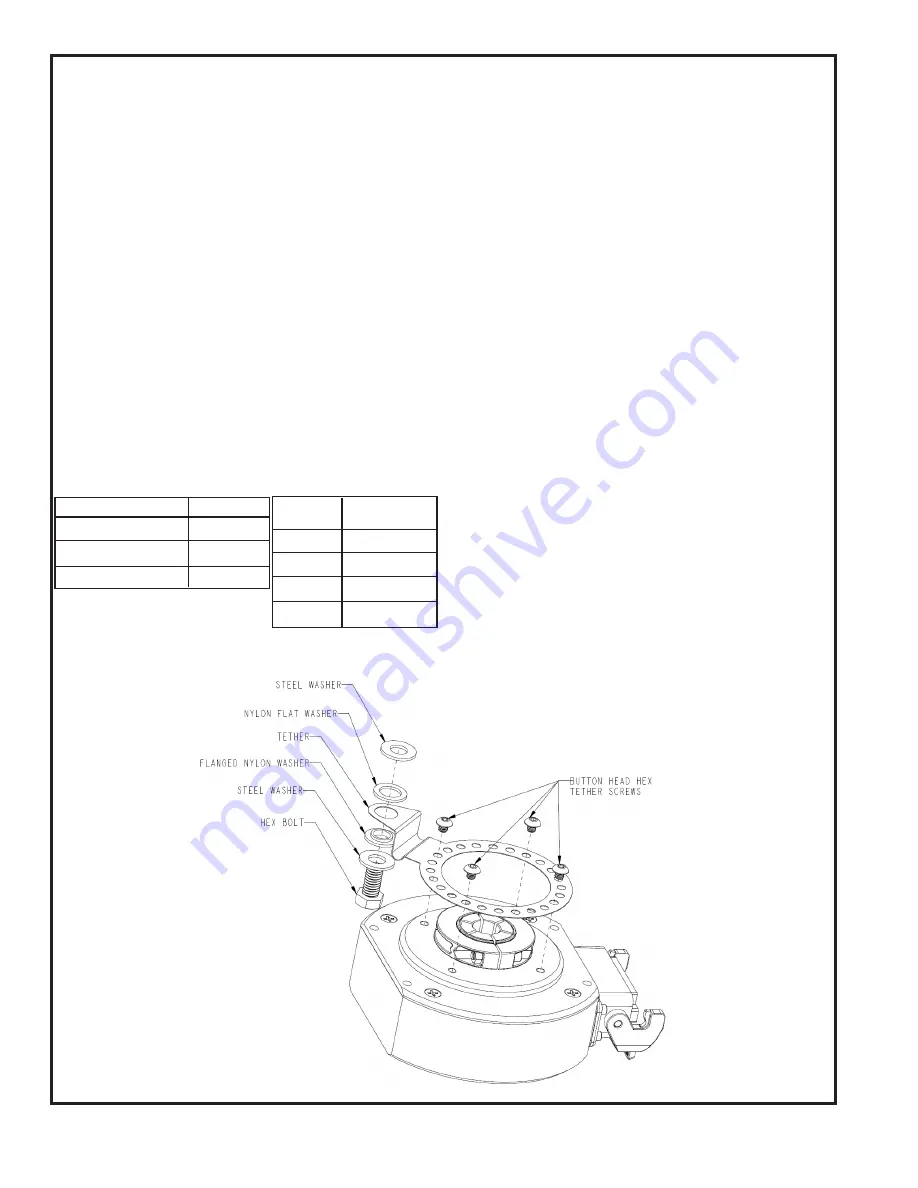
Page 4
A. GENERAL OVERVIEW
The following instructions are meant to assist in proper installation of
Dynapar brand, Series HT55 hollowshaft encoders. The encoder is a
speed and position transducer that when mounted to a rotating shaft,
produces output pulses that are directly proportional to the shaft speed
and direction. The hollowshaft encoder is attached to the motor shaft
by using a clamp down collar. The HT55 can accommodate several
machine shaft diameters by selecting the appropriate bore size. During
installation, certain physical properties associated with the mechani-
cal coupling must be observed to ensure a long operation life of the
encoder.
B. SHAFT EXTENSION
Solid shaft preferred, keyway allowed; flatted shaft must not be used.
The minimum shaft engagement length that will allow support to encod-
er housing is 1.60”. Installations that employ a press-fit or screwed-on
stub shaft adapter should align the stub shaft to 0.002” TIR or less with
a dial indicator
C. TETHER POINT
For general industrial machinery and C-face motor installations, locate
the tether hole at the nominal bolt circle location. The tether holes are
slightly elongated, to allow for hole location tolerance and arcing of the
tether, if the hole location is not flush with the tether surface.
MECHANICAL INSTALLATION
HOLE LOCATION
BOLT SIZE
2.94”(75 mm)
3/8”(9.5 mm)
3.63” (92 mm)
1/2” (12 mm)
2.5”-3.25” (63-82mm) 1/4” (6 mm)
BOLT SIZE RECOMMENDED
TORQUE
1/4”(6mm)
5/16”(8mm
3/8”(9.5mm)
1/2”(12mm)
50-60 in-lbs
70-80in-lbs
100-125 in-lbs
125-150 in-lbs
STEP 1: PREPARATION AND RECOMMENDED TOOLS
Disconnect power from equipment and encoder cable. Ensure that
you have the proper tools. Typical tools that may be needed depend-
ing on the options chosen are:
#2 Phillips Screwdriver; 3mm Hex Wrench; Caliper Gauge; Dial
Indicator Gauge; 3/8”, 1/2” or 1/4” T- handle Wrenches (tether op-
tions); Dynapar M100 encoder tester.
STEP 2: CHECK AND CLEAN THE MATING SHAFT STEEL
Ensure that the mating shaft is within proper tolerances.
Recommended mating shaft diameter tolerances should be nominal
+0.0000”/-0.0005” [0.00 to -0.013mm] and shaft runout TIR should
be under 0.002”.
Clean the mating shaft of any burrs and check that mating shaft
engagement is at least 1.60” inside the encoder shaft. Using a dial
indicator gauge verify that the motor shaft Total Indicated Reading
(TIR) is less than 0.002” [ 0.05 mm].
STEP 4: INSTALL THE TETHER ON ENCODER
Rotate the tether to the required orientation and tighten the tether
arm to the encoder body using the four screws provided .The hollow-
shaft series encoder tethers can be rotated in 15 degree increments
so that connector or cable exit can be conveniently located.
STEP 5: INSTALL WASHERS ON TETHER
Slide the flat nylon washer on the side away from the bend and the
flanged nylon washer on the side of the bend and press them to-
gether until they are fully seated in the tether hole. One steel washer
is to be used on each side of the nylon washer.