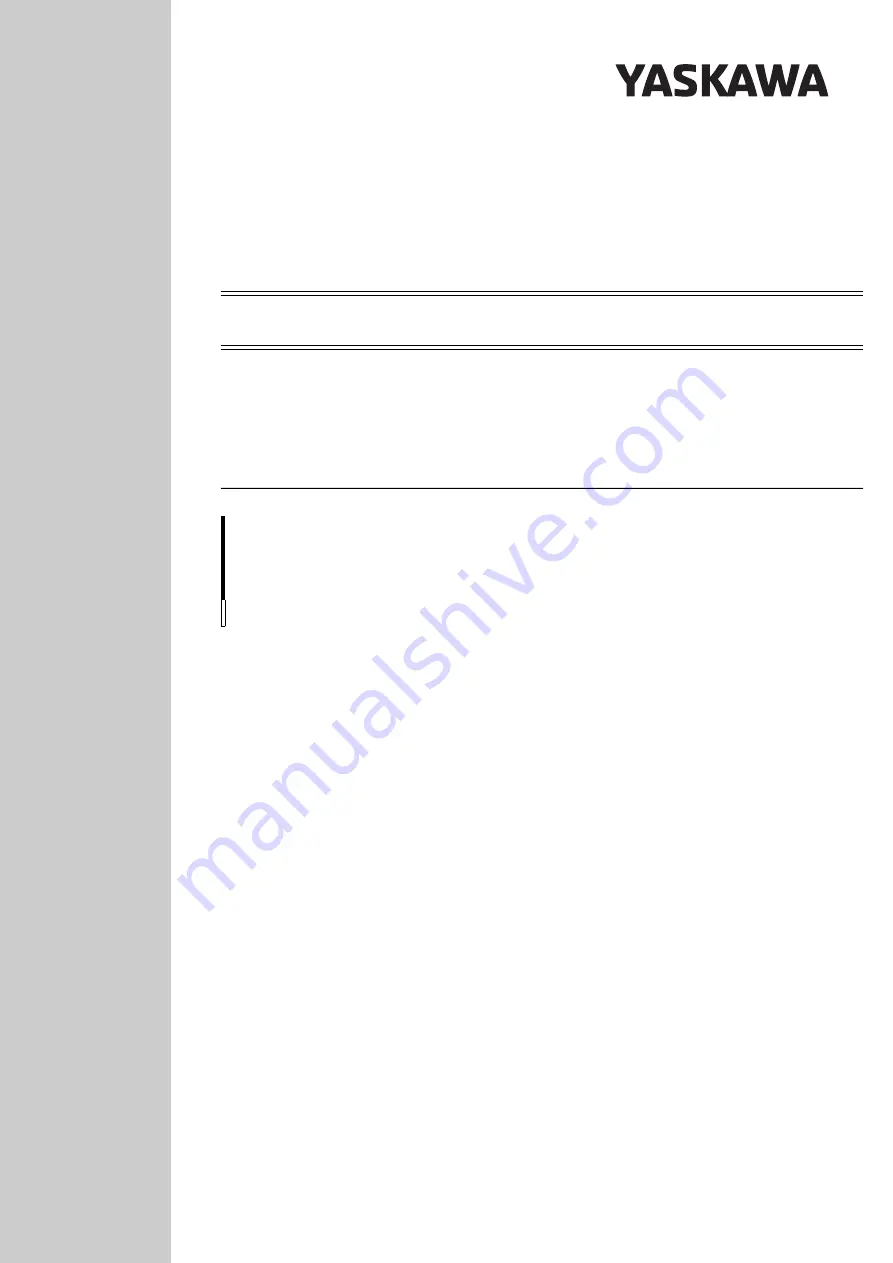
Part Number:
180930-1CD
Revision:
0
MOTOMAN-MH900
MAINTENANCE
Procedures described in this maintenance manual should be carried out by the person who took
the maintenance-relevant trainings offered by Yaskawa.
Upon receipt of the product and prior to initial operation, read these instructions thoroughly, and
retain for future reference.
MOTOMAN INSTRUCTIONS
MOTOMAN-MH900 INSTRUCTIONS
DX200 INSTRUCTIONS
DX200 OPERATOR’S MANUAL (for each purpose)
DX200 MAINTENANCE MANUAL
The DX200 operator’s manual above corresponds to a specific usage. Be sure to use the appropriate manual.
TYPE:
YR-MH00
9
00-A00
1 of 79