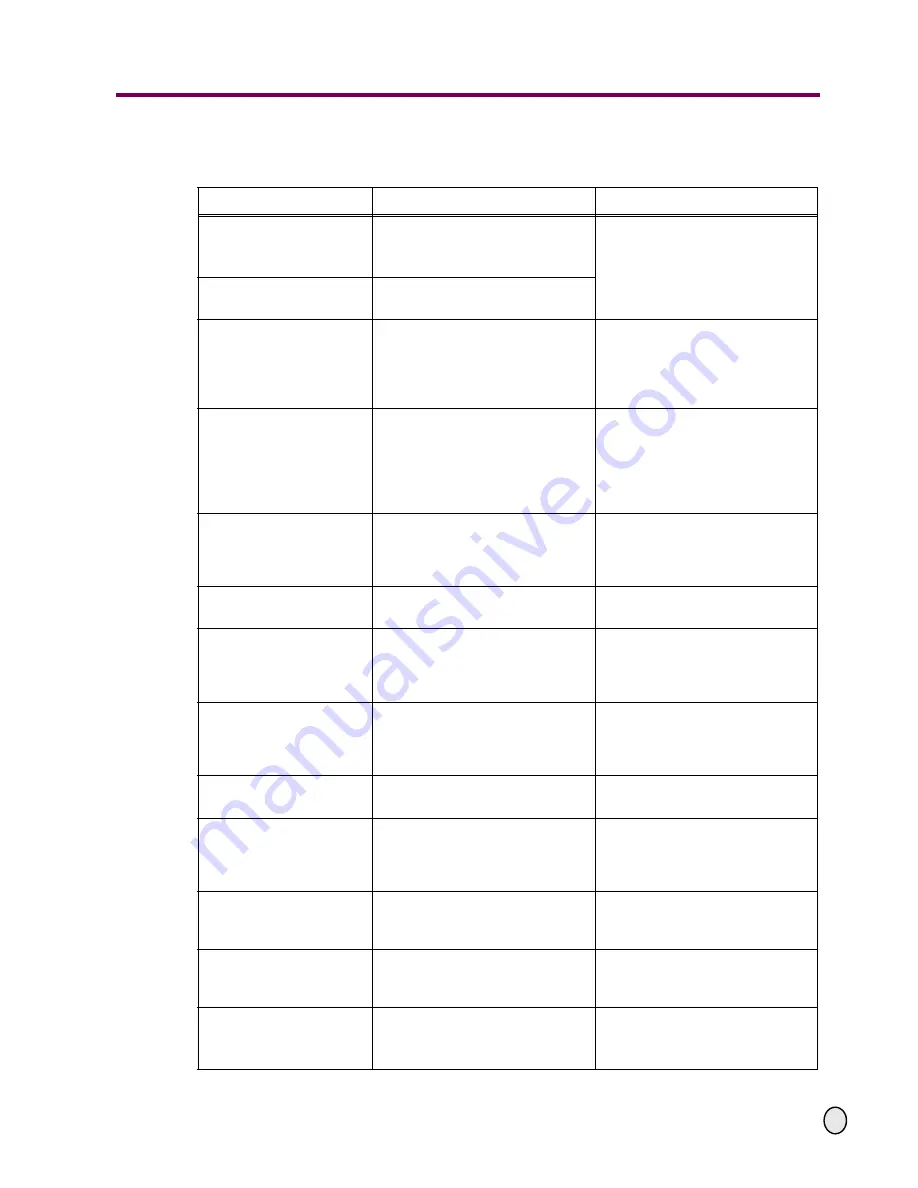
Malfunctions
OPTIMUM
M A S C H I N E N - G E R M A N Y
21 / 10 / 2008
Page 40
Malfunctions Bench drill B16 H Vario ; Version 1.0.2
©
200
8
GB
8
Malfunctions
Malfunction
Cause / possible effects
Solution
FI protective switch on
machines with frequency
converter triggers.
•
an unusual FI protective switch is
being used
•
„Power supply“ on page 20
Engine gets hot
•
wrong connection of 400 V
machines
Noise during working
•
Spindle turning dry
•
Tool blunt or is being incorrectly
secured
•
Grease spindle (only in the dis-
mantled condition possible)
•
Use new tool and check secu-
ring (fixed setting of the bit, drill
chuck and morse taper).
Bit „burnt“
•
bit speed too high/too much feed
•
The chips have not been remo-
ved from the bore hole
•
Bit blunt
•
no or too little cooling
•
Select another speed
•
Extract the bit more often
•
Sharpen or replace bit
•
Use coolant.
Bit tip moves, bore hole
is not circular
•
hard part on the work piece
•
Unequal length of the cutting spi-
ral or angles in the bit.
•
Bit deformed
•
Replace bit
Defective bit
•
No support used.
•
Use a wooden board and secure
it to the work piece
Bit running off-centre or
„hoping“
•
Bit deformed
•
spindle bearing worn out
•
Bit badly secured.
•
Drill chuck defective.
•
Replace bit
•
replace spindle bearing
•
Secure the bit properly
•
Replace the drill chuck
Impossible to introduce
drill chuck or morse taper
•
There is dirt, grease or oil on the
inner conical surface of the drill
chuck or on the conical surface of
the drilling spindle
•
Clean surfaces well
•
Keep surfaces fat free
Engine does not start
•
engine badly connected
•
Defective fuse
•
Have it checked by authorised
personnel
Overheating of motor and
lack of power
•
Engine overloaded
•
Insufficient mains voltage
•
engine badly connected
•
Reduce feed, disconnect if
necessary
•
Have it checked by authorised
personnel
Precision of the work
deficient
•
Heavy and unbalanced or twi-
sted work piece
•
Balance work piece statically and
secure it without straining
•
Adjust work piece holder
Drilling sleeve does not
return to its initial position
•
Failure of spindle return spring
•
Locking bolt inserted
•
Check spindle return spring and
replace if necessary
•
Remove locking bolt
Impossible to move the
drilling spindle sleeve
downwards.
•
Locking bolt inserted
•
Drill depth adjustment no
released
•
Pull out the locking bolt
•
Release drill depth adjustment