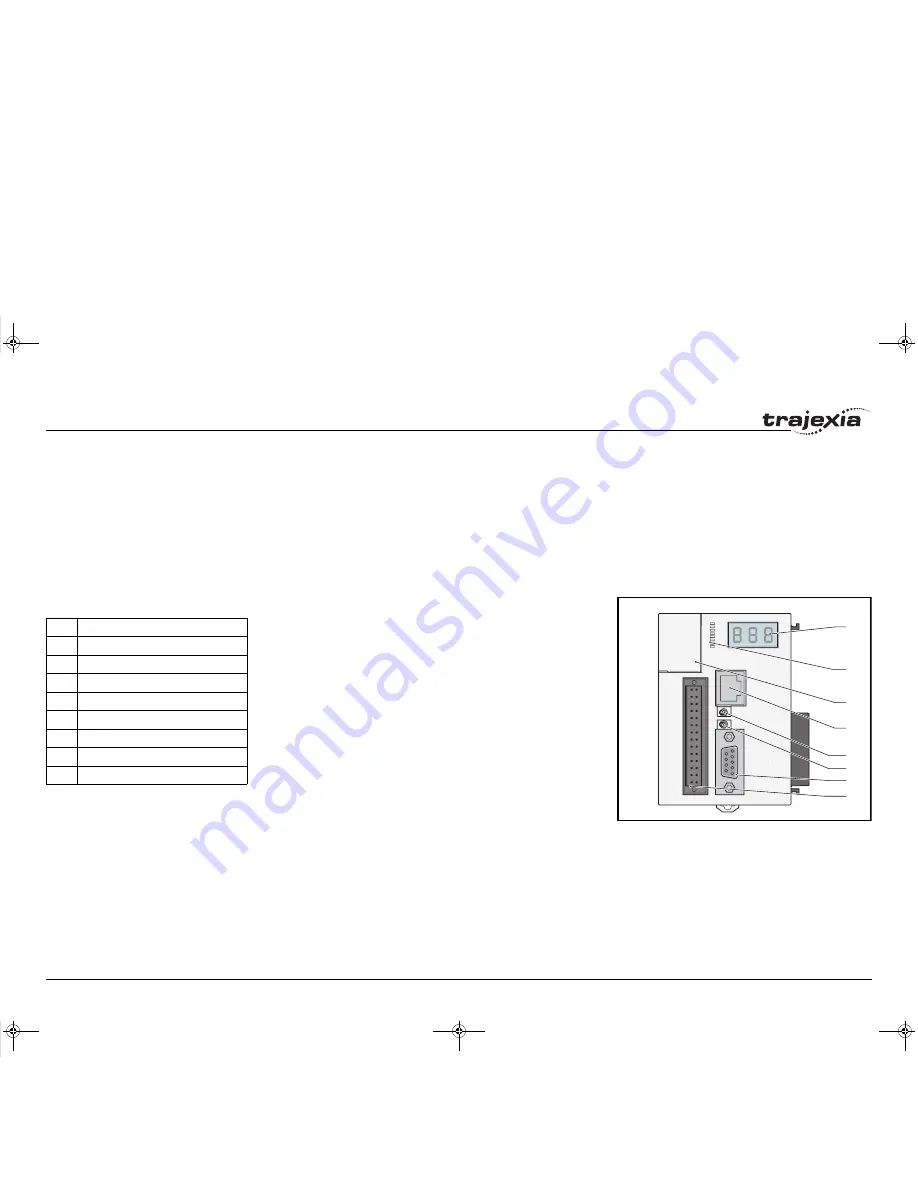
Hardware reference
HARDWARE REFERENCE MANUAL
68
Revi
si
on 3.0
3.4
TJ1-MC__
3.4.1
Introduction
The TJ1-MC__ is the heart of the Trajexia system. You can
program the TJ1-MC__ with the BASIC programming language to
control the expansion units and the servo motors attached to the
expansion units. Refer to the Programming Manual.
There are two versions of the TJ1-MC__: The TJ1-MC04 supports
4 axes. The TJ1-MC16 supports 16 axes.
fig. 19
The TJ1-MC__ has these visible parts:
/i
A
B
C
D
E
F
G
H
Part
Description
A
LED display
B
I/O LEDs 0 - 7
C
Battery
D
Ethernet connector
E
TERM ON/OFF switch
F
WIRE 2/4 switch
G
Serial connector
H
28-pin I/O connector
I51E-EN-03.book Seite 68 Donnerstag, 28. Juni 2007 1:05 13