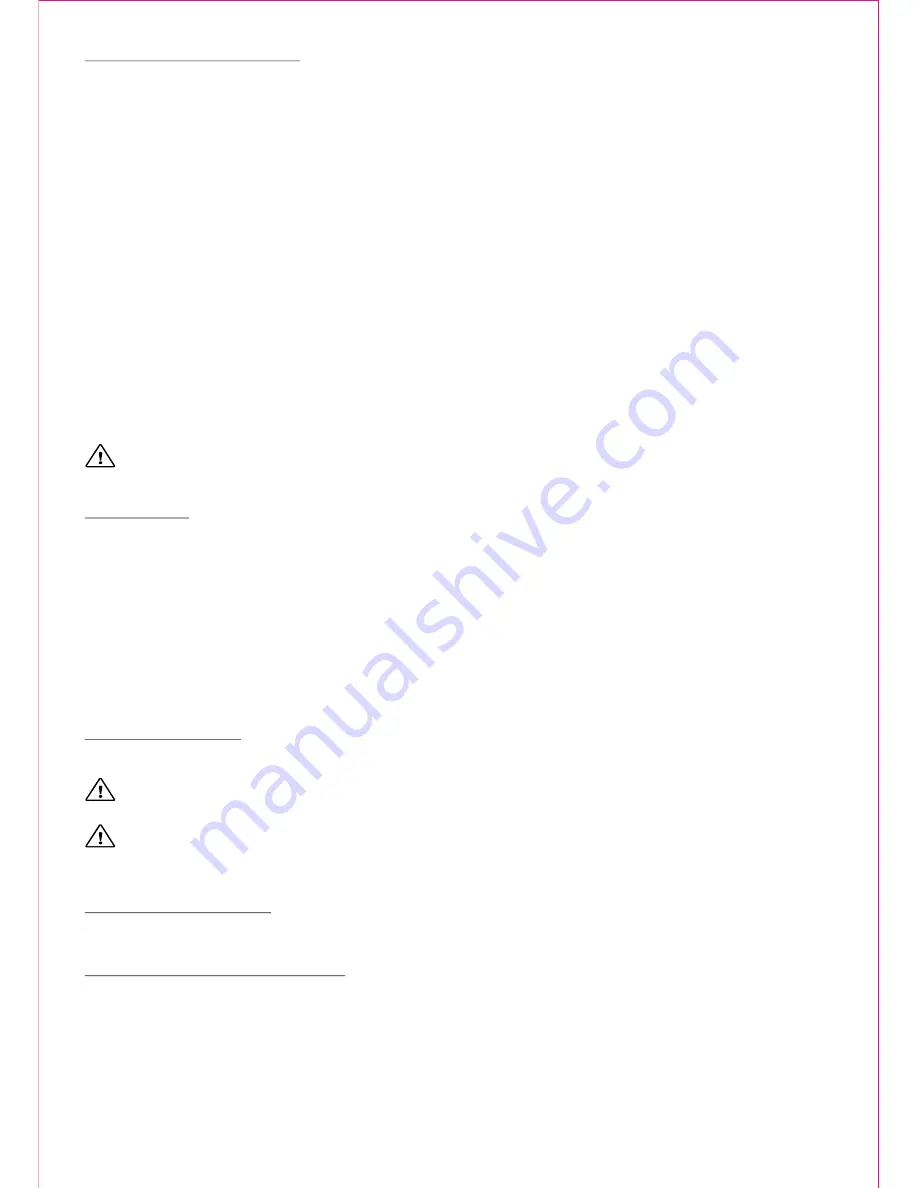
BLADE TRACK ADJUSTMENT
1.Open the blade guard.
2.Remove the blade guide assemblies (top and bottom)
3.Loosen the hex head screw in the tilting mechanism to a point where it is loose but snug.
4.With the machine running, adjust both the set screw and blade tension knob simultaneously to keep
constant tension on the blade. The set screw and blade tension knob are always turned in opposite
directions, when one is turned clockwise the other is turned counterclockwise. The blade is tracking properly
when the back side just touches the shoulder of pulley or a slight gap appears near the center line of the
pulley. Care should be taken not to over tighten the saw blade since this will give a false adjustment and limit
life of the blade.
5.Tighten the hex head screw in tilting mechanism. IMPORTANT: Sometimes in trying to make this critical
adjustment it is possible to cause the basic setting to be misaligned. Should this occur, proceeds as follows:
a.Loosen the set screw and back it out as far as it can go and still remain in the threaded hold.
b.Turn the hex head screw clockwise until it stop (do not tighten).
c.Turn the set screw clockwise until it bottoms, then continue for half a turn and check the tracking by turning
on the machine.
d.If further adjustment is required, go back to step 4.
6.Turn off power to the machine.
7.Replace the blade guide assemblies it may be necessary to loosen the blade tension a lightly.
8.Adjust the vertical position of blade guide bearing assemblies so that the back side of the blade just touches
the ball bearings.
9.Make a final run to check tracking. It required, touch up adjustment (See stop 4)
10.Replace the blade guards.
MAINTENANCE
CAUTION: MAKE CERTAIN THAT THE UNIT IS DISCONNECTED FROM THE POWER SOURCE
BEFORE ATTEMTING TO SERVICE OR REMOVE ANY COMPONENT!
LUBRICATION
Lubricate the following components using SAE-30 oil as noted.
1.Driven pulley bearing: 6-8 drops a week.
2.Vise lead screw: as needed.
3.The drive gears run in an oil bath and will not required a lubricant change more often than once a year,
unless the lubricant is accidentally contaminated or a leak occurs because of improper replacement of the
gear box cover. During the first few days of operation, the worm gear drive will run hot. Unless the temperature
o
exceeds 200 F, there is no cause for alarm.
4.The following lubricants may be used for the gear box:
a)Atlantic Refinery Co., Mogul Cyl. Oil
b)Cities Service Optimus No.6
c)Gulf Refinery Co Medium Gear Oil
d)Pure Oil co. Park Clipper
Circuit Requirements
NOTE: Item# 155793 is prewired for 110V operation. If you plan to operate your machine at 220V, the
motor & pump must be rewired by a qualified electrician.
WARNING: Electrocution or fire could result if machine is not grounded and installed in
compliance with electrical codes. Compliance MUST be verified by a qualified electrician!
CAUTION: Serious personal injury could occur if you connect the machine to power before
completing the setup process. DO NOT connect the machine to the power until instructed in this
manual.
Full Load Amperage Draw
Amp Draw at 110V (prewired)..........16 Amps
Amp Draw at 220V..........8 Amps
Power Supply Circuit Requirements
You MUST connect your machine to a grounded circuit that is rated for the amperage given below. Never
replace a circuit breaker on an existing circuit with one of higher amperage without consulting a qualified
electrician to ensure compliance with wiring codes.
If you are unsure about the wiring codes in your area
or you plan to connect your machine to a shared circuit, consult a qualified electrician.
Minimum Circuit Size (110V)..........20 Amps
Minimum Circuit Size (220V)..........15 Amps
7 OF 15