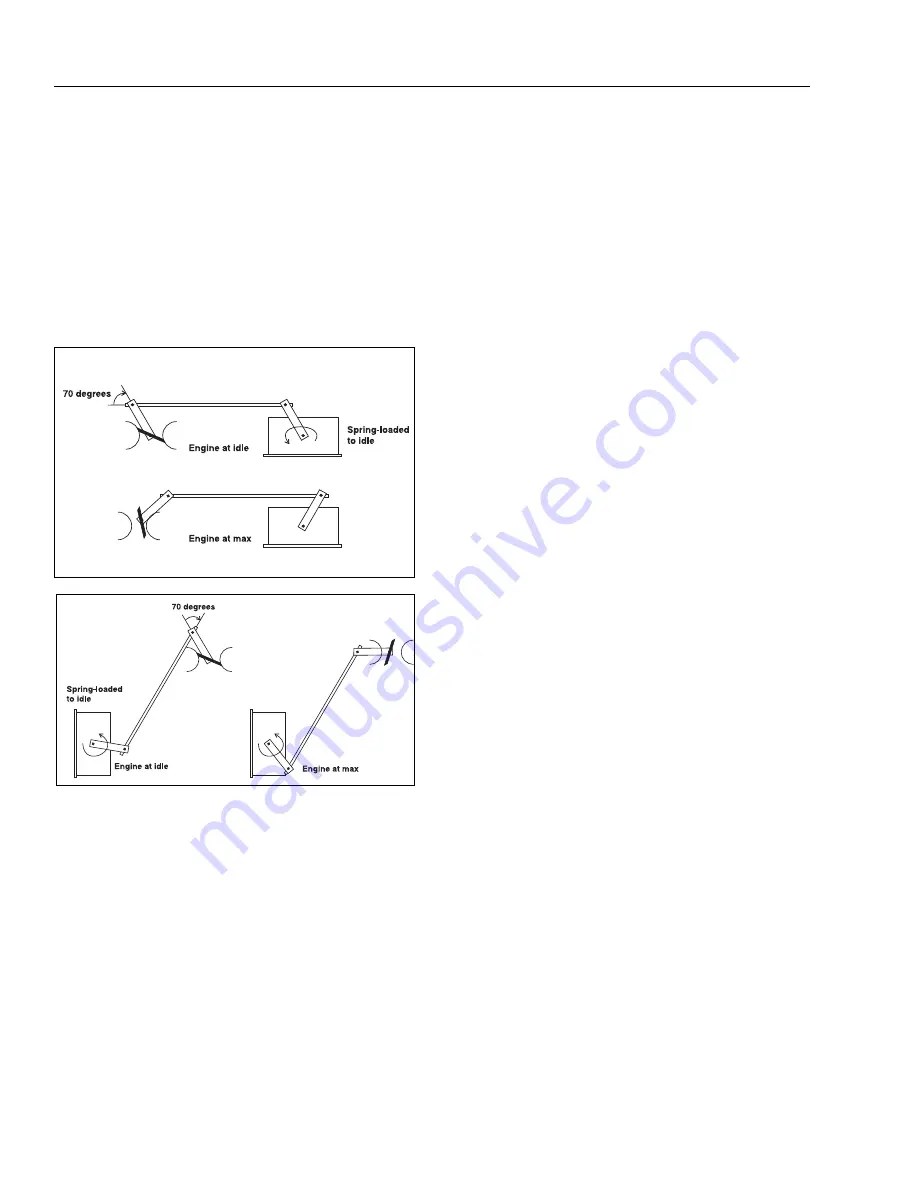
SECTION 3 - CHASSIS & TURNTABLE
3-112
– JLG Lift –
3120740
spring-loaded direction. Also, the Actuator can be mounted in
any attitude.
The needed travel of the carburetor determines how far out on
the Actuator arm the rod is to be attached. In most cases, the
carburetor should be moved from closed to above 10 degrees
from full open as the Actuator is moved min. to max. THEN
ALTER THE LENGTH OF THE ROD SLIGHTLY (PERHAPS.030”), SO
THAT THE ACTUATOR IS JUST OFF ITS INTERNAL STOP, AND IS
PULLING THE BUTTERFLY AGAINST ITS STOP. This insures that
the carburetor can fully close to idle on load dumps, minimiz-
ing overspeeds.
Examine the system for springs, such as carburetor return
springs. These should be removed. Some automotive carbure-
tors (as opposed to industrial carburetors) contain internal
springs for accelerator pumps, etc. These may make good gov-
erning difficult, or even impossible. For this, and other reasons,
industrial carburetors are much to be preferred.
Move the linkage slowly through its travel, and look for any
binding or unexplained forces. Correct any before going fur-
ther.
Many “governing” problems are really caused by binding of
the butterfly and its shaft in the carburetor. This is caused by
loading due to vacuum under the butterfly and atmospheric
pressure above when the engine is running. These forces can-
not be felt when the engine is not running. Therefore, start the
engine while carefully controlling the speed by hand, and feel
for binding or airload forces. Needle bearings on the butterfly
shaft are available on many industrial carburetors to deal with
this problem. Any tendency on the butterfly stick must be cor-
rected.
Mounting-Controller
Select a reasonably cool, dry, and vibration free location.
The rear cover will probably need to be removed during set-up
in order to make adjustments for speed setting and gain. You
may wish to defer final installation until this is done.
After completing these adjustments, replace cover. Mount so
that water cannot pool on this cover. Always mount the con-
troller with the strain relief down. This will prevent water from
entering thru the cable, also place the vent hole in the bottom
of the controller down.
Wiring
See wiring diagram for details of hook-up.
Use #16 wire minimum.
Keep all wiring to the Governor as short as is practical.
Go directly from the controller ground terminal (B of the 8 pin
connector) by dedicated wire, to the battery “minus” terminal.
If this cannot be done, for some reason, go by dedicated wire
to a very good engine ground.
A properly functioning engine electrical system will supply
13.5 - 14.8 VDC when the engine is running. If wiring size is
adequate, with good connections and proper grounds, you
will get this reading between the wires terminals A & B of the 8
pin connector when the Governor is controlling engine speed.
Verify this. Improper hook-up can damage electronics. Re-
check wiring before applying power.
Power Distribution
8 Pin Connector
Pin:
a.
12 VDC from the make before break oil pressure
switch. This switch provides power to pin A when
the ignition is on and the engine is not running (no
oil pressure), or when the ignition is turned off when
the engine is running (has oil pressure).
b.
Ground.
c.
Tach signal from the engine ignition system.
d.
Tach signal from the engine ignition system.
e.
Control signal to operate the Actuator.
f.
Control signal to operate the Actuator.
g.
Removes ground from the start lock out relay when
the engine is running above the start lock out set
point. A 20 turn pot is provided to adjust this set
point. (usually around 500 RPM)
Go
to
Discount-Equipment.com
to
order
your
parts