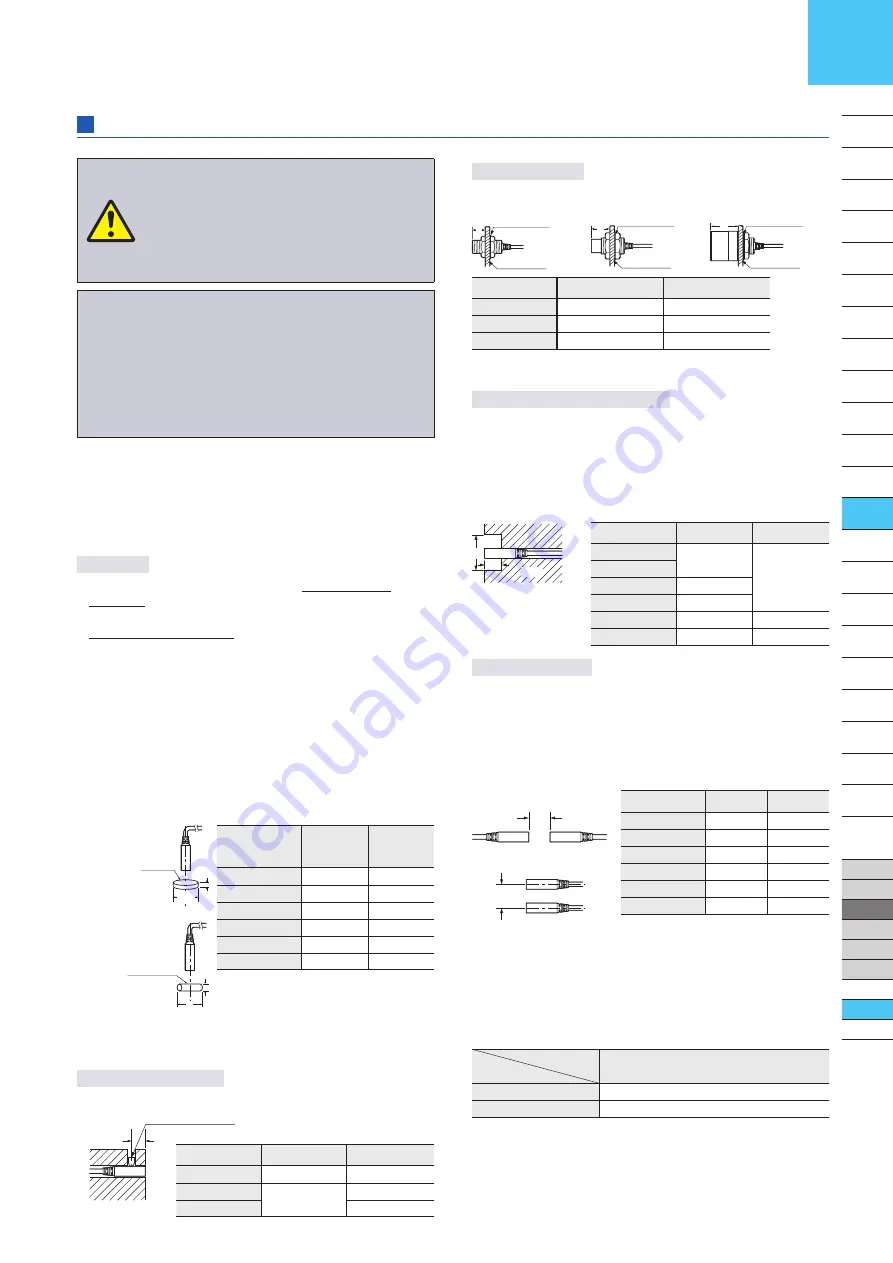
High Speed High Accuracy Eddy Current Type Digital Displacement Sensor
GP-X
SERIES
1032
FIBER
SENSORS
LASER
SENSORS
PHOTO-
ELECTRIC
SENSORS
MICRO
PHOTO-
ELECTRIC
SENSORS
AREA
SENSORS
LIGHT
CURTAINS
PRESSURE /
FLOW
SENSORS
INDUCTIVE
PROXIMITY
SENSORS
PARTICULAR
USE
SENSORS
SENSOR
OPTIONS
SIMPLE
WIRE-SAVING
UNITS
WIRE-SAVING
SYSTEMS
MEASURE-
MENT
SENSORS
STATIC
CONTROL
DEVICES
ENDOSCOPE
LASER
MARKERS
PLC /
TERMINALS
HUMAN
MACHINE
INTERFACES
ENERGY
CONSUMPTION
VISUALIZATION
COMPONENTS
FA
COMPONENTS
MACHINE
VISION
SYSTEMS
UV
CURING
SYSTEMS
Selection
Guide
Laser
Displacement
Magnetic
Displacement
Collimated
Beam
Digital Panel
Controller
Metal-sheet
Double-feed
Detection
GP-X
GP-A
Mounting with nut
• The sensor head and the controller are adjusted in order
to conform to the default specification linearity.
• In the event of replacing sensor heads, input the sensor
head’s characteristic code and conduct 3-point correction
(calibration).
• Should you use an extension cable, turn the sensor head cable
length selection switch located on the back of the controller
to “3 m + 7 m
9.843 ft
+ 22.966 ft
”. Then reintroduce the
power supply and conduct 3-point correction (calibration).
