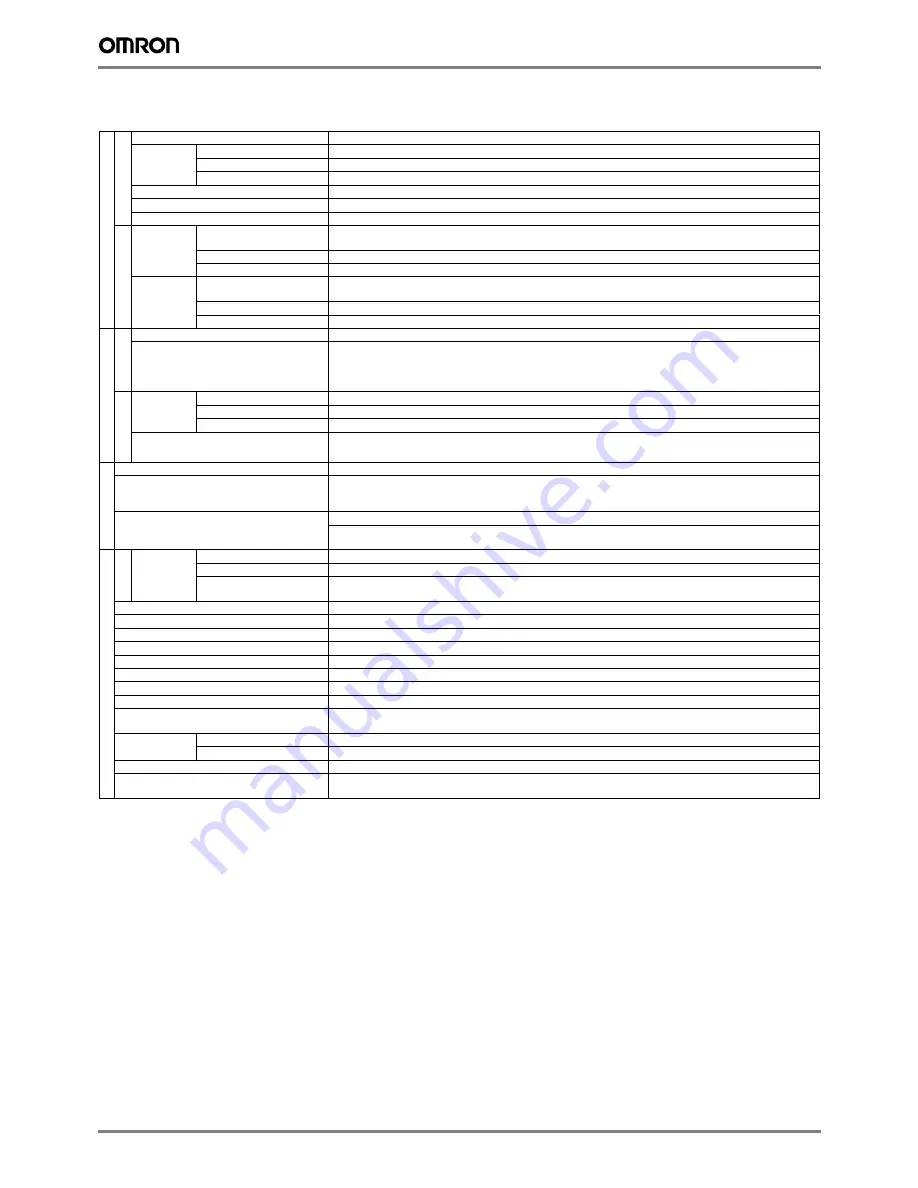
Sigma-5 servo system
3
A
C
S
er
vo
s
ys
te
m
s
Sigma-5 Analog/Pulse Reference Servo Drive
General specifications
Sp
ee
d/
to
rque
con
tr
o
l mode
P
er
fo
rm
an
ce
Speed control range
1:5000
Speed
variance
Load variance
During 0 to 100% load ±0.01% max. (at rated speed)
Voltage variance
Rated voltage ±10%:0% (at rated speed)
Temperature variance
25 ±25 °C: ±0.1 % max. (at rated speed)
Frequency characteristics
1.6 kHz
Torque control accuracy (Repeatability)
±1%
Soft start time setting
0 to 10 s (acceleration, deceleration can each be set.)
