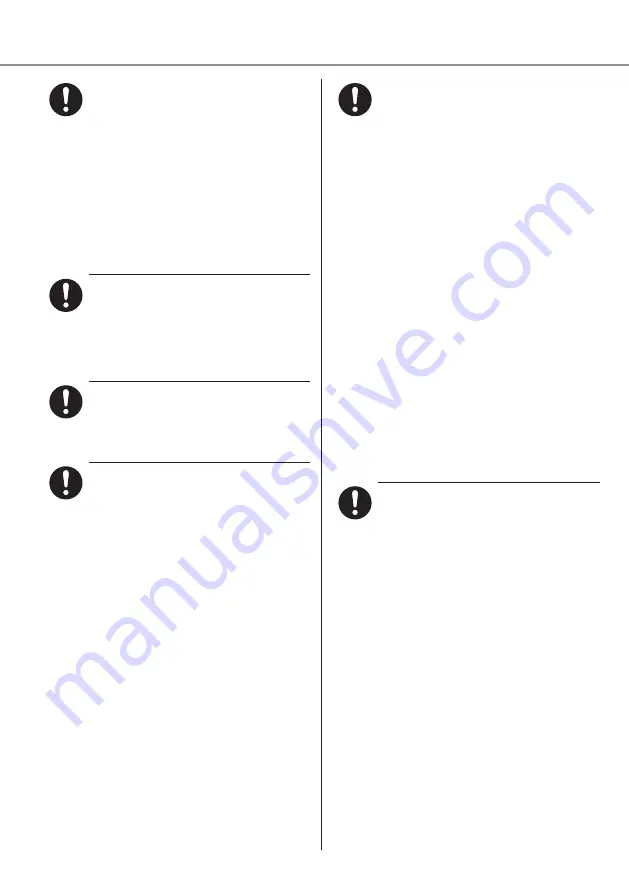
8
4. Repair to intrinsically safe components
• Do not apply any permanent inductive or
capacitance loads to the circuit without
ensuring that this will not exceed the
permissible voltage and current permitted for
the equipment in use.
• Intrinsically safe components are the only
types that can be worked on while live in the
presence of a fl ammable atmosphere.
• The test apparatus shall be at the correct
rating.
• Replace components only with parts
specifi ed by the manufacturer. Unspecifi ed
parts by manufacturer may result ignition of
refrigerant in the atmosphere from a leak.
5. Cabling
• Check that cabling will not be subject
to wear, corrosion, excessive pressure,
vibration, sharp edges or any other adverse
environmental effects.
• The check shall also take into account the
effects of aging or continual vibration from
sources such as compressors or fans.
6. Detection of
fl
ammable refrigerants
• Under no circumstances shall potential
sources of ignition be used in the searching
or detection of refrigerant leaks.
• A halide torch (or any other detector using a
naked fl ame) shall not be used.
7. Leak detection methods
• Electronic leak detectors shall be used
to detect fl ammable refrigerants, but the
sensitivity may not be adequate, or may
need re-calibration.
(Detection equipment shall be calibrated in a
refrigerant-free area.)
• Ensure that the detector is not a potential
source of ignition and is suitable for the
refrigerant used.
• Leak detection equipment shall be set at
a percentage of the LFL of the refrigerant
and shall be calibrated to the refrigerant
employed and the appropriate percentage of
gas (25 % maximum) is confi rmed.
• Leak detection fl uids are suitable for use with
most refrigerants but the use of detergents
containing chlorine shall be avoided as the
chlorine may react with the refrigerant and
corrode the copper pipe-work.
• If a leak is suspected, all naked fl ames shall
be removed/extinguished.
• If a leakage of refrigerant is found which
requires brazing, all of the refrigerant shall
be recovered from the system, or isolated
(by means of shut off valves) in a part of the
system remote from the leak. Oxygen free
nitrogen (OFN) shall then be purged through
the system both before and during the
brazing process.
8. Removal and evacuation
• When breaking into the refrigerant circuit to make
repairs – or for any other purpose – conventional
procedures shall be used.
However, it is important that best practice is
followed since fl ammability is a consideration.
The following procedure shall be adhered to:
remove refrigerant -> purge the circuit with inert
gas -> evacuate -> purge again with inert gas ->
open the circuit by cutting or brazing
• The refrigerant charge shall be recovered into
the correct recovery cylinders.
• The system shall be “fl ushed” with OFN to
render the unit safe.
• This process may need to be repeated several times.
• Compressed air or oxygen shall not be used
for this task.
• Flushing shall be achieved by breaking the
vacuum in the system with OFN and continuing
to fi ll until the working pressure is achieved,
then venting to atmosphere, and fi nally pulling
down to a vacuum.
• This process shall be repeated until no
refrigerant is within the system.
• When the fi nal OFN charge is used, the system
shall be vented down to atmospheric pressure
to enable work to take place.
• This operation is absolutely vital if brazing
operations on the pipe work are to take place.
• Ensure that the outlet for the vacuum pump is
not close to any ignition sources and there is
ventilation available.
9. Charging procedures
• In addition to conventional charging procedures,
the following requirements shall be followed.
-Ensure that contamination of different
refrigerants does not occur when using
charging equipment.
-Hoses or lines shall be as short as possible to
minimize the amount of refrigerant contained
in them.
-Cylinders shall be kept upright.
-Ensure that the refrigeration system is earthed
prior to charging the system with refrigerant.
-Label the system when charging is complete
(if not already).
-Extreme care shall be taken not to over fi ll the
refrigeration system.
• Prior to recharging the system it shall be
pressure tested with OFN (refer to #7).
• The system shall be leak tested on completion
of charging but prior to commissioning.
• A follow up leak test shall be carried out prior to
leaving the site.
• Electrostatic charge may accumulate and
create a hazardous condition when charging
and discharging the refrigerant.
To avoid fi re or explosion, dissipate static
electricity during transfer by grounding and
bonding containers and equipment before
charging/discharging.
Safety precautions
Содержание CS/CU-HU12ZKY Series
Страница 15: ...Note 15 English Troubleshooting...