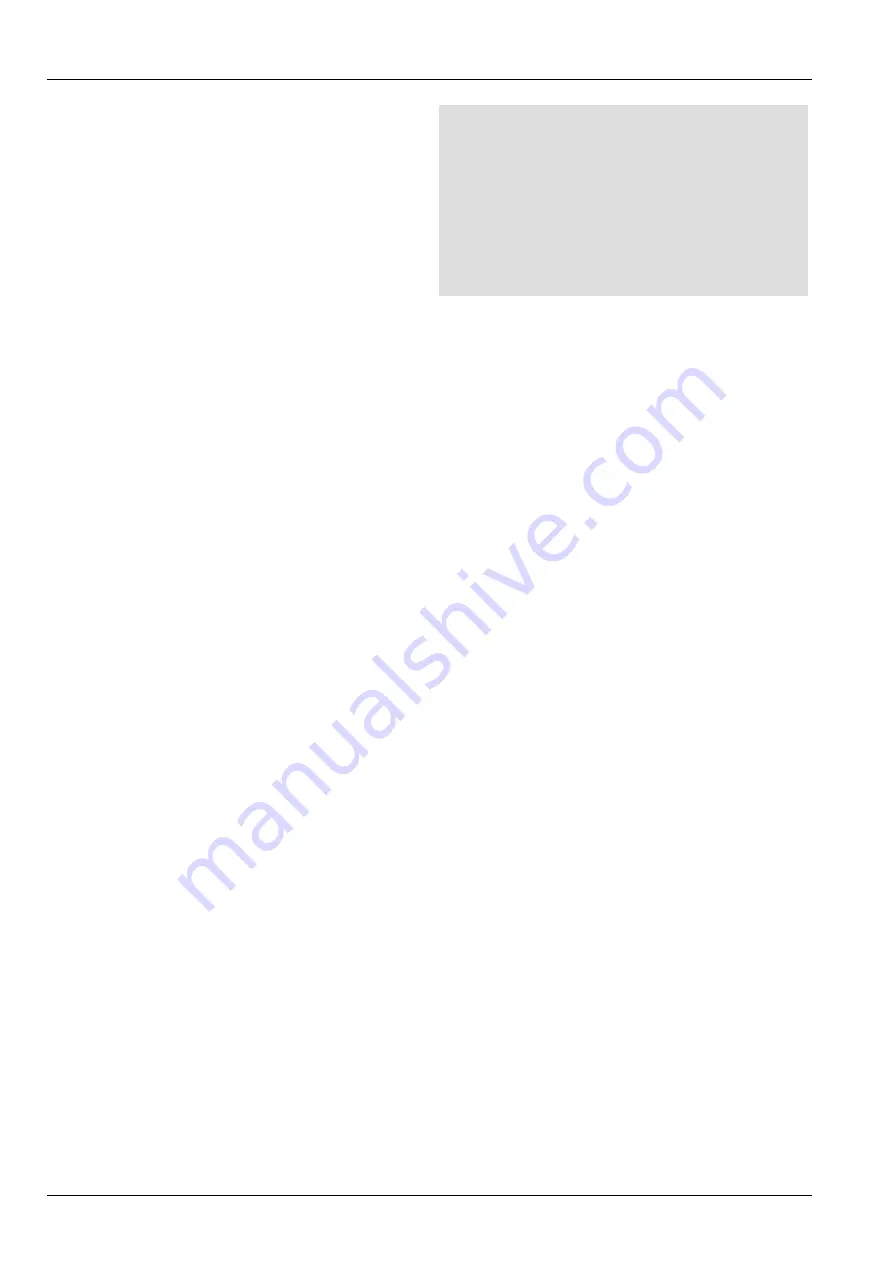
4 - OPERATING INSTRUCTIONS
• Wear and corrosion of internal components due to wa-
ter content, which affects lubricity.
• Deterioration of some rubber sealing compounds in the
fuel system.
• Biodiesel oxidation, which can lead to the formation of
deposits that can harm the fuel injection system.
NOTICE:
Any problem in the engine fuel injection equip-
ment associated with non-compliance to the following
conditions for biodiesel fuel handling and maintenance
will not be covered for Warranty by NEW HOLLAND.
Purchase biodiesel fuel from a trusted supplier who
understands the product and maintains acceptable
fuel quality.
