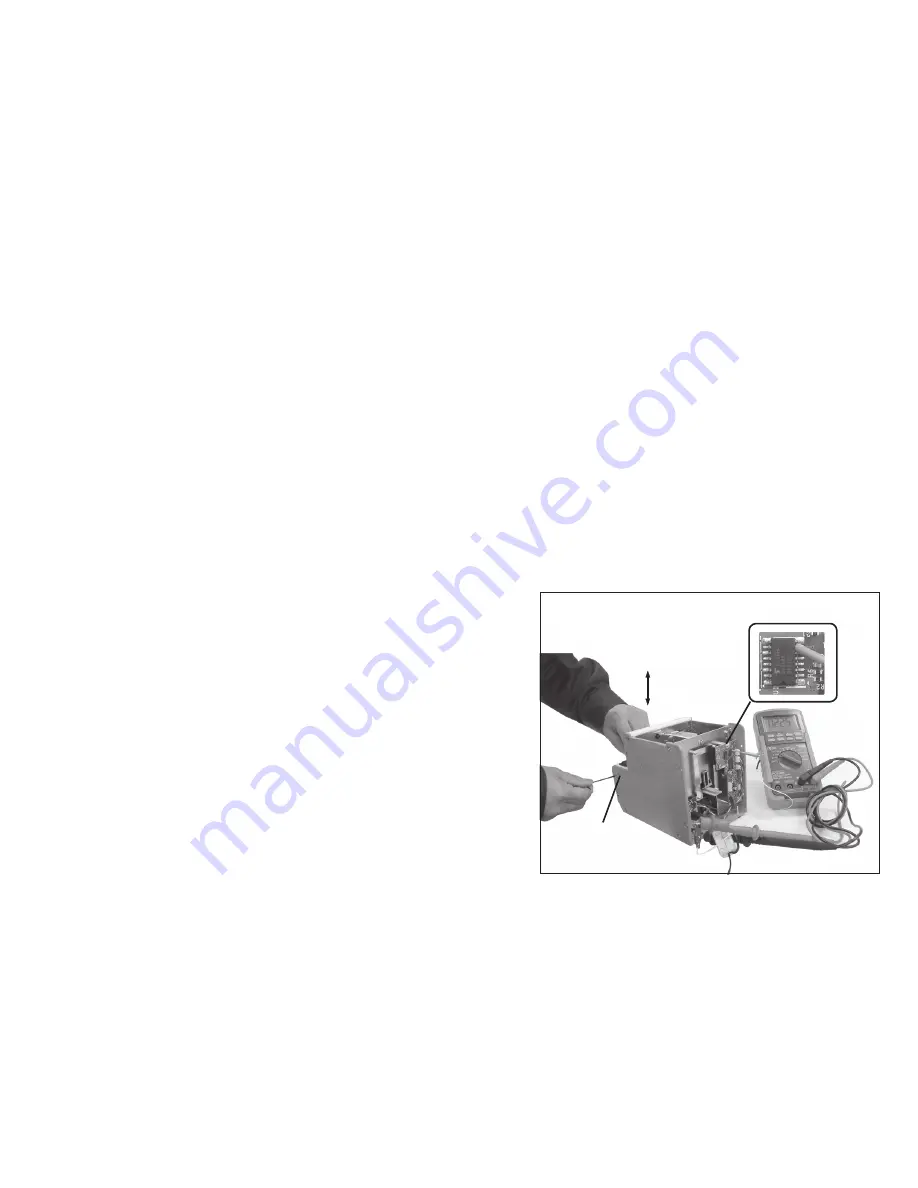
-
10
-
◆
Check of the sensor’s optical axis
If there is no screw at the stopper section, this machine continues operation, and if there are
screws, it
stops after a certain period of time has passed. This machine has the level of the screw/no screw sensor
adjusted by the reference rail on shipment. In reality, however, a level adjustment of the sensor may
become necessary when using thin-head screws or due to
occurrence of variation on rail replacement.
Then, follow the directions (1) and (2) for the adjustment.
(1)
- Loose the sensor attaching screw on the side lit up as much as it moves by picking up the sensor holder with fingers,
and turn on the power switch.
- Place a screw on the fail within the sensor range.
- Hold the rail end lightly with fingers as much as it doesn’t vibrate so that screws doesn’t pass through.
- When the sensor holder is moved up and down, there is a position the sensor of the receiving light side defects a screw
head and stops the vibration.Tight the sensor attaching screw at this position.
- Comfirm whether it really works or not. See if a screw passes through and the sensor detects if and stops.
(2)
* Remove the machine body rear cover, and measure the voltage
level. Adjust the IC4050 7th-pin voltage level. The ground, when mea-
suring it, is the body’s metal part.
* Adjustment is not necessary if the voltage level is within 0.25 to 1.5V
when a rail is and if there is no screw at the stopper section.
* When adjustment is necessary, loosen the sensor attaching screw
on the side. Adjust the voltage level by moving it up and down.
(It is easier to make an adjustment if connector of the main motor is
removed.)
* After the adjustment, throw in the screws and run it practically in or-
der to check the operation.
Note:
When no loaded screws are: 0.25 V to 1.5 V
When loaded screws are: 3.5 V or more
Adjusting the sensor attachment
up and down on the side lit up
The sensor attaching
screw on the side lit up
No.7 pin of IC4050