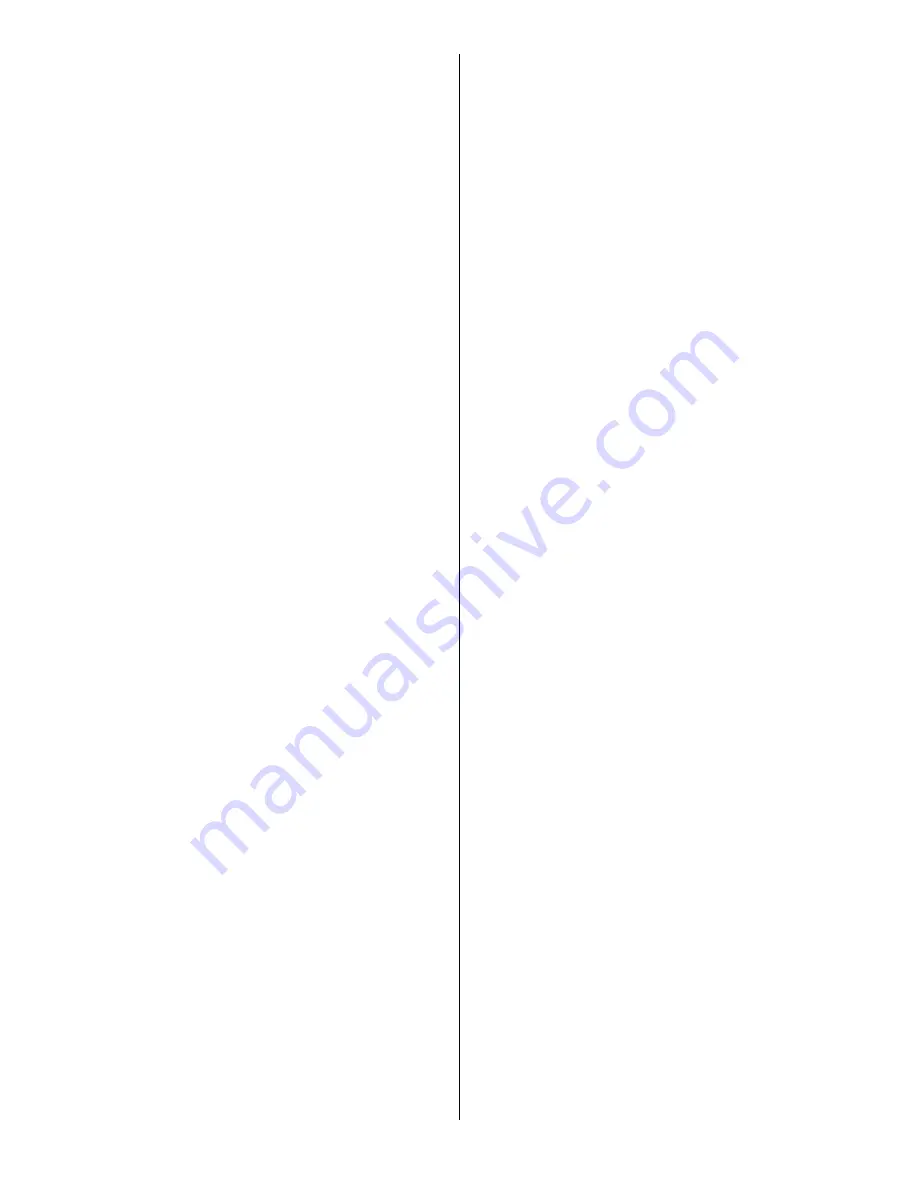
When the feed screw has been run down its full length, shut off
the circulating water BEFORE loosening chuck screws. If this is
not done, the water pressure may push the rods and core barrel
off the bottom of the hole and allow some of the core to drop
out of the bit. When drilling with a short string of rods, always
hold them down with a wrench while running the feed screw
back to prevent the string being raised and the core lost if the
chuck jaws should catch on the rods while returning.
If pieces of core should drop out of the bit and lie sideways in
the hole, damage to the diamond bit will result in running over
them.
When the feed screw has been returned, tighten the chuck
screws, turn on the water and wait for it to start running out of
the hole before drilling is resumed.
