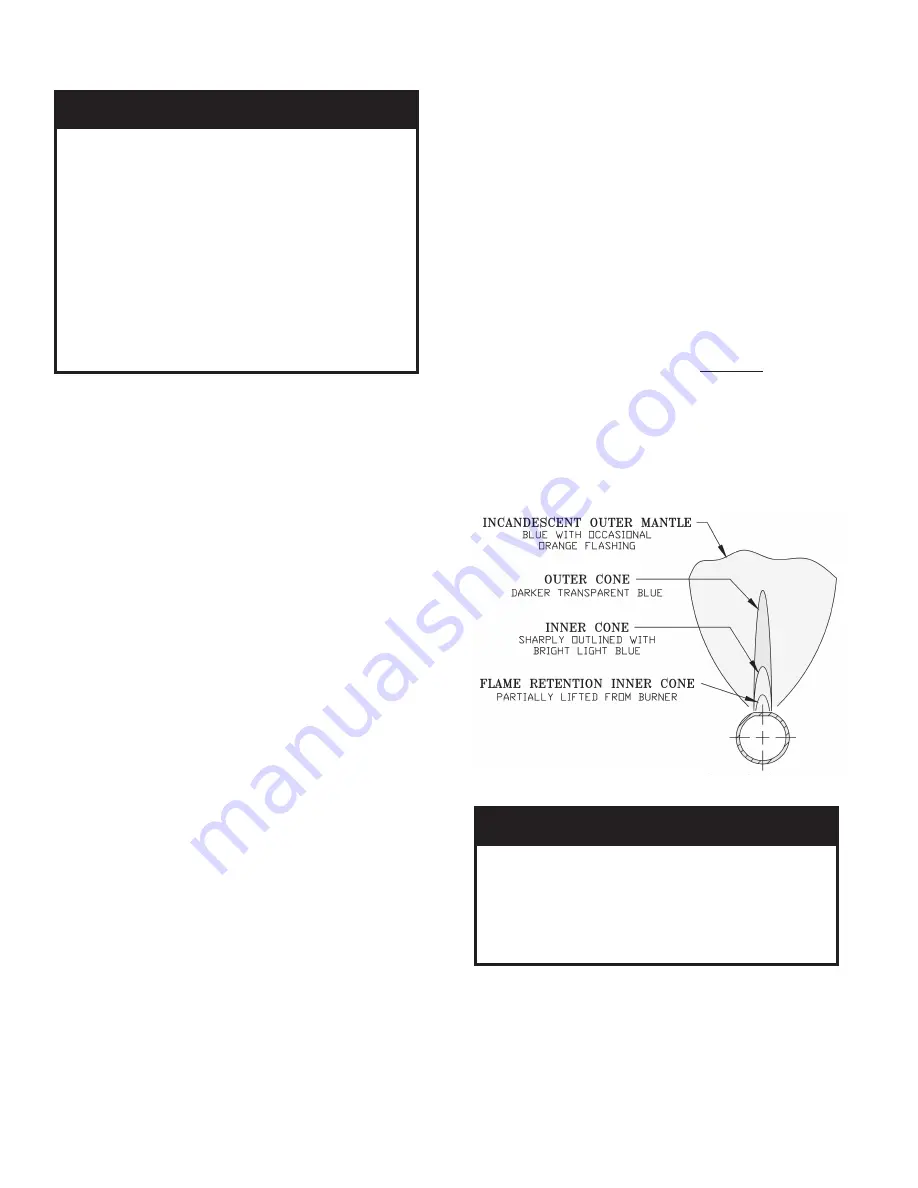
18
Figure 17: Main Burner Flame
D
.
Check Gas Input to Boiler
For minor input changes readjust Regulator Gas
Valve to increase or decrease manifold pressure
to obtain corresponding increase manifold
pressure more than 0.3" of water to obtain rated
input, remove orifices and drill one size larger.
Reinstall and recheck input rate.
b. Additional Check on Input - Since input is a
function of heating value, specific gravity, and
volume of gas flow contact your utility for the
first two items in order to utilize the formula
below. The gas meter should then be clocked for
three (3) minutes with stop watch and
substituting the appropriate values in the formula
below, determine what the gas flow should be in
this 3 minute period to give the input shown on
the Rating Label:
Gas Input cu. ft. __________Btuh Input_________
per 3 min. = Heating Value Multiplier from
of Gas X Table 5
(Btu / cu. ft.)
