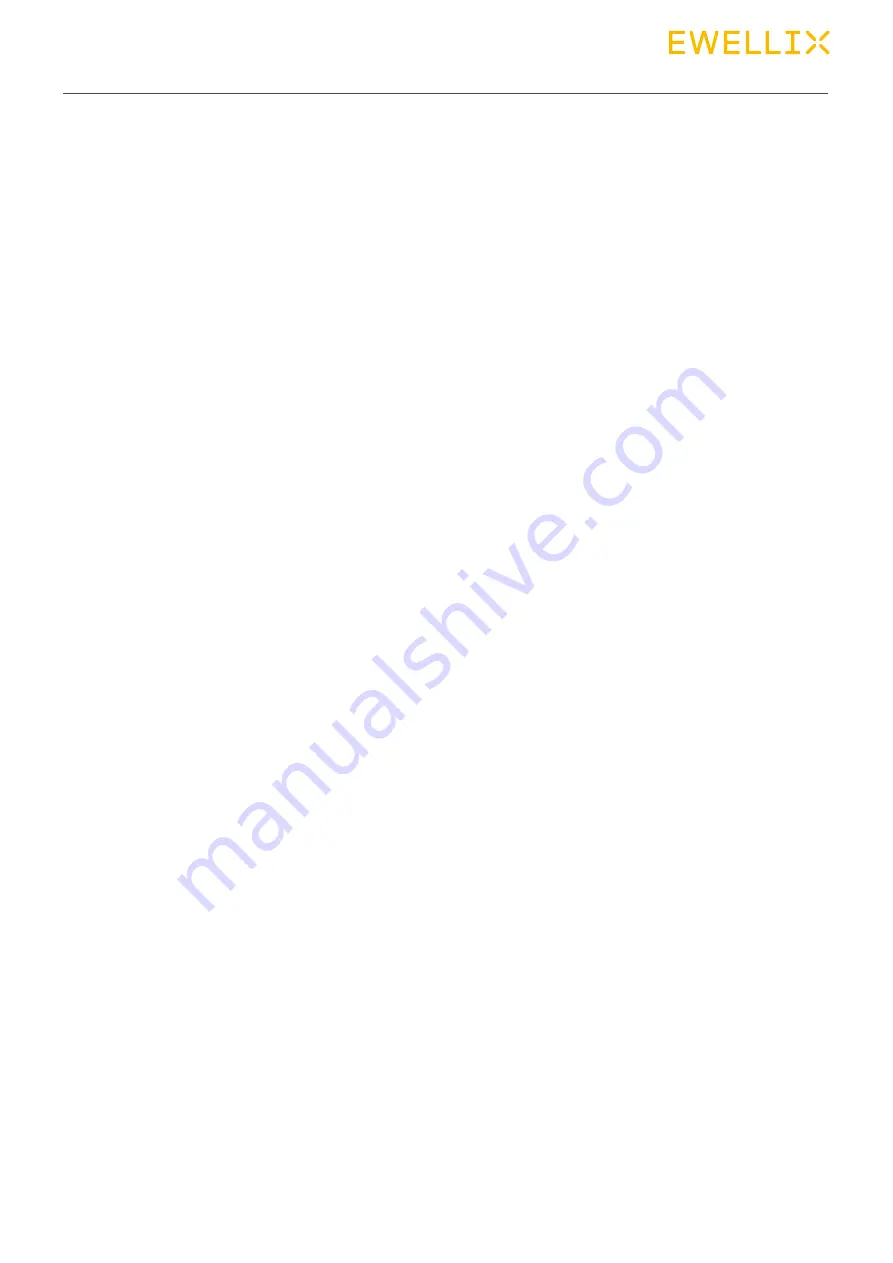
19
19
Typical Usage
Initial Installation and Testing
Upon the installation of the pillar with the TM robot, the
Command component should be used by itself in an empty
project to troubleshoot any connection issues and to test if
the commands are working. Use the following steps to get
the pillar running:
1. Create a new project and drag-and-drop the component
into the flow.
2. If the pillar’s IP address has been changed from the de-
fault, specify the new IP address in the component.
3. Run the project with the Get_Info function set to true
and the other functions set to false (this is the default
configuration of the component).
a. If there is an Error Code displayed, follow the error
code troubleshooting tips and repeat Step 3 until the
pillar gives a response. See Appendix A for a list of
LIFTKIT component error codes.
b. If there is a response from the pillar other than
“READY”, the connection to the pillar was success-
fully established, but further action is required based
on the response given. Depending on the pillar’s cur-
rent state, it may be possible to issue the set_type
and set_virtualLimits commands with the compo-
nent. Refer to the Ewellix LIFTKIT manual for more
details on the available LIFTKIT commands, allowed
states, and responses. After each troubleshooting
step, repeat Step 3.
c. If the response from the pillar is “READY”, then it is
now possible to send it motion commands.
4. If needed, use the Set_VirtualLimits command to set the
appropriate virtual limits of the pillar.
5. Test the pillar’s motion by using the Move_Absolute
function to command the pillar to various positions within
the range of the virtual limits.
Regular Operation
The component can be used multiple times throughout a
TMflow project to get the current pillar status via the Get_
Info function or to send the pillar motion commands with the
Move_Absolute function. The relevant imported variables
will be updated as the flow moves through the component.
NOTE: If the component is used more than once in a project for
one LIFTKIT device, then the “Inherit old component” option
must be selected when dragging and dropping each component
after the first one into flow. This is because the LIFTKIT cannot
accept multiple connections to the same socket.
NOTE: It is not recommended to use the Set_Info function
during regular operation unless the virtual limits need to be
reconfigured regularly for an application.
7.0 S of tware in s truction for Ewellix LIF TKIT C om p on ent for TMflow