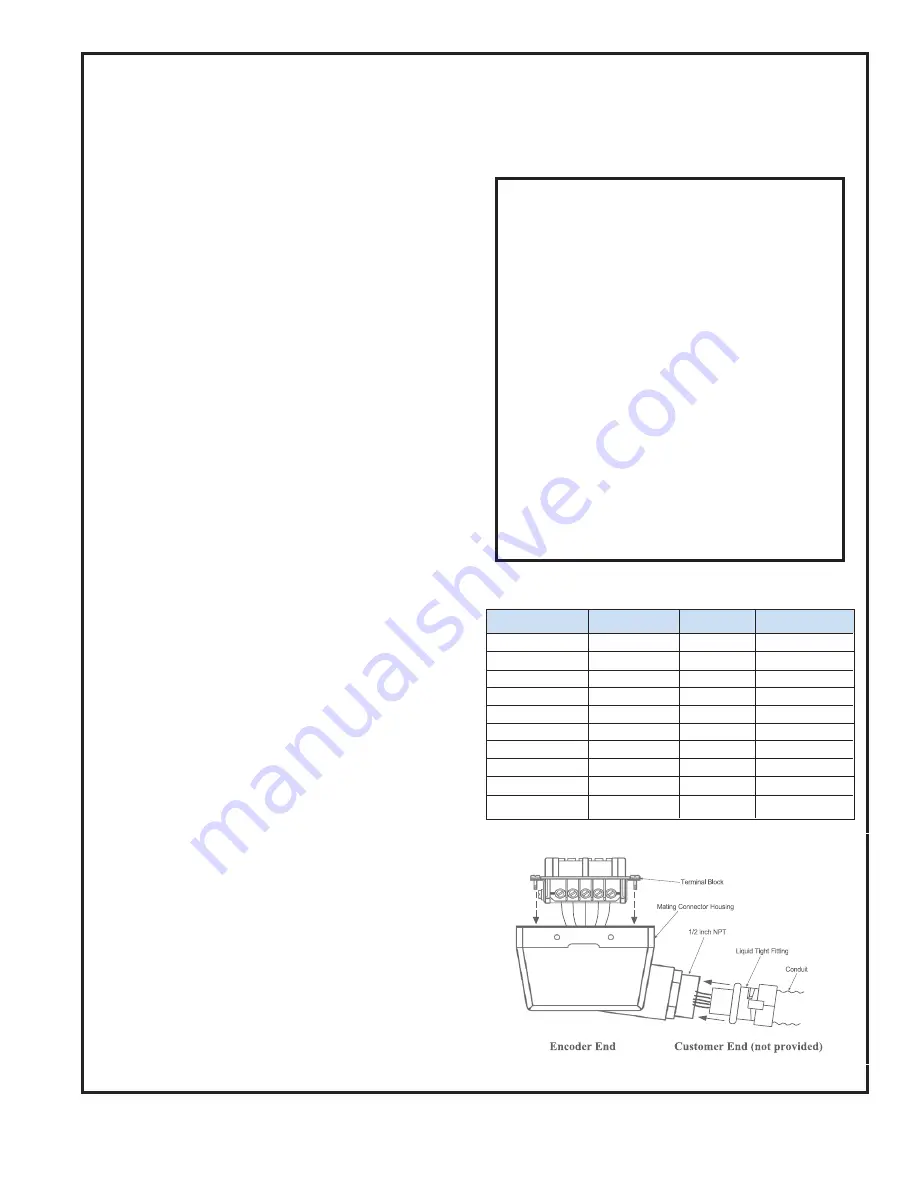
Page 9
1.2 ELECTRICAL INSTALLATION
IT IS VERY IMPORTANT
that the mating connector
and the encoder body be isolated from electrical
ground in the wiring and conduit to prevent motor or
machine shaft eddy currents from going to ground
through the encoder bearings, as this will damage the
bearings over time. To insure that this is being done,
it is suggested that a plastic wiring/conduit adaptor or
non-conductive conduit is used to isolate the connector
from any metallic surface or conductive conduit. Please
see special note under table 1, for proper encoder
connector shielding. Also, to allow for proper encoder
grounding, the motor must be wired and grounded per
your local NEC Requirements.
