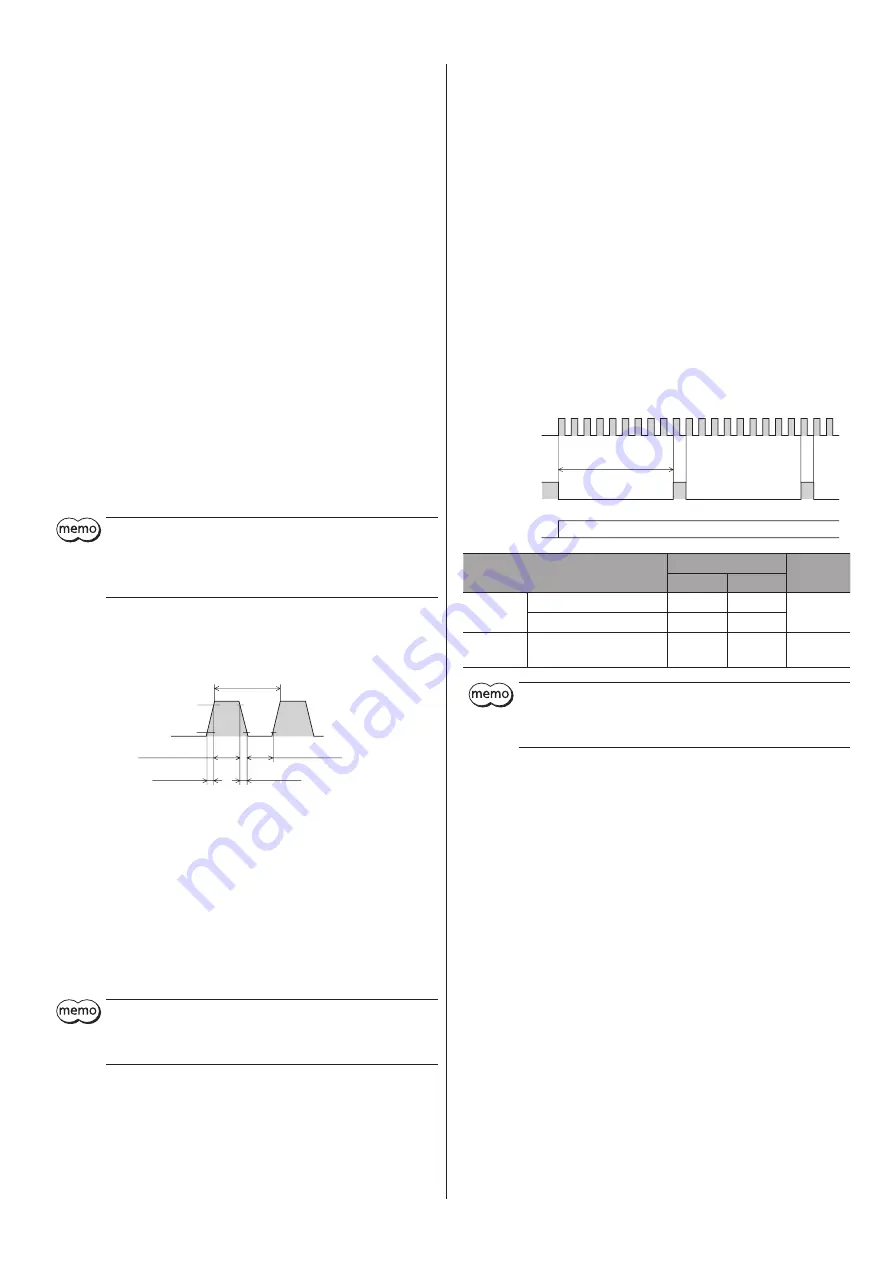
8
Explanation of I/O signals
z
Input signals
The signal input state represents "ON: Carrying current" or "OFF: Not carrying
current" state of the internal photocoupler.
The interval for switching the motor direction represents the response time of
the circuit. Set this interval to an appropriate time after which the motor will
respond.
•
PLS (CW) input, DIR (CCW) input
Set a desired pulse input mode of the driver according to the pulse output
mode of the controller used with the driver.
Maximum input pulse frequency (duty cycle is 50%)
y
When the controller is of line driver type: 1 MHz
y
When the controller is of open-collector type: 250 kHz
1-pulse input mode
When the PLS input is turned from OFF to ON while the DIR input is ON, the
motor will rotate by one step in CW direction.
When the PLS input is turned from OFF to ON while the DIR input is OFF, the
motor will rotate by one step in CCW direction.
2-pulse input mode
When the CW input is turned from OFF to ON, the motor will rotate by one
step in CW direction.
When the CCW input is turned from OFF to ON, the motor will rotate by one
step in CCW direction.
y
When the motor is at standstill, be sure to keep the photocoupler in
OFF state.
y
Do not input the CW pulse and CCW pulse simultaneously. If the
other pulse is input while one of the pulse is ON, the motor cannot
operate normally.
Pulse signal
Pulses with sharp rising and falling edges should be input as shown in the
figure below. The figure shows the voltage levels of pulse signals.
90%
10%
0.4 µs or more
0.4 µs or more
1 µs or more
2 µs or less
2 µs or less
ON
OFF
•
AWO (all windings off) input
When the AWO input is turned ON, the motor current will be cut off and the
motor will lose its holding torque. The motor output shaft can be turned
manually.
When the AWO input is turned OFF, current will be supplied and the holding
torque will be restored.
•
CS (step angle switching) input
When the CS input is turned ON, the motor rotates at a basic step angle.
When the CS input is turned OFF, the motor rotates at the step angle set by
the driver switch.
y
Do not change the CS input while operating. The motor may lose its
synchronism, causing position deviation or standstill of the motor.
y
When changing the step angle using the CS input, do so while the
TIM output is ON.
z
Output signals
The driver outputs signals are photocoupler/open-collector output. The
signal output state represents "ON: Carrying current" or "OFF: Not carrying
current" state of the internal photocoupler.
•
ALM (alarm) output
The ALM output is normally closed. When an alarm generates, the ALM
output will turn OFF and the motor current will be cut off.
At the same time, the PWR/ALM LED of the driver will blink in red.
•
TIM (timing) output
Every time the motor output shaft rotates by 7.2° (3.6° for high-resolution
type), the motor excitation state becomes the initial setting state (step 0), and
the TIM output turns ON. If an AND circuit is configured with signals of the
home sensor and TIM output when the home position in the equipment is
detected, the tolerance for the motor stop positions in a detection range of
the home sensor can be reduced and the further accurate home position can
be detected.
Example of the TIM output when the step angle is 0.72
°
(resolution
500 P/R)
Pulse input
Motor output shaft
rotates by 7.2º.
1 2 3
• • •
1
0
20
ON
OFF
TIM output
ON
OFF
Motor operation
Motor type
Number of divisions
TIM output
1
10
Standard
Base step angle 1.8°/step
1.8°
0.18°
every 7.2°
Base step angle 0.72°/step
0.72°
0.072°
High-
resolution
Base step angle 0.36°/step
0.36°
0.036°
every 3.6°
y
When using the TIM output, keep the input pulse frequency to be
500 Hz or less.
y
When using the TIM output, set the pulse or step angle so that the
motor output shaft stops at an integral multiple of 7.2°.