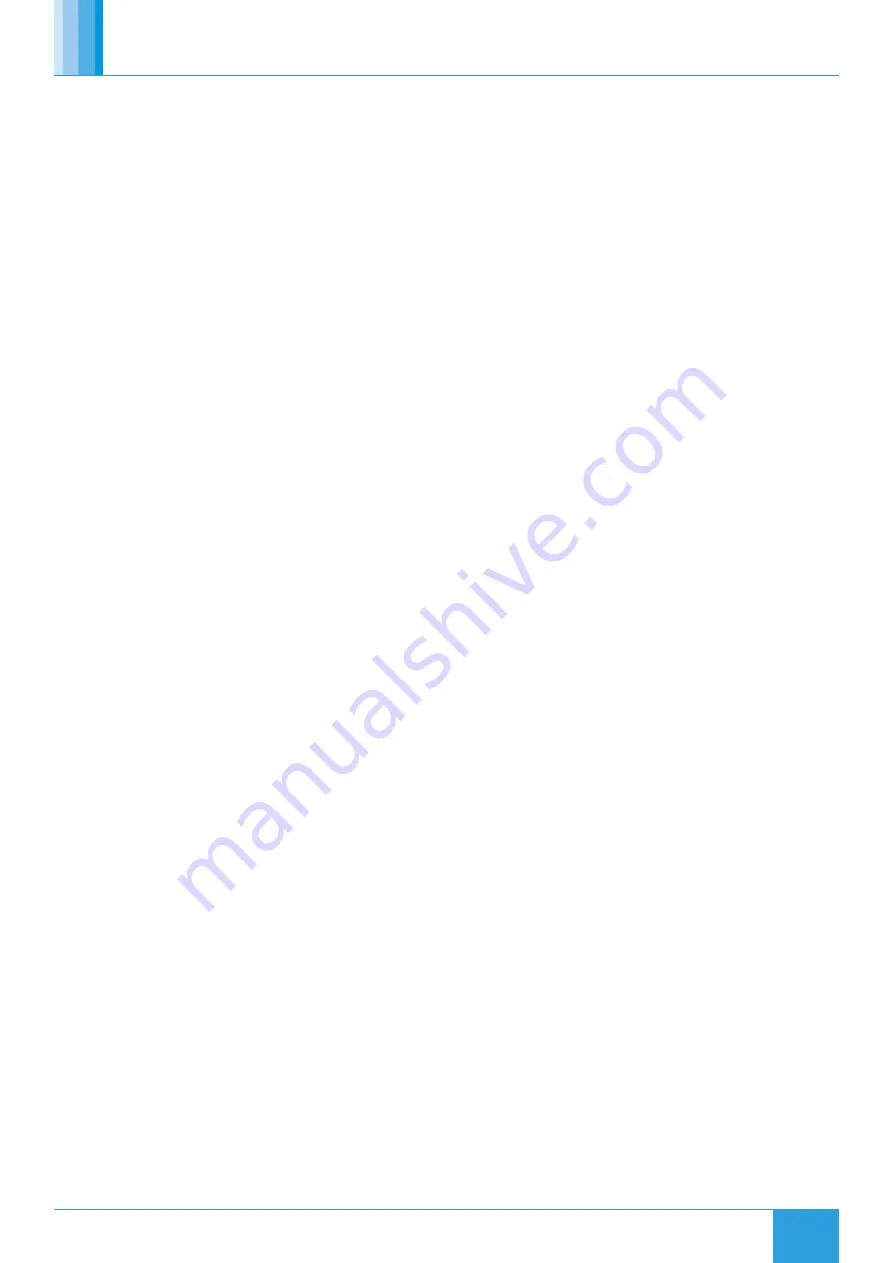
24
26. 01. 22. Document Number 671829
Nuaire | Western Industrial Estate | Caerphilly | CF83 1NA | nuaire.co.uk
BPS H-AT
Installation Manual
All coils sit in a common drip tray connected to the pre-fitted
condensate pump.
The coil panel has been pre-drilled and fitted with appropriate
grommets for pipe connections. Do not drill or cut the unit casing for
this purpose.
Coils should have their finned surface examined for accumulation of
dirt, lint and biological contaminants or similar. If necessary, wash
down affected areas with a mild detergent solution and a soft brush.
