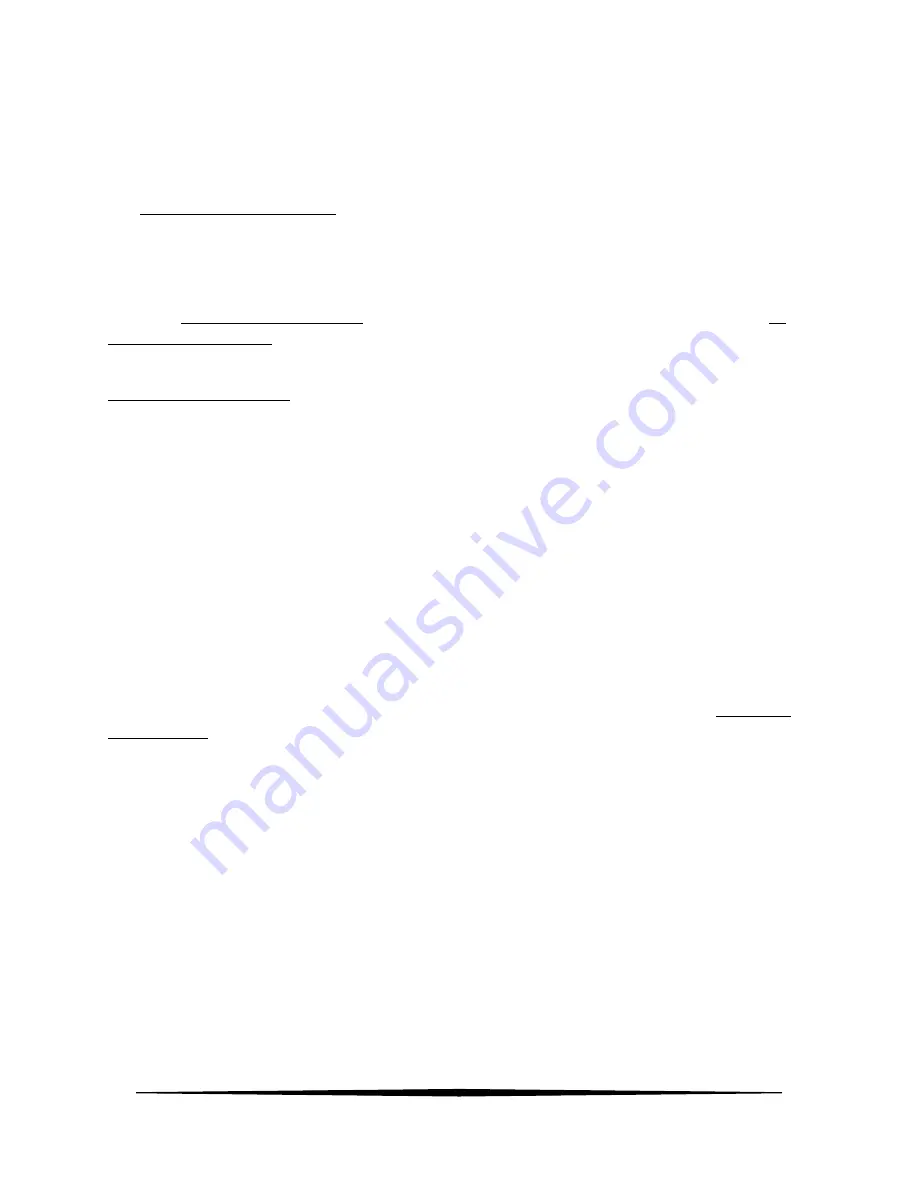
15
wood that will fit through a 1.29” diameter hole. The same 15/16 socket used to remove the nuts works
well for this. We do not need to be cautious about damaging the old bearings to remove. (see
illustration page 16)
When installing the new bearings, first clean the surface of the opening where the bearings are to enter.
If your pulley has the 4 drive pins installed, I suggest removing them for this process. You will need a
7/16 deep well socket for this. Stand the pulley in the press resting on its front face. Use a pusher device
that will contact the OUTER RACE. It is important that you do NOT press on the inner race to install the
bearings. This will damage the bearings and shorten their life. The best choice for a pushing tool is a
round rod/pipe or piece of wood that is 1-
1/2” diameter that will pass through the 1.57” opening in the
pulley. (see illustration on page 16) Many people use a large socket that makes contact with the outer
race but fits through the opening. The first bearing must be pressed all the way down to the bottom of
the cavity, followed by the spacer ring
(you don’t want to forget this) then, finally the last bearin
g. Be
careful not to over press especially if you left the drive pins in the pulley. When properly installed the
last bearing will be below the retaining ring groove and the retaining ring should go in easily.
Installation without a Press
When using this method, use a short piece of wood (or 15/16 socket) and a mallet/hammer to drive the
old bearings from the cast inner bowl. Support the pulley on a piece of wood to prevent damaging it.
We don’t have to be cautious about damaging the old bearings. When i
nstalling the new bearings, first
clean the surface of the opening where the bearings are to enter. Turn the pulley over and rest its front
face (or drive pins if present) on the piece of wood. Place the first bearing in the center opening and
place a flat piece of wood or steel across the top of the bearing. It is important that you drive the
bearing in straight AND that you do this by applying force to the outer race. It is OK that the flat steel or
wood is contacting the inner race as long as the outer race is also in contact. Tap the wood/steel plate
with the hammer and slowly drive the bearing until it is flush with the top of the pulley. Now there are 2
ways to proceed. One is to find a round object (large socket, steel tube, steel rod, etc.) that will contact
the outer race and also fit through the opening in the pulley and use this object to further tap the
bearing to the bottom of the cavity. The other way is to use a short wooden dowel ½ or ¾” in diameter
and to tap the outer race with small taps as you work the dowel around the perimeter of the outer race
as you gradually drive the bearing down to the bottom. When the first bearing is installed, follow with
the spacer ring
(you don’t want to forget this) then; repeat the same process with the top
bearing. Then
install the retaining ring.
Reinstall drive pins, pulley, belts, keeper plates, dust cover in reverse order of removal.