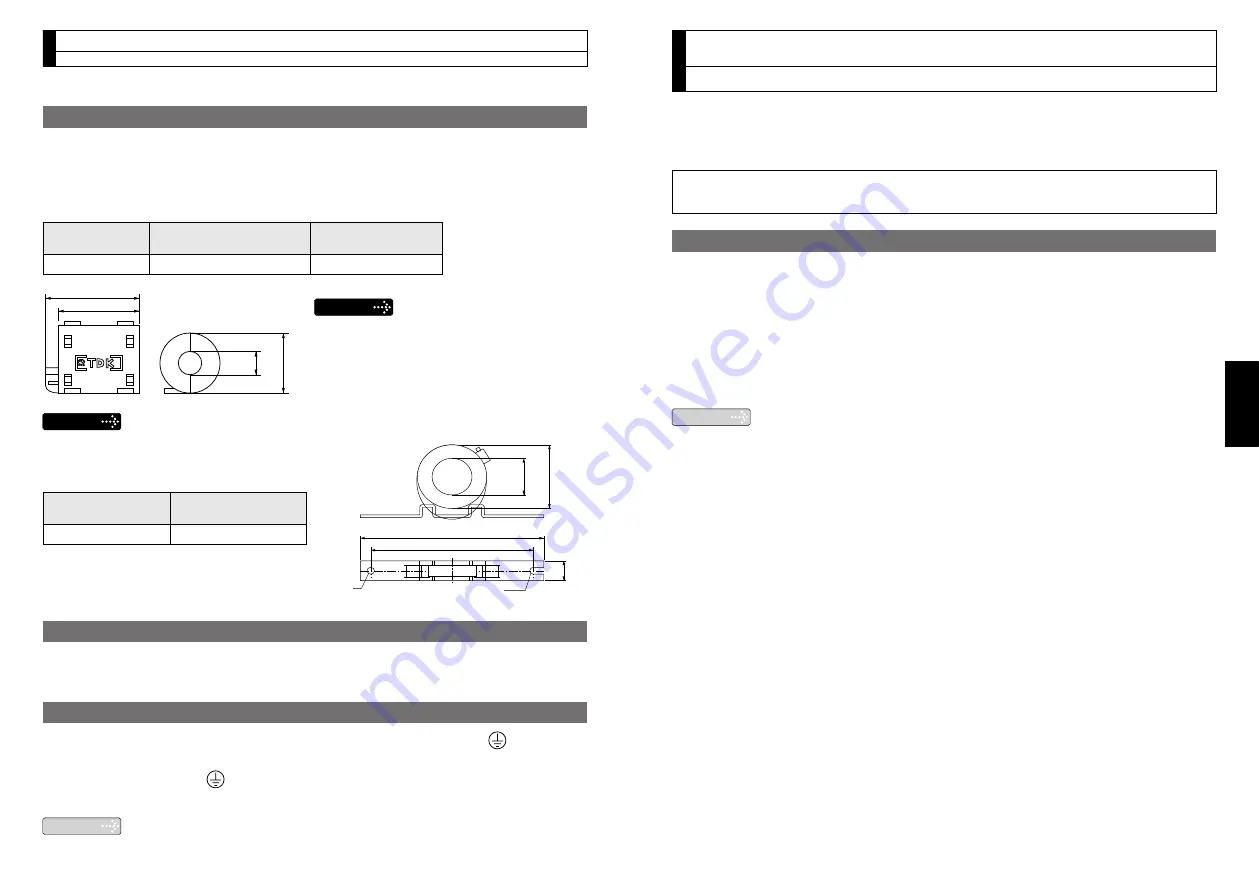
−
B43
−
−
B42
−
English
8. Built-in Holding Brake
Outline / Specifications
In the applications where the motor drives the vertical axis, this brake would be used
to hold and prevent the work (moving load) from falling by gravity while the power to
the servo is shut off.
Use this built-in brake for "Holding" purpose only, that is to hold the stalling
status. Never use this for "Brake" purpose to stop the load in motion.
Output Timing of BRK-OFF Signal
• For the brake release timing at power-on, or braking timing at Servo-OFF/Servo-
Alarm while the motor is in motion, refer to the Operating Instructions (Overall).
• With the parameter, Pr4.38 (Setup of mechanical brake action while the motor is in
motion), you can set up a time between when the motor enters to a free-run from
energized status and when BRK-OFF signal turns off (brake will be engaged), when
the Servo-OFF or alarm occurs while the motor is in motion. Refer to the Operating
Instructions (Overall) for the details.
Note
1. The lining sound of the brake (chattering and etc.) might be generated
while running the motor with built-in brake, however this does not af-
fect any functionality.
2. Magnetic flux might be generated through the motor shaft while the
brake coil is energized (brake is open). Pay an extra attention when
magnetic sensors are used nearby the motor.
Noise Filter for Signal Lines
Install noise filters for signal lines to all cables (power cable, motor cable, encoder
cable and interface cable)
• Optional parts
<24 V Power cable, Encoder cable, Interface cable and USB cable>
Option part No.
Manufacturer’s
part No.
Manufacturer
DV0P1460
ZCAT3035-1330
TDK Corp.
39
±
1
34
±
1
30
±
1
13
±
1
Mass: 62.8 g
[Unit: mm]
Remarks
To connect the noise filter to
the connector XB
connection cable, adjust the
sheath length at the tip of
the cable, as required.
Caution
Fix the signal line noise filter in order to prevent excessive stress to the
cables.
• Recommended components
<Power cable>
Manufacturer’s
part No.
Manufacturer
RJ8035
KK-CORP.CO.JP
Residual current device
Install a residual current device (RCD) at primary side of the power supply.
Select a RCD of type.B prescribed in IEC60947-2, JISC8201-2-2.
Grounding
(1) To prevent electric shock, be sure to connect the ground terminal (
) of the driv-
er, and the ground terminal (PE) of the control panel.
(2) The ground terminal (
) must not be shared with other equipment. Two ground
terminals are provided.
Note
For driver and applicable peripheral equipments, refer to P.B12 "Driver
and List of Applicable Peripheral Equipments" .
7. Conformity to EC Directives and UL Standards
Composition of Peripheral Equipments
[Unit: mm]
180
200
34
130
7
R3.5
107