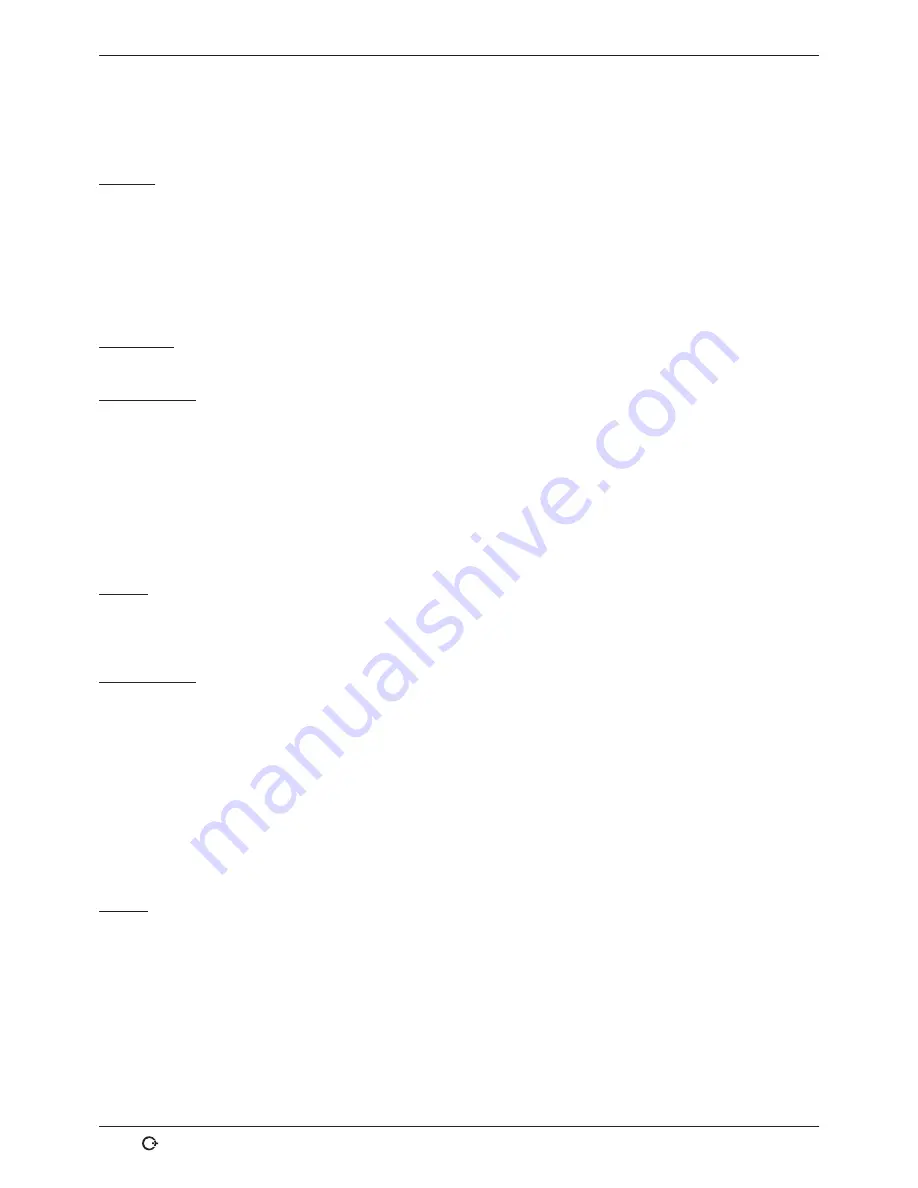
Service and troubleshooting
ORBIMAT 180 SW
| Operating instructions
68
orbitalum tools
GmbH, D-78224 Singen, www.orbitalum.com, Phone +49 (0) 77 31 792-0
(17.09.18) OW_ORBIMAT_180SW_BA_850060202_00_EN
9.1.7
Info
Information on the software version currently used and the Serial No. of the machine.
View Info
X
Enter the letter sequence
VER
(for VERSION) on the keyboard.
9.2
Possible application/operating errors
9.2.1
Uneven weld seam ("current fluctuations")
Observation
Weld seam uneven
Possible causes
• Current fluctuations as cause
The OM 165 CA unit, for example, compensates possible current fluctuations in the mains in the range from 85–260
Volt.
If you do not receive an error message from the system during welding, the weld current is, with 99% certainty,
within the limit values set for the respective procedure.
• Pipe tolerances
• Uneven weld seams can occur if classic forming gases (which contain up to 30% hydrogen in addition to nitrogen)
are used with cassette heads inside the pipe. The hydrogen enters the welding pocket in an undefined quantity and
affects the welding result as an energy carrier "randomly".
Remedy
X
Always use the same gas inside the pipe as in the weld head.
9.2.2
Annealing colors inside/outside
Possible causes
• Annealing colors arise only as a result of a reaction between the base material and another substance under the
effect of a high temperature introduced into the material by the arc. This other substance can take the form of oxy-
gen, humidity or other impurities.
• Parts of grinding disks that remain on the workpiece as residue.
• Annealing colors at the start of the seam: Possibly gas pre purge time too short. Annealing colors gradually fade as
welding progresses.
• Annealing colors at the end of welding: Gas post purge too short or (closed) weld head possibly opened too early.
• Depending on the design type, more annealing colors occur on the outside of the pipes with open weld heads (TP
series) than with cassette heads.
• TP weld heads invariably react with more sensitivity to any drafts present. A draft can "blow away" the gas cover,
thereby causing extreme annealing colors.
Remedy
X
Clean pipe ends with a suitable solvent which evaporates without leaving residue (for example acetone).
X
Ensure that the pipe ends are bare metal.
X
Remove any and all oils and greases (from sawing or bending).
X
Ensure that the following parameters are set:
–
Gas quantity set sufficiently long, sufficient volume.
–
Approx. 7 l/min for the weld gas and approx. 2–3 l/min for the forming gas
–
Gas pre purge time/gas post purge time set optimally.