Electrical connections are made to the sensor
module through a standard 1/2 inch NPT liquid tight
flexible conduit. The nipple length may be changed
to extend the outlet box if desired. Interconnection
cable recommendations are as follows: stranded
copper, 22 through 16 gage, braided or foil with drain
wire shielding 0.05 F maximum total mutual or direct
capacitance, outer sheath insulated. Shrink tubing may
be placed over any wires without insulation. For lengths
over 100 feet, use 18 gage or larger, to a maximum
of 1000 feet. If shielded twisted pair wire is used, do
not cross channels. Keep each pair of complementary
channel outputs together in a single twisted pair (e.g.,
A and A).
IMPORTANT: Reversing power and common will
not damage the unit. However, applying power to
any of the sensor outputs may cause damage.
Grounding:
For applications with high ground
potential differences, DO NOT ground the encoder
through both machine and controls end. Connect
the shield at the controls end only.
NOTE: If the
shield is connected at both ends, grounding
problems that degrade system performance can
result.
CE Grounding Measures
– For best EMC
immunity the cable screen must be grounded on
both encoder and controls end. For cable lengths
longer than 30m or outdoor applications, additional
measures must be implemented to comply with
CE requirements. Connection of the encoder
to DC power supply network is prohibited if CE
compliance is required. CE-compliant products are
tested to EN61326-1 EMC.
In all cases, system CE compliance is ultimately the
responsibility of the manufacturer integrating the
encoder.
1.3 QUICK RELEASE CONNECTOR HOOD WIRING
To install the Quick Release Connector, perform the
following steps.
1.Remove the four screws from the mating connector
housing that hold the terminal block in place. Re-
move terminal block from housing.
2.Insert wiring through liquid tight flexible seal and
mating connector housing. Leave enough wire ex-
posed to comfortably reach the terminal block. Wire
to terminal block according to wire code in Table 1.
A similar wiring list is attached to enclosure.
3.Tighten Liquid Tight fitting on housing. OPTIONAL:
In some hostile environments, seal between con-
nector body and Sensor Module can be improved
by smearing a sealant (silicone grease, etc.) on the
neoprene seal of the connector.
4. Mate connector into place on sensor mount and
snap the two latches into place. If only one sensor is
being installed, ensure cover plate is installed over
other sensor hole.
Table 1. Signal Coding Table
* Index (Z) optional. See Ordering Information
Common
B
A
Z*
No Connection
Vcc (5-26 VDC)
B
A
Z*
Shield
1
2
3
4
5
6
7
8
9
10
Black
Green
Blue
Violet
N/A
Red
Yellow
Gray
Orange
Braid
Signal Connector Pin Pigtail Cable MS 3102E18-IT#
F
B
A
C
E
D
I
H
J
G
Quick Release Connector Hood Wiring
To install the Quick Release Connector, perform the following steps:
1. Remove the four screws that hold the terminal block in place from mating connector hood. Remove the terminal block from the
hood.
2. Insert wiring through the liquid tight flexible seal and the mating connector hood. Enough wire should be left exposed to
comfortably reach the terminal block.
3. Wire to terminal block according to the wire code in Table 1. A similar wiring list is attached to the enclosure.
4. Replace the terminal block in the connector hood. Insert and tighten the four mounting screws.
5. Tighten the liquid tight fitting on the housing.
6. OPTIONAL: In some hostile environments, seal between connector body and sensor module can be improved by applying a
Figure 7: Industrial Latching Connector
Uninstalling the Encoder
1. Loosen the 10-32 socket head cap screws in split shaft collar. Loosen 10-32 x • hex bolt attached to the bracket or bolt on
the motor. Carefully remove the encoder and torque arm assembly.
2. Perform the installation steps in reverse order.
Returning Equipment to Dynapar
If it is necessary to return the unit for repair or replacement, a Return Goods Authorization (RGA) number must be obtained from a
factory representative before returning the equipment to our service department. When returning an instrument for service, the
following information must be provided before we can attempt any repair.
1. Instrument model and serial number.
2. User’s name, company, address, and phone number.
3. Malfunction symptoms.
4. Description of system.
5. Returned Goods Authorization number.
Please consult the factory for shipping instructions.