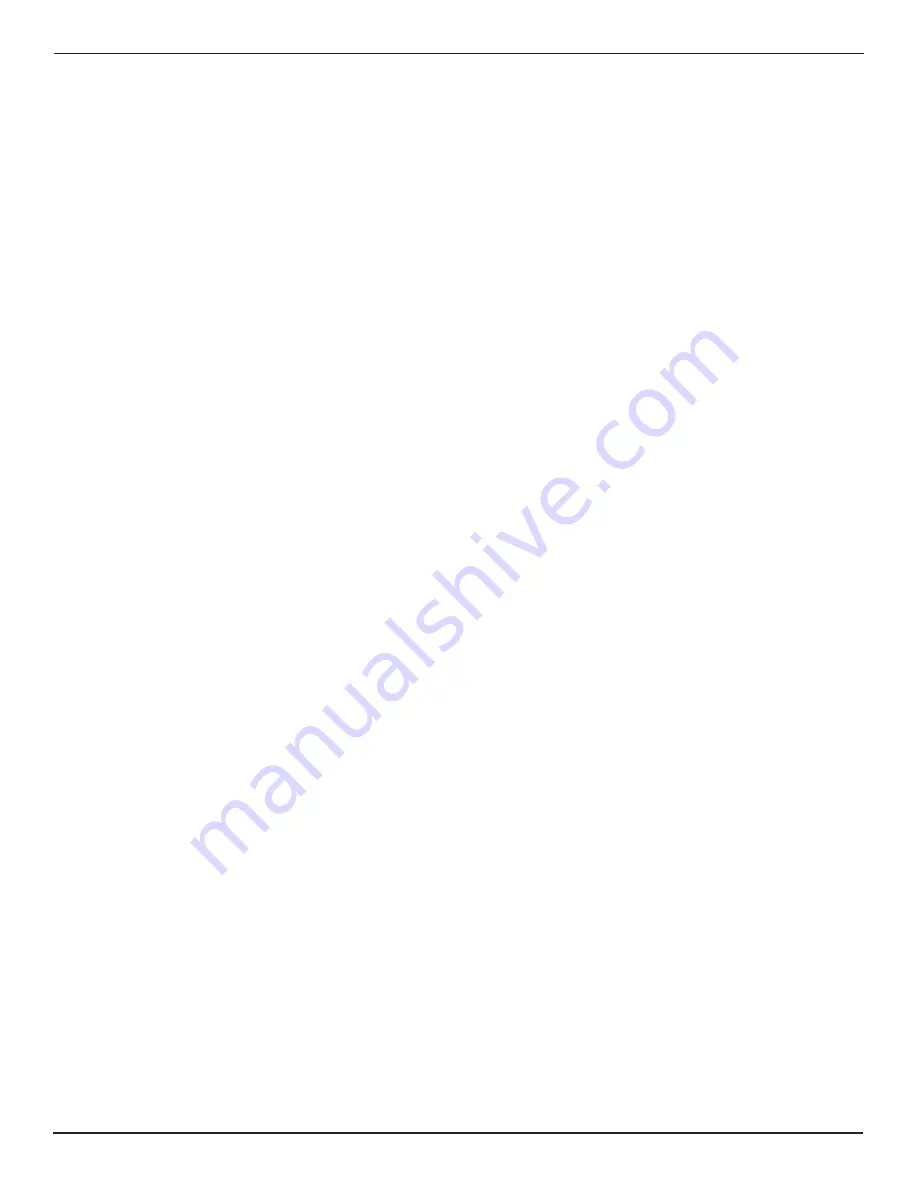
10
© 2021 Nordson Corporation
System Operation
See Figure 5. Coating material enters the pump inlet through a low-pressure gravity or
siphon feed system. The pressurized coating material passes through the manifold and
then is either routed to the spray system through the outlet fitting or, if the two-way ball
valve is opened, through the drain rod to a waste container.
Fluid returning from the spray system flows through the return fitting on the rear side of
the panel, through the 3-way ball valve, back pressure regulator, and back to the supply.
The three-way ball valve can also route the return fluid flow to the drain rod.
The back pressure regulator maintains the desired fluid pressure within the spray system
during normal operation. Depending on the application, it may be removed from the panel
and installed in a different location in the spray system.
The pressure relief valve protects the pump and system components from excessive
pressure.
•
It is set for lacquer coating systems to open at 89.6−91.4 bar (1300−1325 psi). This is
the factory setting.
•
For CleanSpray systems, it must be set to open at 51.7−55.2 bar (750−800 psi). Refer
to
Pressure Relief Valve Adjustment
Содержание EP2
Страница 4: ... 2021 Nordson Corporation 1072608 04 ii Change Record ...
Страница 11: ...7 EP2 Pump System 2021 Nordson Corporation 1072608 04 1 2 3 4 3 5 Figure 1 Safety Label Location ...
Страница 32: ...28 EP2 Pump System 2021 Nordson Corporation 1072608 04 This page is intentionally left blank ...
Страница 38: ...34 EP2 Pump System 2021 Nordson Corporation 1072608 04 ...