E
C
I
T
O
N
t
a
n
o
i
t
a
l
l
a
t
s
n
i
r
o
f
t
l
i
u
b
s
r
e
l
i
o
b
A
-
G
C
a
e
s
e
v
o
b
a
t
e
e
f
0
0
0
,
2
n
a
h
t
r
e
t
a
e
r
g
s
e
d
u
t
i
t
l
a
e
c
u
d
e
r
o
t
d
e
c
i
f
i
r
o
y
l
l
a
i
c
e
p
s
n
e
e
b
e
v
a
h
l
e
v
e
l
t
e
e
f
0
0
0
,
1
r
e
p
t
n
e
c
r
e
p
4
e
t
a
r
t
u
p
n
i
s
a
g
s
a
G
l
e
u
F
l
a
n
o
i
t
a
N
e
h
t
r
e
p
l
e
v
e
l
a
e
s
e
v
o
b
a
2
.
1
.
8
n
o
i
t
c
e
S
,
1
.
3
2
2
Z
I
S
N
A
/
4
5
A
P
F
N
,
e
d
o
C
s
l
e
d
o
m
r
e
l
i
o
b
e
d
u
t
i
t
l
a
h
g
i
H
.
F
x
i
d
n
e
p
p
A
d
n
a
e
h
t
n
i
t
i
g
i
d
d
r
i
h
t
e
h
t
y
b
e
l
b
a
i
f
i
t
n
e
d
i
e
r
a
:
l
e
b
a
l
g
n
i
t
a
r
e
h
t
n
o
x
i
f
f
u
s
r
e
b
m
u
n
l
e
d
o
m
.
t
f
0
0
0
2
n
a
h
t
s
s
e
l
:
2
_
_
-
A
O
_
G
C
n
o
i
t
a
v
e
l
e
.
t
f
0
0
0
5
o
t
0
0
0
2
:
5
_
_
-
A
O
_
G
C
n
o
i
t
a
v
e
l
e
1. Input Rate and Maximum Inlet Pressure shown on
Rating Label must not be exceeded. Inlet pressure
must not be lower than minimum inlet pressure
shown on Rating Label.
2. All Rate checks and all adjustments are to be made
while boiler is firing - all other appliances connected
to the same meter as the boiler must be off.
3. With boiler off, water Manometer or water column
gauge should be connected to a shut-off cock
installed in the 1/8" outlet pressure tap in the gas
valve (See Figure 14). By installing gas cock
upstream of manometer, gas pressure can be
introduced gradually - without shut-off cock; surge
of pressure when boiler is turned on, could blow
liquid out of manometer. Replace plug in gas valve
when rate check is finished.
4. LP Gas Input:
Adjust Regulator on Gas Valve so that manifold
pressure is 10 inches water column. Turning
Regulator Adjusting Screw Clockwise increases
pressure. Counterclockwise rotation decreases
pressure.
5. Natural Gas Input
a. Appx. Input - Adjust regulator on Gas Valve so
that manifold pressure is three and a half (3½)
inches water column (three inches water column
for high altitude). Turning Regulator Adjusting
Screw Clockwise increases pressure,
Counterclockwise rotation decreases pressure. If
more accurate check on input is necessary see
(b) .
N
O
I
T
U
A
C
t
n
e
m
n
o
r
i
v
n
e
n
a
n
i
r
e
l
i
o
b
s
i
h
t
g
n
i
t
a
r
e
p
o
d
i
o
v
A
y
r
d
,
s
r
e
b
i
f
n
o
i
t
a
l
u
s
n
i
e
s
o
o
l
,
t
s
u
d
w
a
s
e
r
e
h
w
s
i
r
e
l
i
o
b
f
I
.
t
n
e
s
e
r
p
e
r
a
.
c
t
e
,
t
s
u
d
l
l
a
w
r
e
n
r
u
b
e
h
t
,
s
n
o
i
t
i
d
n
o
c
e
s
e
h
t
r
e
d
n
u
d
e
t
a
r
e
p
o
d
n
a
d
e
n
a
e
l
c
e
b
t
s
u
m
s
t
r
o
p
d
n
a
r
o
i
r
e
t
n
i
.
n
o
i
t
a
r
e
p
o
r
e
p
o
r
p
e
r
u
s
n
i
o
t
y
l
i
a
d
d
e
t
c
e
p
s
n
i
E.
Check Main Burner Flame.
See Figure 17. Flame
should have a clearly defined inner cone with no yellow
tipping. Orange-yellow streaks caused by dust should
not be confused with true yellow tipping.
Содержание CG-A 30
Страница 16: ...16 Figure 15 Operating Instructions ...
Страница 17: ...17 Figure 16 Lighting Instructions ...
Страница 20: ...20 ...
Страница 21: ...21 ...