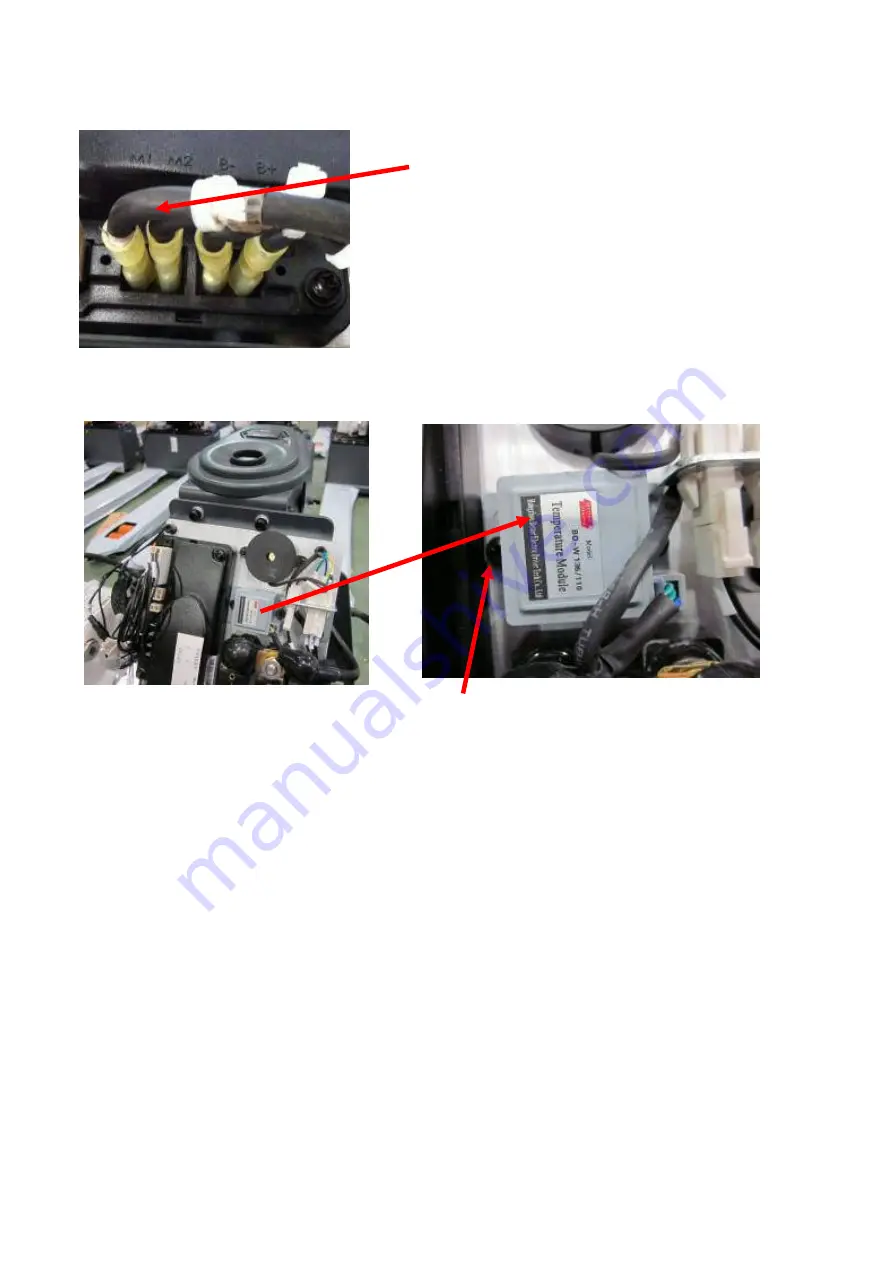
46
Two plug terminals (M1 and M2) are provided for the
connections to the motor field winding. Do not allowed to
access anti-Line, otherwise the motor will be reversed.
REPLACE THE PROTECT MODULE
When the temperature of the motor is more than 115
O
C, the protect module will give a signal to the
controller, then driving speed will automatically change to low-speed mode. After the temperature
reduces to 115
O
Dismantle the screw and the plug, then you can dismantle the protect module and replace it
C, the speed mode will change to normal mode.
If one line of the cable open circuit, the driving speed will be slowly.
https://forklift-manuals.jimdofree.com