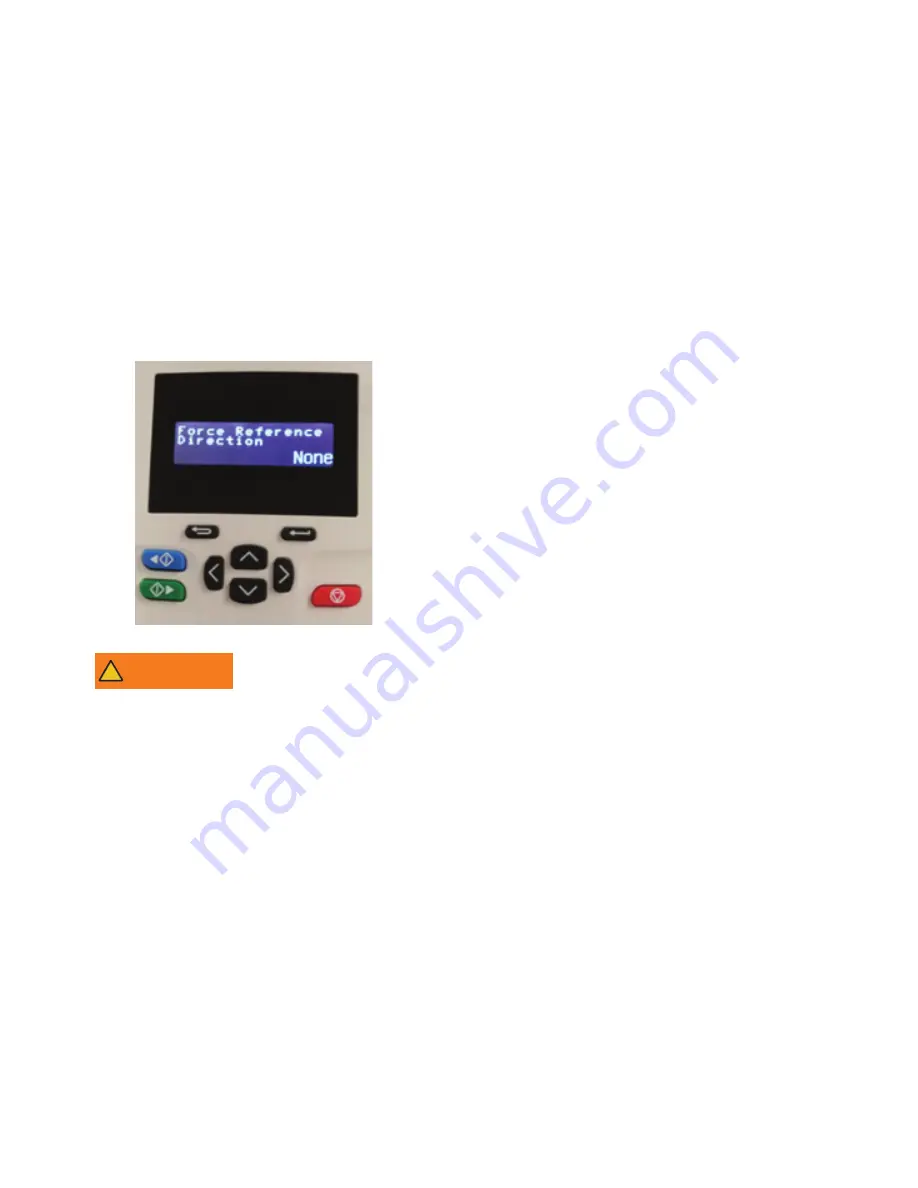
www.usmotors.com
8
ID300/302 Integrated Motor Drive |
Start Up Tips for the ID300/302
6. Press the Left arrow key to move the cursor to the digit you want to highlight. Use the Up or Down
arrow keys to increase or decrease the value.
7. Press the Enter key to save the value, if you are in the
0 Menu.
•
Note:
If you are in any other menu (menu 1-22), then there is another step to save the value
when power is removed.
Press the
Down
arrow key until you see the
0 Menu
. Then, press the Enter button. The display
will start flashing. Press the Up arrow key to change the display from
No Action
to
Save
Parameters.
Press the
Enter
button and then the
Red
button. The display will change to
No Action,
which
means your changes have been saved. Press the
Escape
button to exit
Programming Mode
.
1.8 Example Setting Change: Parameter 0.008 - Force Reference Direction
Force Reference Direction changes the direction
of the motor rotation.
None
is the default. Other
than
None
, there are two options for the different
rotations of the motor. As the motor leads are not
easily accessible in the controller terminal box, this
step replaces reversing any two of the motor leads
to change direction.
Press the
Enter
key to save all changes. Then,
press the
Escape
key.
• The control circuits are isolated from the power circuits in the ID300/302 by single insulation only.
The installer must ensure that the external control circuits are insulated from human contact by at
least one layer of insulation (supplementary insulation) rated for use at the AC supply voltage.
•
If the control circuits are to be connected to other circuits classified as Safety Extra Low Voltage
(SELV) (e.g., to a personal computer), an additional isolating barrier must be included in order to
maintain the SELV classification.
• If any of the digital inputs (including the drive enable or STO inputs) are connected in parallel with
an inductive load (i.e., contactor or motor brake) then suitable suppression (i.e., diode or varistor)
should be used on the coil of the load. If no suppression is used, then over voltage spikes can
cause damage to the digital inputs and outputs on the ID300/302.
• When the ID300/302 is controlled remotely, avoid routing of power cables and control cables in
close proximity with each other.
• Ensure the logic polarity is correct for the control circuit to be used. Incorrect logic polarity could
cause the motor to be started unexpectedly. Positive logic is required for the ID300/302.
WARNING
!