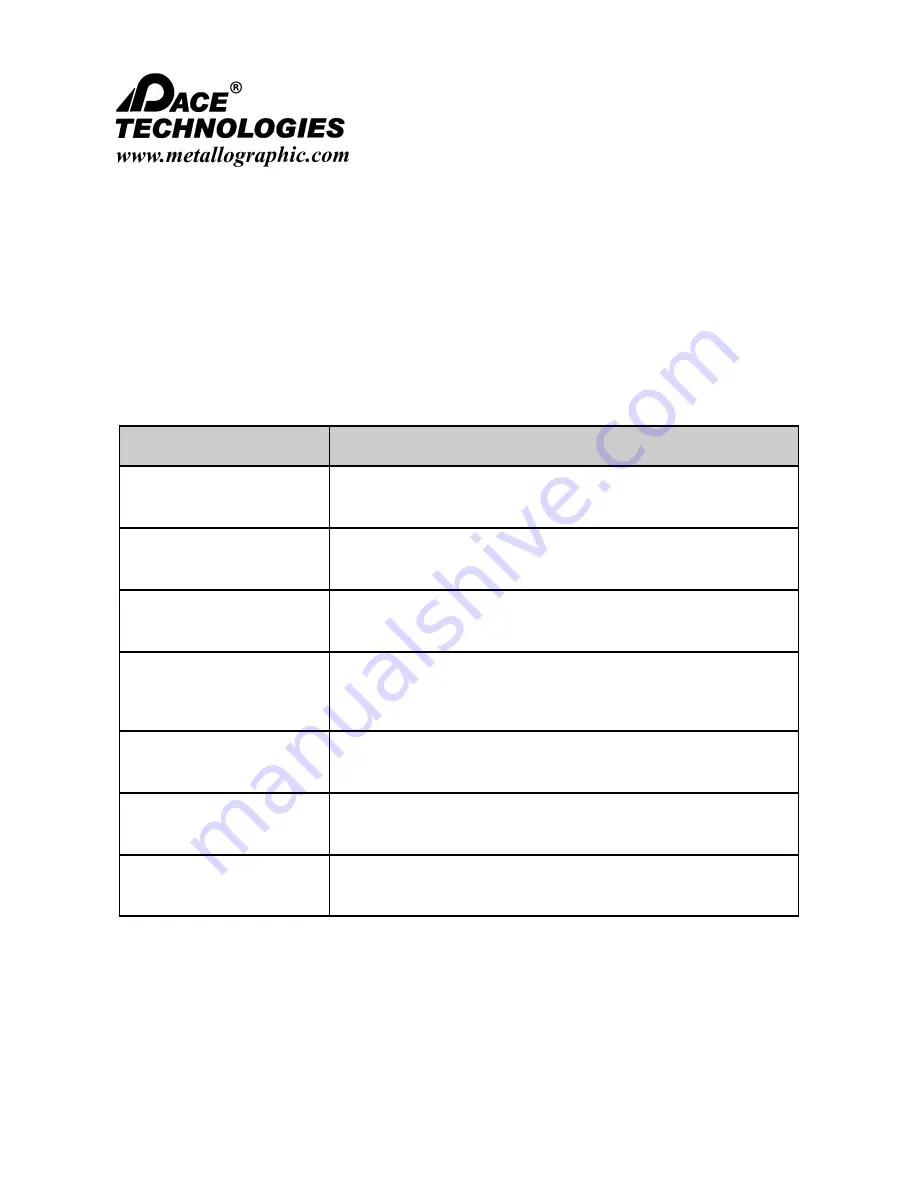
- - - - - - - - - - - - - - - - - - - - - - - - - - - - - - - - - - - - - - - - - - - - - - - - - - ▲
I
NSTRUCTION
M
ANUAL
3601 E. 34th St. Tucson, AZ 85713 USA Tel. +1 520-882-6598 Fax +1 520-882-6599 email: [email protected] Web: http://www.metallographic.com
33
Please read this instruction manual carefully and follow all installation, operating and safety guidelines.
NANO 1000T / FEMTO 1500
Polishing Head
The purpose of final polishing is to remove only the cosmetic surface damage. It should not be used
to remove any damage remaining from cutting and planar grinding. If the damage from these steps is
not completely removed, the rough polishing step should be repeated or continued.
5.10.3 Final Polishing
Material
Recommendation
Metals (ferrous, non-
ferrous, tool steels, super
alloys, etc.)
High-napped polishing pads with a nanometer alumina polishing
abrasive. The polishing times should nominally be less than 30
seconds.
Ceramics and ceramic
matrix composites (CMC)
Low-napped polishing pads using 1-um polycrystalline diamond,
alternating with colloidal silica or colloidal silica alone.
Polymer matrix composites
(PMC)
Fine abrasive diamond-lapping films, followed by a very light polish
on a high-napped polishing pad.
Biomaterials
Low-napped polishing pads with polycrystalline diamond, alternating
with colloidal silica.
Microelectronic specimens
Diamond-lapping films followed by a very light polish on a
high-napped polishing pad.
Plastics and polymers
Light polish with alumina on a high-napped polishing pad.
Plasma spray materials
Diamond-lapping films followed by a very light and short alumina or
colloidal silica polish on a high-napped polishing pad.
Final Polishing Guidelines