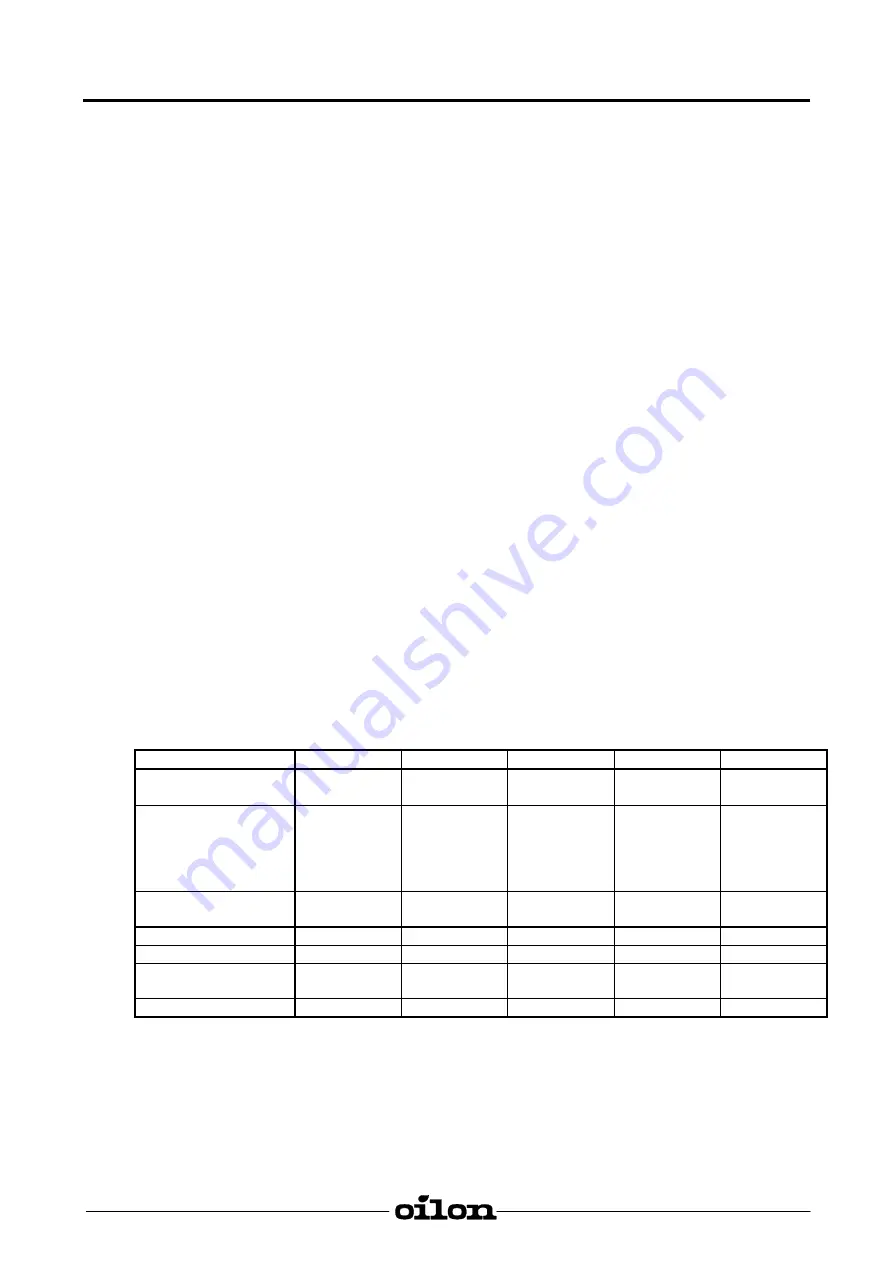
4
20039847GB
3.
Burner Technical Data
3.1. General
●
burner types: • 1-stage burners
KP-6
KP-6 L
KP-6-2
• 2-stage burners (”H” burners)
KP-6
LH
KP-6
H-2
●
on standard version the burner can be hinged to both sides
●
the burner must be installed in such a position, that the motor shaft lies horizontally; but the
burner must not, however, be installed upside down.
●
burner control unit internally connected
●
safety switch (limit switch) on hinged flange
●
control switch
●
air regulation: • stepless adjustable (1-stage burners)
• servomotor (2-stage burners)
●
oil pump atomising pressure:• 700 - 1400 kPa (7 - 14 bar) (1-stage burners)
• 700 - 2500 kPa (7 - 25 bar) (2-stage burners)
●
standard version equipped for two-pipe system
●
electrical connection with a plug connector (KP-6, KP-6 L, KP-6-2).
Extra equipment
●
run hour counter
●
filter Oilon 20
●
de-aerator Tiger Loop
●
oil meter
●
oil pressure gauge and valve
3.2. Technical
Data
Burner
KP-6
KP-6 L
KP-6 LH
KP-6-2
KP-6 H-2
Capacity kg/h
kW
3,5 - 10,042 -
120
3,5 - 10,0
42 - 120
3,5 - 10,0
42 - 120
6,0 - 12,0
71 - 140
6,0 - 16,0
71 - 190
Burner motor
Voltage 50 Hz 230 V
Output kW
Current A
Speed rpm
0,125
1,0
2750
0,125
1,0
2750
0,125
1,0
2750
0,125
1,0
2750
0,125
1,0
2750
Control unit
LOA24
/BHO64
LOA24
/BHO64
LOA24
/BHO64
LOA24
/BHO64
LOA24
/BHO64
Servo motor
-
-
SQN
-
SQN
Oil hoses
R ¼"
R ¼"
R ¼"
R ¼"
R ¼"
Oil pump
AS 47 C/
BFP 21 L3
AS 47 C/
BFP 21 L3
BFP 52E L3
AT 2 45 C
AS 47 C/
BFP 21 L3
BFP 52E L3
AT 2 45 C
Preheater W
-
30 - 240
30 - 240
-
-
Light fuel oil 1 kg/h
≅
11,86 kW
Содержание KP-6
Страница 7: ...5 20039847GB 3 3 Basic Assembly Drawing...