It is highly recommended that you use
biodiesel from BQ 9000 accredited suppliers to maintain
the quality and consistency of the fuel. The BQ 9000
Quality Management Program is accredited by the Na-
tional Biodiesel Board for producers and marketers of
biodiesel fuel. See the National Biodiesel Board website
at www.biodiesel.org for more information.
The use of biodiesel blends above B5 through B20 will
not void the NEW HOLLAND warranty as long as the fol-
lowing conditions for biodiesel fuel handling and mainte-
nance are stringently followed:
Biodiesel fuel must be pre-blended by the supplier. Mixing
biodiesel fuels on-site can result in an incorrect mixture
that could damage the engine and/or fuel system.
For machines using Tier 4a engines with an exhaust
aftertreatment system:
1. If the biodiesel blend stock to
ASTM D6751-09
A
is used, special precautions need to be taken to
insure that it fully complies with the following special
requirements:
• Group I Metals content ( Potassium) is ≤
5 mg/kg
per
EN14538
as specified in the biodiesel
spec.
• Group II Metals content (C Magnesium) is ≤
5 mg/kg
per
EN14538
as specified in the biodiesel
spec.
• Phosphorus content lower than specified is a
mandatory requirement.
Phosphorus must not
exceed
4 mg/kg
per
ASTM D4951
.
2. The resulting greater than B5 through B20 blend must
not exceed
1 mg/kg
for Group I Metals (
Potassium) and for Group II Metals (C Mag-
nesium).
NOTICE: For machines using Tier 4a engines with
an exhaust aftertreatment system in regions where
the biodiesel blend stock is supplied to the ASTM
D6751-09
A
standard, it is essential that evidence of
compliance to the special limits for Group I Metals,
Group II Metals and the reduced phosphorus
content specified above be obtained on every
delivery of fuel from the fuel supplier. Failure to
comply with this requirement can result in damage
to the catalyst of the aftertreatment system which
will not be covered under warranty.
NOTICE:
NEW HOLLAND may void your warranty if the
problem is associated with poor fuel quality due to im-
proper blending. It is the responsibility of the fuel supplier
and/or yourself to ensure the right type of fuel and blend
is delivered and used.
Maintenance intervals
For machines using the all electronic engines with a high
pressure common rail fuel system, the engine oil and filter
change interval is reduced to
250 h
when using biodiesel
blends greater than B5 up to B20. Please refer to the
maintenance intervals specified in the Operator Manual
for all engines.
Check all hoses, connections and gaskets to ensure in-
tegrity and cleanliness every 3 months or 150 hours of
operation, whichever comes first.
Regular oil sampling is highly recommended to monitor
for oil and engine deterioration.
NOTE:
Oil sampling kits are available from your autho-
rized NEW HOLLAND dealer.
When switching back from biodiesel to regular #2 diesel,
all fuel filter, oil and oil filter should be changed even if this
falls between routine service intervals.
Storage
The machine should not be stored for more than three
months with biodiesel in the fuel system. For longer stor-
age time, it is strongly suggested that only regular #2
diesel fuel is used.
NOTE:
If storage for longer than 3 months is necessary,
the engine must be run on regular #2 diesel for a minimum
of
20 h
to flush the biodiesel fuel out of the fuel system
prior to storage.
Biodiesel is highly hygroscopic and tends to collect water
more than diesel fuel. This increases the risk of algae
and bacteria growth which can cause severe damage to
the fuel injection system. Keep the machine fuel tanks
and on-site storage tanks as full as possible to limit the
amount of air and water vapors inside the tank. Drain
water from the tanks at least once a week.
NOTICE:
Do not use biocide additives on Tier 4a engines
with an exhaust aftertreatment system.
4-4
Содержание Workmaster 25S
Страница 20: ...1 GENERAL INFORMATION 1 14 ...
Страница 102: ...3 CONTROLS AND INSTRUMENTS 3 40 ...
Страница 118: ...4 OPERATING INSTRUCTIONS 4 16 ...
Страница 186: ...7 MAINTENANCE 7 50 ...
Страница 199: ...9 SPECIFICATIONS NHIL17CT01125FA 1 NHIL17CT01124FA 2 9 9 ...
Страница 200: ...9 SPECIFICATIONS 9 10 ...