In normal ground the machine will run smoothly while drilling,
but as soon as the bit is blocked or the core barrel gets full the
motor will act erratically, alternately slowing down, speeding
up, or even stopping momentarily and shutting off the water
when core breaks tightly.
When this happens, core barrel must be pulled and emptied. As
soon as the core barrel is out of the hole, remove the bit and
reaming shell, then remove the back end connection and empty
the inner tube. If some of the core sticks in the inner tube, tap
tube lightly with the flat of a wooden paddle, taking are not to
bend or dent tube.
It is a good plan to have a trough made up that is long enough to
take the core as it is emptied from the tube so that it does not get
mixed up with cores pulled previously. It is important also that
the core be marked as to depth every time the barrel is emptied,
using wooden blocks in boxes made up for preserving the core.
Normally, very little trouble will be encountered in diamond
drilling. Make sure before starting the drill that water circulation
is established. If water shuts off while drilling, stop immediately
until the cause is found. If the bit is blocked or mudded, at
which time the bit will slow down or stop, rods must be pulled
and the core barrel emptied and cleaned. If it is found that rods
turn easily and water is still circulating after chuck screws have
been loosened and still no water shows at the collar, it is
probable that the bit has run into a seam or small cavity which is
taking up the water and drilling may be safely resumed. Since a
new face is then being cut, start drilling for an inch or so. If drill
operates smoothly, it is safe to open the throttle again.
Generally the drill should be run in the fastest feed gear possible
as long as it operates smoothly and without too much effort.
With a sharp bit, after the hole is collared, the drill may be run
in the 100 feed gear. When the motor begins to labor or slow
down, because of a dull bit or harder ground, gear should be
shifted to a slower rate of feed.
Diamond bits should not be run too far for economic reasons. In
very hard ground, bits should be changed as soon as the motor
labors too hard in slowest feed gear. In abrasive formations, or
where the bits have run to the point where metal is worn away
from the diamonds and there is danger of their being torn out,
the bit should be taken out of service because loose stones may
break up the entire bit.
Drill Rod Recommendations
It should be recognized that size of chuck, chuck jaws and drill
rod do not necessarily govern the size of hole what is to be
drilled. For example, the largest size NW casing may be drilled
into the rock using EW drill rod. The EW rod is run through the
chuck jaws and an EW to NW rod-to-casing sub is used to
connect to the NW casing or starting barrel equipped with a
diamond casing bit.
The foregoing is not recommended as a desirable combination
but frequently it is necessary to improvise in order to expedite
the work. Obviously it is impractical to have every desirable
piece of equipment on all jobs, many of which are isolated from
sources of supply.
With the exception of short holes in easy drilling conditions, do
not use EW rods for drilling AX or larger holes EXCEPT
THROUGH FEED SCREW AND CHUCK!
AW rods have the necessary strength for drilling to any depth up
to 3500 feet; however, when drilling with AW rods and BX or
NX core barrels, be sure to insert one or two rods of
complementary size (BW or NW) immediately behind the core
barrel; otherwise, serious rod vibration or wobble may develop.
Blast Hole and Grout Hole Drilling
When drilling blast or grout holes, where recovery of core is
unnecessary, the use of a short, hard metal protected blast hole
barrel, is recommended. The use of a diamond set reaming shell
is dispensed with and the bit screwed directly into the barrel.
The advantage of using these barrels lies in their greater wearing
qualities as compared to the ordinary core barrel.
Where space is at a premium in blast hole drilling, the use of
two foot rods ahead of the drill is recommended. This is the
most rapid method of drilling with the CP65. Using the water
swivel screwed directly to the back end of the blast hole feed
screw, and with blast hole coupling in the front end, drilling is
simply a matter of adding rods instead of chucking and
changing water swivel in the ordinary manner. The reversible
feature of the CP65 motor is a time-saver in this type of drilling
since the rods, after the joint has been broken, may be
unscrewed and screwed up using the motor.
When drilling in soft ground, it is recommended that the spindle
and gear which gives a spindle speed of 3000 RPM be used. In
harder ground the 1500 RPM set may be used to advantage, but
the highest practical spindle speed is recommended to cut
drilling time to the minimum.
The Grout Pipe Clamp setup is indispensable for grout hole
drilling as the drill is always in alignment when moving on and
off grout pipes.