Conditions in use for CE conformity
• This product is CE compliant and complies with EMC
directives. EN 61000-6-2 is the applicable standard
that covers immunities relating to use of this product,
but in order to comply with this standard, the following
conditions must be satisfied.
Conditions
• The controller should be connected less than 10 m
32.808
ft
from the power supply.
• The signal line to connect with the controller should be
less than 30 m
98.425 ft
.
• A ferrite clamp must be mounted within 10 mm
0.394
in
from connector fitted onto the
GP-XBCC3
cable with
connector on one end for BCD output units.
Linearity in case of disc-shaped or cylindrical objects
• In case the sensing object is disc-shaped or cylindrical,
the linearity varies with the sensing object size.
In the event the sensing object is larger than the sizes
indicated in the table below, the linearity specification
(within ±0.3 % F.S.) is satisfied by performing zero-
adjustment and span adjustment when in contact using
the scaling function.
<In case of disc>
Sensor head Disc diameter
ø (mm
in
)
Cylinder diameter
ø (mm
in
)
GP-X3SE
6
0.236
16
0.630
GP-X5SE
8
0.315
16
0.630
GP-X8S
12
0.472
50
1.969
GP-X10M
12
0.472
50
1.969
GP-X12ML
25
0.984
55
2.165
GP-X22KL
30
1.181
165
6.496
t
t: 1 mm
0.039 in
Iron disc
ø mm
in
( )
<In case of cylinder>
Iron cylinder
ø (mm
in
)
ℓ: 135 mm
5.315 in
ℓ
Mounting sensor head
• The tightening torque should be under the value given below.
A
Set screw (M3 or less)
(Cup-point)
Model No.
A (mm
in
)
Tightening torque
GP-X3SE
4 to 16
0.157 to 0.630
0.10 N·m or less
GP-X5SE
5 to 16
0.197 to 0.630
0.44 N·m or less
GP-X8S
0.58 N·m or less
Mounting with set screw
• Make sure to use an M3 or smaller set screw having a cup-point.
<GP-X10M>
<GP-X12ML>
<GP-X22KL>
B
Attached toothed
lock washer
Mounting plate
B
Mounting plate
Attached toothed
lock washer
B
Mounting plate
Attached toothed
lock washer
Model No.
B (mm
in
)
Tightening torque
GP-X10M
7
0.276
or more
9.8 N·m or less
GP-X12ML
14
0.551
or more
20 N·m or less
GP-X22KL
20
0.787
or more (Note 1)
20 N·m or less
Notes: 1) Without nut. If a nut is installed, the dimension will be 23.5 mm
0.926 in
or more.
2) Mount such that the nuts do not protrude from the threaded portion.
Distance from surrounding metal
• As metal around the sensor head may affect the sensing
performance, pay attention to the following points.
<Embedding of the sensor head in metal>
• Since the analog output may change if the sensor head
is completely embedded in metal, keep the minimum
distance specified in the table below.
D
C
Metal
Sensor head
C (mm
in
)
D (mm
in
)
GP-X3SE
ø10
ø0.394
3
0.118
GP-X5SE
GP-X8S
ø18
ø0.709
GP-X10M
ø14
ø0.551
GP-X12ML
ø50
ø1.969
14
0.551
GP-X22KL
ø50
ø1.969
20
0.787
Mutual interference
• If several sensor heads are mounted close together, some specifications may
not be satisfied. Therefore, proceed with the interference prevention function
enabled.
The interference prevention function eliminates interference among sensors by
alternating sensor oscillations. Contact our office for details about time charts etc.
If not using the interference prevention function, leave a distance more than the
values given below.
PRECAUTIONS FOR PROPER USE
Refer to General precautions.
Others
• After turning on the power, wait 15 min. or more [20 min.for the
GP-XC3SE
(
-P
) and
GP-XC5SE
(
-P
)] before usingthe product.
The power supply circuit is not stable immediately after the power is
turned on, and this may cause measurement values to be distorted. In
addition, note that there will also be a muting period of approx. 2 sec.
<Face to face mounting>
E
<Parallel mounting>
F
Sensor head
E (mm
in
) F (mm
in
)
GP-X3SE
15
0.591
9
0.354
GP-X5SE
30
1.181
11
0.433
GP-X8S
40
1.575
15
0.591
GP-X10M
40
1.575
15
0.591
GP-X12ML
170
6.693
50
1.969
GP-X22KL
200
7.874
200
7.874
Sensing range
• The sensing range is specified for the standard sensing object [stainless steel
(SUS304) / iron [Cold rolled carbon steel (SPCC)], 60 × 60 × t 1 mm
2.362 × 2.362 ×
t 0.039 in
]. For sensing metals other than the standard sensing objects, use the
correction coefficient stated below as a guideline. Verify with the actual sensor
before using.
Sensor head
GP-X3SE GP-X5SE GP-X8S
GP-X10M GP-X12ML GP-X22KL
Metal
Stainless steel (SUS304), Iron
1
Aluminum
0.5 approx.
Correction coefficient
• Never use this product as a sensing device
for personnel protection.
• In case of using sensing devices for
personnel protection, use products which
meet laws and standards, such as OSHA,
ANSI or IEC etc., for personnel protection
applicable in each region or country.