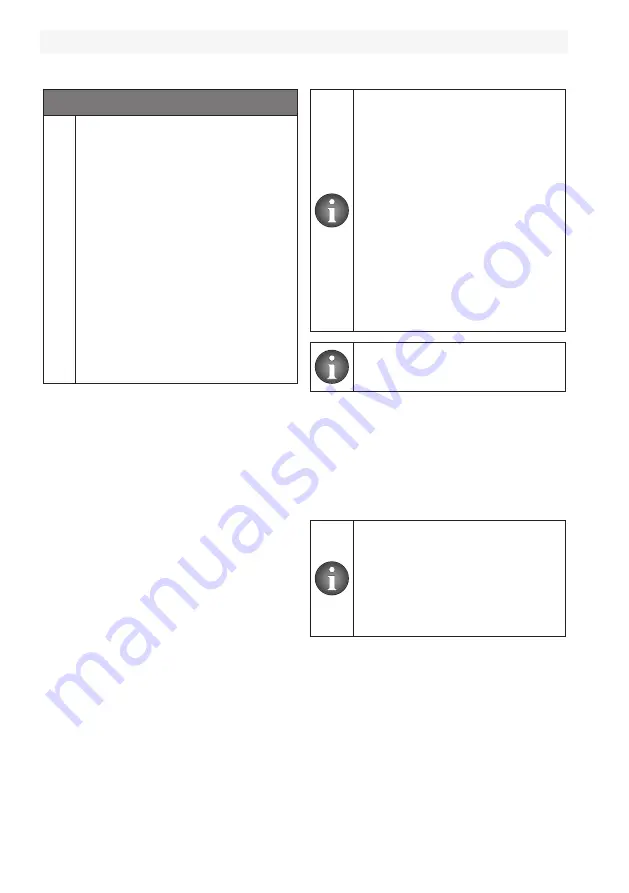
26
Commissioning
“Multidis SFQ”
140485280-V02.08.2019
NOTICE
Risk of damage due to
lubricants!
Seals can be destroyed by greasing
agents or oil.
f
Do not use any greasing agents or
oil for the installation.
f
Any dirt particles or grease or oil
residues must be flushed out of
the pipework before the product is
installed.
f
When choosing the operating fluid,
the latest technical status has to
be considered (e.g. VDI 2035).
f
A strainer must be installed in the
supply pipe to avoid contaminated
operating fluids (VDI 2035).
7. Commissioning
7.1 Filling, bleeding and leak
testing of the installation
The installation has to be filled and bled before
commissioning.
1.
Close the ball valves in front of the flow
distributor and return collector.
2. Open the valve inserts “QM” completely.
3. Turn the handwheel to position 5 with
the help of the presetting key.
The G
¾
connection of the fill and drain valve is
suitable for standard DN 15 hoses.
4. Close all valve inserts “QM” except for the
valve insert of the circuit to be filled, with
the help of the protection caps.
5.
Flush and fill each individual circuit, one
after another, via the fill and drain valve at
the return collector up to the fill and drain
ball valve of the flow distributor.
6. Carry out a leakage test according to DIN
EN 1264.
The leakage test and test pressure
have to be recorded. The leakage
test record is available as sample
form on our homepage.
f
Visit www.oventrop.com.
f
Select the menu point
“Products”.
f
Proceed to “Brochures”.
f
Select “Surface heating and
cooling Cofloor”.
f
The leakage test record can
be found in the brochure
“Cofloor Surface heating and
cooling systems - Systems with
distributor/collector”.
Bleeding during the filling process
and even during operation is carried
out via the fill and drain valves.
7.2 Protection cap
The valve inserts “QM” of the stainless steel
distributor/collector “Multidis SFQ” are
supplied with a plastic protection cap (see
Illust. 2 on page 22). It protects the valve
stem and can be used for the manual setting of
the valve lift during the construction period.
f
Turning in clockwise direction
Z
The valve insert closes and
the heat supply is reduced
f
Turning in anticlockwise direction
Z
The valve insert opens and
the heat supply is increased