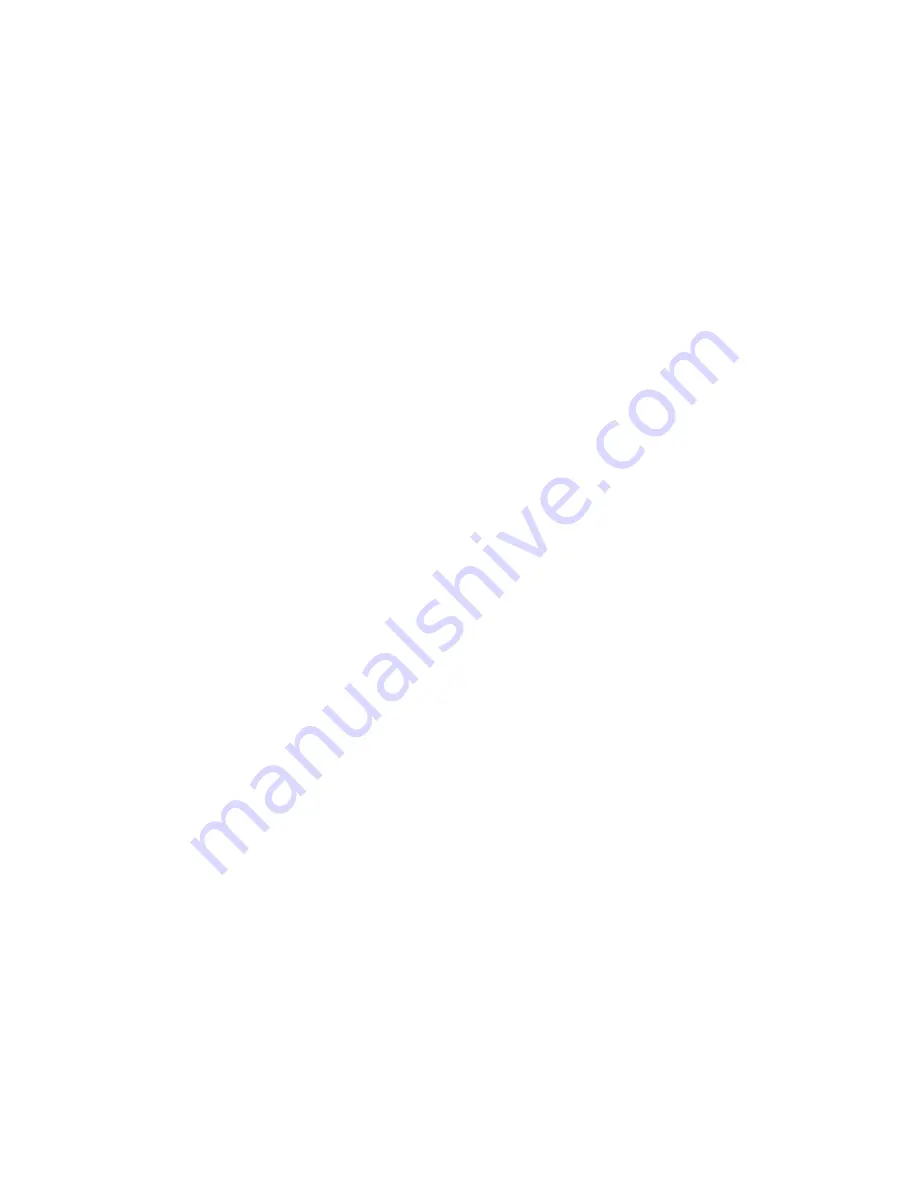
05/16/2014 30
NI216
Troubleshooting
Comment
– this section assumes the service technician is recently familiar with all sections or pages of this
installation and operating manual up through this page. To emphasize only a few, there are many installation
and operating items detailed which could affect the system and if not initially done correctly could bring the
service technician to this page.
Correct system installation design, piping, water flow, Btu/h absorption of the various components, air
handler CFM, etc.
Correct water fill and purge
Electrical hookup
Field setup
Start up suggestions
System logic description
– the Control Sequence Information section provides considerable information on the
characteristics of this controller. Correct field setup or programming, water flow, and approximate correct
outdoor temperature reading become key to most of these sequences.
Various voltage checks
– it’s always helpful to check various key voltage points. The externals of this NorAire
controller follow HVAC terminology and basic design concept. The controller 5V power supply can be checked
at the sensor terminal block Red to C.
Anti-cycle delay (ACD) –
see Control Sequence section, relates action at the end of ACD.
Option PC software CD and provided USB cable
– see Start Up section. This can be a very valuable
diagnostic tool plus it allows the opportunity for changing some of the delay times to shorten testing wait times.
Notice the warning paragraph, must return default values
Properly evaluate boiler staging OT disables
Alt-A history
could be a valuable piece of information. At the beginning of each ACD (green power
light blinking) the reason for triggering ACD is written out on a pull-down screen. This will show the
history of the last five ACD’s, the first is written over for a rotating list of five.
Hint, testing the control board by itself could be very difficult
– powering up the board and providing stat W
or Y input will trigger a series of sequences which will require external limit or temperature sensor information.
Without these proper connections and external components, the board will go into various error or alarm modes.
Flow sensor
RT temp sensor – compressor no response, low water flow
STc temp sensor – ODT mode error, compressor no response, low water flow
OT temp sensor – within reasonable range
Temperature sensor sequence usage:
RT – low flow, tank changeover, GPM calculation
STc – freeze, low flow, ODU mode, cool limit, heat limit
STh – Electro-Boiler target
Bad temperature sensor, power on LED
– software detected no value, cannot detect incorrect value. This
green LED blinks indicating which sensor.
RT – one blink every 2 seconds
44° F (1° C)
STh (above boiler) – two blinks every 2 seconds
110° F (43° C)
OT – three blinks every two seconds
OT mid value minus 4° F (2° C)
STc (heat exchanger out) – four blinks every 2 seconds
44° F (1° C)
Bad sensor forced default value – the above right column number
Nuisance service LED low flow or alarm compressor no response LED –
both of these sequence temperature
calculations can be disabled with PC setup software. Entering a 0 digit cancels these sequence tests.
Содержание NC-FE series
Страница 22: ...05 16 2014 20 NI216 ...
Страница 49: ... 0 1 2 3 4 5 6 3 0 1 40 1 5 3 1 7 8 8 4 5 43 15 ...
Страница 50: ... ...
Страница 51: ... ...
Страница 52: ... ...
Страница 53: ... ...
Страница 54: ... ...
Страница 55: ... 01 2 ...
Страница 56: ... 0 0 1 0 2 1 3 4 4 5 0 6 ...
Страница 57: ... ...
Страница 60: ......
Страница 63: ...XX036 ...
Страница 64: ...XX036 ...