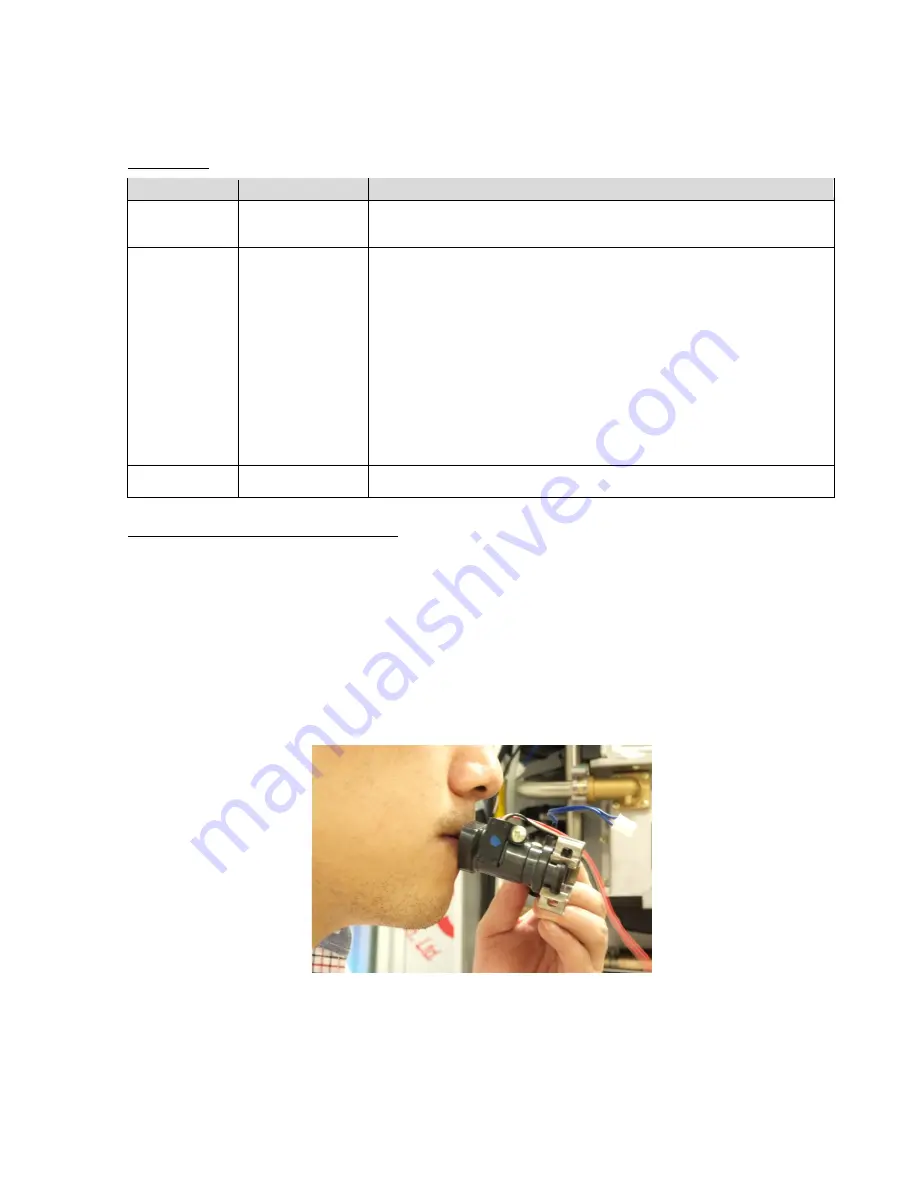
Check method
Fault
Possible Causes
Check method
No hot water flow
Cold water supply
error
1.
Check if the cold water line is frozen.
2.
Check if the cold water filter is clogged.
Boiler not
working
Defective flow sensor
1.
Check the current flow displayed on the front panel.
If the flow sensor is defective, the displayed flow value is 0.0 while water
flows from the hot water tap.
Remove the flow sensor and blow into it. The rotation detector on the flow
sensor is defective if the impeller rotates and display remains 0.0.
* Component Test mode may also be used to check the operation of the flow sensor
(refer to page 21).
2.
Check connector assembly and contact of the flow sensor.
3.
Check the input voltage of the flow sensor.
Operating voltage (Black + Red) : Defective PCB if DC 12 V is not supplied.
4.
Replace the flow sensor if no flow is detected while the operating voltage is
normal.
Other trouble
Defective PCB
If the issue continues despite the checking of items above the PCB is defective.
Emergency measures for a defective flow sensor
Replacement of the part is usually required for the boiler to operate when an error occurs with the flow sensor. If it is impossible to
replace the part immediately, use the following emergency measures.
If the flow sensor impeller is stuck due to foreign substances:
Remove the flow sensor and blow air through the part from the inlet side. If the impeller does not rotate, disassemble the impeller, and
remove the foreign substance before reassembling it.
If the flow displayed on the front panel is 0.0, and the impeller rotates when you blow into it, the flow sensor will need to be replaced.
1.
Drain water from the unit, then remove the flow sensor (refer to page 127).
2.
Blow air through the flow sensor. Check that the impeller rotates freely.
Содержание NCB-180
Страница 3: ......
Страница 4: ...Revisions Version Description of changes Date 1 00 First Issue October 27 2013 1 00 Reviewed BY...
Страница 16: ......
Страница 135: ...132 NCB Service Manual Version 1 0 7 2 Burner Assembly...
Страница 139: ...136 NCB Service Manual Version 1 0 7 4 Fan Gas Assembly...
Страница 142: ...Memo...
Страница 143: ...140 NCB Service Manual Version 1 0 Memo...
Страница 144: ...Memo...
Страница 145: ...142 NCB Service Manual Version 1 0 Memo...
Страница 146: ...Memo...
Страница 147: ...144 NCB Service Manual Version 1 0 Memo...
Страница 148: ...Memo...
Страница 149: ...146 NCB Service Manual Version 1 0 Memo...