Care should be taken not to damage the finned surface, and any
cleaning fluids should be rinsed away with water.
A compressed air line may be used to blow out any solids between
fins. Do not probe the coil fin block with metal objects as damage
may cause leaks. Drain lines should be checked to ensure that they
are unobstructed and free draining. Drain pans should be flushed out
periodically to remove contamination.
The unit application may require particular attention to this item –
Check with Building Management personnel for details.
9.6 Legionella Check
Legionella risk management should be undertaken by a competent
person appointed by the duty holder in accordance with the latest
edition of the HSE approved code of practice L8 Legionnaires’ disease,
the control of legionella bacteria in water systems. Particular attention
should be given to:
•
Cooling coil.
•
Thermal Wheel.
•
Drain trays.
•
Water reservoirs.
9.7 Electric Heaters
An air handling unit would normally require no heater maintenance.
However a periodic check is advised to ensure that the fasteners and
electrical connections are operating correctly.
The electric heater unit is fitted with fail-safe thermal switches (self-
resetting) which will isolate the electric heater supply if a temperature
of 80°C is detected. This action is performed independently of any
controls fitted. Nuaire fitted controls will also stop heating if a fan or
heater failure is detected.
9.8 Bulkhead Lights
Ensure that lights are switched off and isolated before checking or
changing the lamp.
9.9 General
Inspect all internal and external surfaces to check for corrosion or
peeling of painted surfaces.
Thoroughly clean affected areas with a wire brush, apply a coat of zinc
rich primer or similar, and re-touch with suitable finishing paint. Ensure
tightness of all nuts, bolts, and fixings.
Check all components for general condition.
9.10 Specialist Equipment
Contact Nuaire for maintenance of specialised equipment that
would have been specified during design stage. A breakdown of the
component parts can be found on the design specification documents,
additional maintenance literature is available, please contact Nuaire.
This applies to any components not specifically mentioned in this
document.
9.0 MAINTENANCE
It is important that maintenance checks are recorded and that the
schedule is always adhered to, in all cases, the previous report should
be referred to.
9.1 Fans
Please refer to general arrangement drawings for details of the type
of fan and drive that is fitted. Maintenance guidelines for all fans are
beyond this manual, please contact Nuaire for specific documents.
•
Before any work is carried out, please ensure that:
•
The power supply to the motor is switched off.
•
The fan impeller is at rest.
Measures are taken to ensure that the accidental, uncontrolled running
of the fan is prevented during maintenance work.
In general, fans should be inspected twice a year, and care should be
taken to ensure that any unusual vibration or sound is investigated as
an urgent matter.
Access to the fan section is via hinged or lift-off panels. Cable entry
must be made through the apertures provided. Screwed glands with
cable restraint devices should be used.
9.2 General Fan Maintenance
Access to the fan is normally gained by opening the hinged access
doors.
Care should be taken to remove any build up of dust (a light vacuum or
light brushing will normally take care of this) Do not use a steam or any
other high pressure cleaners.
Inspect the connection between the fan and unit for any damage or
wear and tear.
9.3 Bearings
The bearings that are fitted will be (unless otherwise specified) “sealed
for life”, therefore consequence maintenance is not required.
Fan bearings are lifelong; up to 40,000 hours of operation. In cases of
heavy duty operation, maintenance intervals are to be established by
the operator.
9.4 Filters
When removing the filter access panels, pay attention to the airflow
direction marked on the panel, this must be replaced to the exact
position prior to being removed. Disposable filters should be checked,
and changed when they become fully laden with dust. Washable filters
should be removed and washed in a mild detergent, flushed with clean
water and allowed to dry before refitting.
9.5 Coils
Coils should be connected to ensure that full counter flow exists i.e. the
entering airflow meets the return connection.
All coils should be connected with the flow at the bottom and the
return at the top unless otherwise advised. Drain and bleed valves are
located on the coil, others may be required in the system pipe-work
depending on the installation.
Frost protection must be incorporated on shut down and fresh air
conditions to avoid coil freezing. Ideally, where the system is at risk of
frost damage, the addition of a proprietary antifreeze solution to the
water is recommended.
Pipe-work connections should be made to the unit using appropriate
techniques, and must be independently supported. The connections
should be pressure tested.