Inpu
t
signal
Speed
reference
input
Reference voltage
±6 VDC (forward motor rotation if positive reference) at rated speed: Set at delivery
Variable setting range: ±2 to ±10 VDC at rated speed/ max. input voltage: ±12 V
Input impedance
Approx. 14 k
Ω
Circuit time constant
Approx. 30 µs
Torque
reference
input
Reference voltage
±3 VDC (forward rotation if positive reference) at rated torque: Set at delivery
Variable setting range ±1 to ±10 VDC at rated torque reference, max. input voltage: ±12 V
Input impedance
Approx. 14 K
Ω
Circuit time constant
Approx. 30
µs
Po
si
tion
co
ntrol
mod
e
p
er
fo
rm
an
ce Feedforward compensation
0 to 100% (setting resolution: 1%)
Position completed width setting
0 to 1073741824 command units (setting resolution: 1 command unit)
Inpu
t s
ignal
Command
pulse
Input pulse type
Sign + pulse train, 90° phase displacement 2-phase pulse (A-phase+ B-phase) or CCW/CW pulse train
Input pulse form
Non-insultated line driver (+5 V level) , open collector.
Input pulse frequency
0 to 4 Mpps (200 Kpps max. at open collector)
Control signal
Clears error pulse by external signal
I/O
s
ig
n
al
Position signal output
A-phase, B.phase, C-phase: line driver output.
Sequence input signal
Servo ON, P control (or control mode switching, forward/reverse motor rotation by internal speed setting, zero
clamp, command pulse inhibit), forward/reverse run prohibit, forward/reverse current limit (or internal speed
switching), alarm reset.
Sequence output signal
Servo alarm, alarm codes (3-bit output): CN1 output terminal is fixed
It is possible to output three types of signal form incl.: positioning complete, speed coincidence detection, servo-
motor rotation detection, servo ready, current limit detection, speed limit detection, brake release, warning, NEAR.
In
te
g
ra
te
d
f
u
n
ct
io
n
s
USB
Communica-
tions
Interface
Personal computer
Communications standard
Compliant with USB1.1 standard (12 Mbps)
Function
Status display, parameter settings, adjustment functions, utility functions, alarm traceback display, JOG run/au-
totuning operations and graphing functions for speed/torque command signal, etc
Automatic load inertia detection
Automatic motor parameter setting. One parameter rigidity setting.
Dynamic brake (DB)
Operates during main power OFF, servo alarm, servo OFF or overtravel
Regenerative processing
Internal resistor included in models from 500 W to 5 kW. Regenerative resistor externally mounted (option).
Overtravel (OT) prevention function
DB stop, deceleration stop or coast to stop during P-OT, N-OT operation
Encoder divider function
Optional division pulses possible
Electronic gearing
0,01< Numerator/Denominator<100
Internal speed setting function
3 speeds may be set internally
Protective functions
Overcurrent, overvoltage, low voltage, overload, regenerative error
Analog monitor functions for supervision
Integrates analog monitor connector for supervision of the speed and torque reference signals, etc.
Number of channels: 2 (Output voltage: +/-10V DC)
Panel operator
Display functions
CHARGE, 7-segments LEDx5
Panel operator keys
Used to set parameters (4 keys)
Safety functions
Hard wire base block signal and status monitor (fixed output) of safety circuit
Others
Reverse connection, zero search, automatic motor discrimination function, and DC reactor connection terminal
for high frequency power suppression function.
10
Sigma-5 servo system