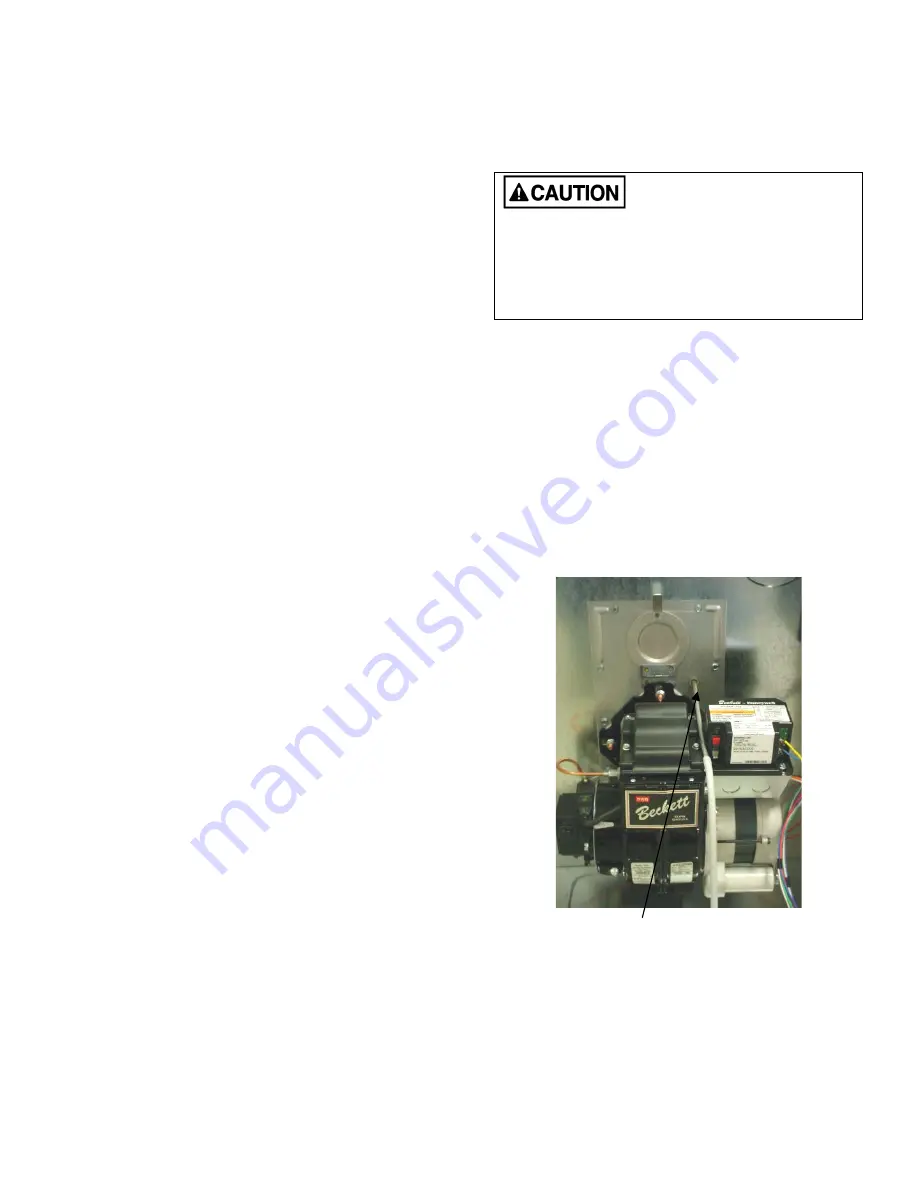
4. AIR CONDITIONING APPLICATIONS
If the furnace is used in conjunction with air conditioning,
the furnace shall be installed in parallel with or upstream
from the evaporator coil to avoid condensation in the
heat exchanger. In a parallel installation, the dampers or
air controlling means must prevent chilled air from
entering the furnace. If the dampers are manually
operated, there must be a means of control to prevent
the operation of either system unless the dampers are in
the full heat or full cool position. The air heated by the
furnace shall not pass through a refrigeration unit unless
the unit is specifically approved for such service.
The blower speed must be checked and adjusted to
compensate for the pressure drop caused by the
evaporator coil. Refer to Appendix B for recommended
wiring and electrical connections of the air conditioning
controls.
5. COMBUSTION AIR
If the furnace is installed in a closet or utility room, two
openings must be provided connecting to a well-
ventilated space (full basement, living room or other
room opening thereto, but not a bedroom or bathroom).
One opening shall be located above the level of the
upper vent opening and one opening below the
combustion air inlet opening in the front of the furnace.
Each opening shall have a minimum free area of 1½
square inches per 1,000 Btu/h of total input rating of all
appliances installed in the room.
For furnaces located in buildings of unusually tight
construction, such as those with high quality weather
stripping, caulking, windows and doors, or storm sashed
windows, or where basement windows are well sealed, a
permanent opening communicating with a well ventilated
attic or with the outdoors shall be provided, using a duct
if necessary. The duct opening shall have a free area of
1½ square inches per 1,000 Btu/h of total input rating of
all appliances to be installed. When a furnace is installed
in a full basement, infiltration is normally adequate to
provide air for combustion and draft operation. Furnace
rooms under 65m³ (700 ft³) should automatically be
treated as confined space.
6. CHIMNEY VENTING
The flue pipe should be as short as possible with
horizontal pipes sloping upward toward the chimney at a
rate of one-quarter inch to the foot. The flue pipe should
not be smaller in cross sectional area than the flue collar
on the furnace. The flue pipe should connect to the
chimney such that the flue pipe extends into, and
terminates flush with the inside surface of the chimney
liner. Seal the joint between the pipe and the lining. The
chimney outlet should be at least two feet above the
highest point of a peaked roof. All unused chimney
openings should be closed. Chimneys must conform to
local, provincial or state codes, or in the absence of local
regulations, to the requirements of the National
Building Code.
NOTE: THE FURNACE IS APPROVED FOR
USE WITH TYPE L VENT OR EQUIVALENT.
CHIMNEY VENTED VERSIONS
OF THE
FURNACE MUST BE CONNECTED TO A
FLUE HAVING SUFFICIENT DRAFT AT ALL
TIMES TO ENSURE SAFE AND
PROPER
OPERATION OF THE APPLIANCE.
NOTE: THE RECOMMENDED FLUE DRAFT
PRESSURE IS -0.02 IN. W.C. (SEE FIG 2.)
The flue pipe must not pass through any floor or
ceiling, but may pass through a wall where suitable
fire protection provisions have been installed. Refer
to the latest edition of CAN/CSA B-139 for rules
governing the installation of oil burning equipment.
In the United States, refer to the latest edition of
NFPA 31 for regulations governing the installation of
oil burning equipment.
See appendix A for burner set-up.
Fig. 2: Checking Over-Fire Draft.
Over-fire draft access port.
7. BAROMETRIC DAMPER CONTROL.
The barometric damper control, also known as a
draft regulator, is used on conventional chimney
venting only. This control automatically maintains a
constant negative pressure in the furnace to obtain
maximum efficiency. It ensures that proper
pressures are not exceeded. If the chimney does not
develop sufficient draft, the draft control cannot
4
Содержание O4HD-091A-12-FB
Страница 34: ...34...