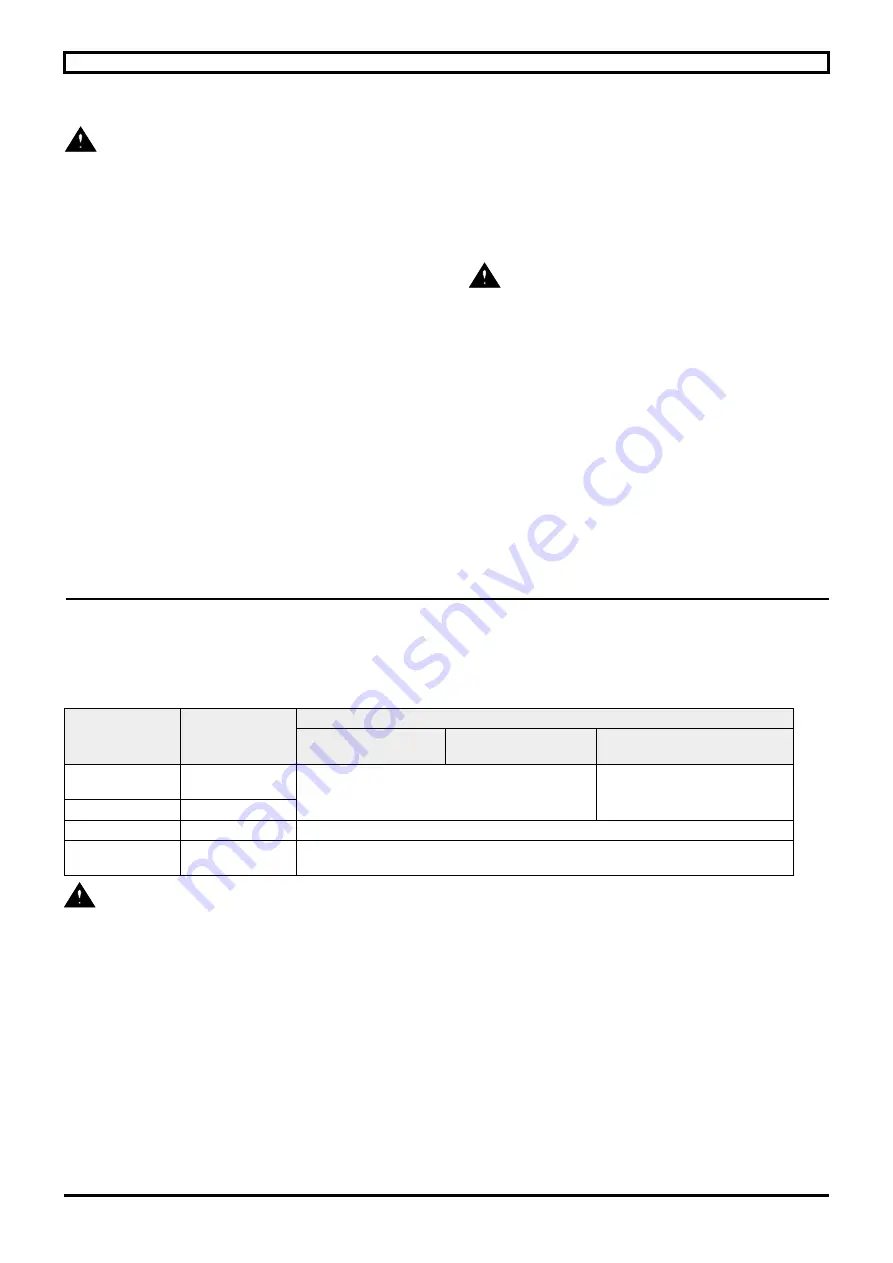
17
CONNECTIONS
Installation guide Powerdrive MD Smart Equipment
5704 en - 2021.10 / b
3 - CONNECTIONS
• All connection work must be performed by
qualified electricians in accordance with the laws in force
in the country where the drive is installed. This includes
grounding to ensure that no directly accessible part of
the equipment can be at the AC supply voltage or any
other voltage which may be dangerous.
• The drive must be supplied via an approved circuit-
breaking device so that it can be powered down safely.
• The optional switch supplied with the drive does
not isolate the drive input busbars. It must without
fail be associated with a circuit-breaking device in the
switchboard.
• The equipment power supply must be protected
against overloads and short-circuits.
• Check that the voltage and current of the drive, the
motor and the AC supply are compatible.
• The voltages on the connections of the AC supply, the
motor, the braking resistor or the filter can cause fatal
electric shocks. The protective plates supplied with the
drive must always be installed correctly to protect the
user against direct electric shocks.
• Only one permanent magnet motor can be connected
to each drive output. It is advisable to install a circuit-
breaking device between the permanent magnet motor
and the drive output to eliminate the risk of hazardous
voltage feedback when performing maintenance work.
• Also comply with the recommendations in section 7.
3.1 - Power connections
3.1.1 - General
Details of the power connections for the
Powerdrive MD Smart
equipment are given in the Electrical plan THxxxxx.
The
Powerdrive MD Smart
with ratings higher than 570T are
obtained by connecting lower ratings in parallel.
• The cables for each of the motor U/V/W phases
must be distributed evenly over the U/V/W connection
plates in each drive cabinet.
3.1.2 - Connection terminal characteristics
The following characteristics only describe an equipment containing a single drive, from 1000T to 1400T and from 270TH to
1500TH.
For highly-specific equipment (high power > 1400T, DC BUS, equipment with several drives), please refer to electrical plan
THxxxxx for information on the connection of power terminals to the mains supply.
Functions/
connections
Marking
Type of connection and tightening torque
100T to 150T
180T to 270T
340T to 1400T
270TH to 1500TH
AC power supply
L1, L2, L3,
or R, S, T
M10 screw bolt - 20 Nm
M12 screw bolt - 30Nm
Motor outputs
U , V, W
Earth
PE
M10 bolt - 20 Nm
Braking resistor
(1)
BR1, BR2
M8 bolt - 12Nm
Do not exceed the indicated maximum tightening torque.
(1) If the braking transistor option is installed.