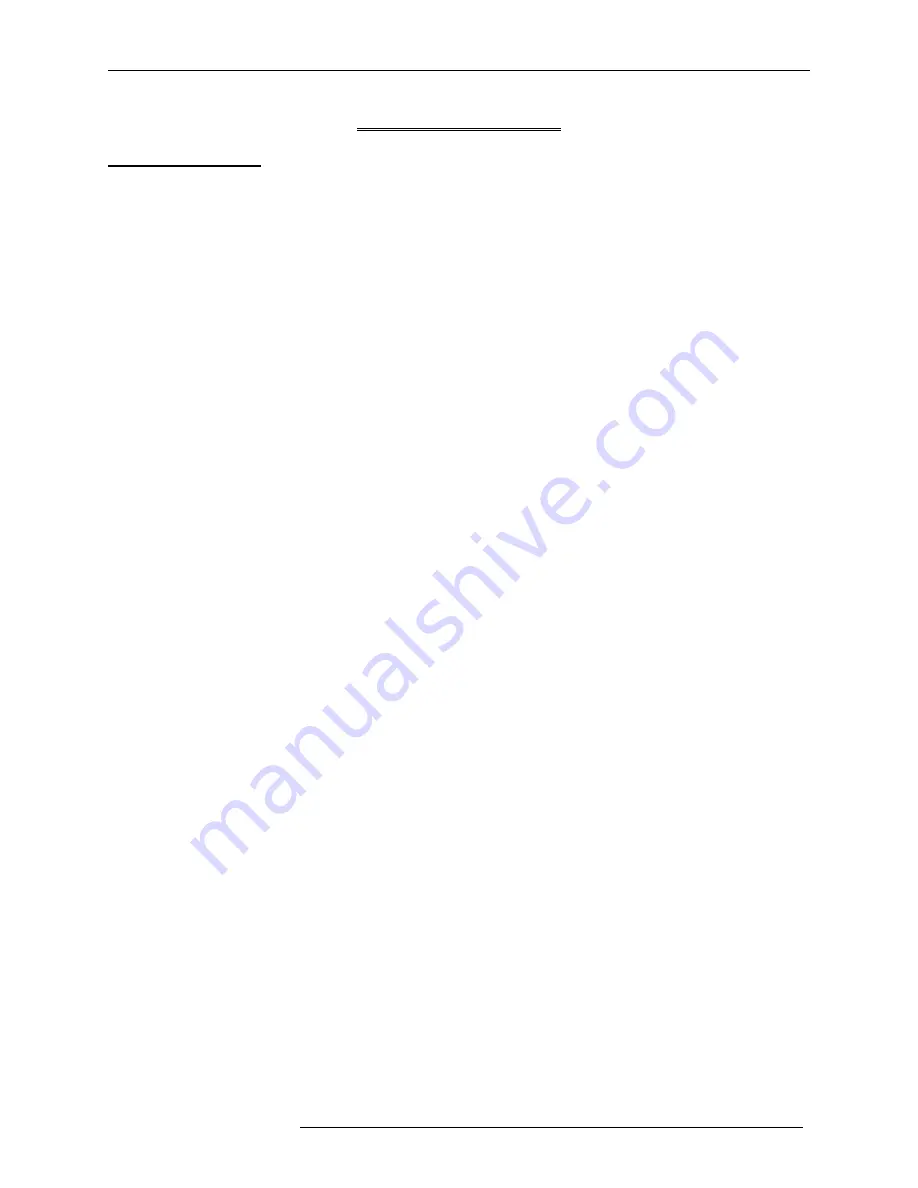
Mydax, Inc.
1M150W
Water Cooled Chiller
Designed for Lockheed Martin
4
SYSTEM
OVERVIEW
System Fluid Schematic
REFRIGERATION
Refer to drawing #D2914, the fluid (refrigerant & coolant) schematic. The heart of this design is the refrigerant valves,
shown at the left side of the drawing. These are pulse-width-modulated valves, controlled directly by the system's
embedded microprocessor. By controlling the duration of the openings of the evaporator valve, a precisely determined
flow of refrigerant is sent to the evaporator, allowing for exceptionally stable recirculating temperatures. This system is
designed to control the recirculating output temperature to ±0.5
°
C or better.
The microprocessor sets the positions of the evaporator valve based upon the system heat load. If the load increases, the
evaporator valve is opened for longer durations, passing more refrigerant. If the load decreases, the evaporator valve is
opened for shorter durations, passing less refrigerant. The microprocessor controls the bypass valve independently,
shunting unneeded refrigerant through the bypass heat exchanger, where it is evaporated before it can reach the
evaporator. The superheat valve passes only enough refrigerant to maintain the proper gas temperature at the suction
inlet of the compressor. Using this technique, Mydax is able to run in load conditions of zero to full load and all
combinations in between.
During normal operation, the durations of the valve openings remain nearly constant. Only major changes in heat load or
system-wide power cycling cause large changes in the valve drives. In the case of a step-wise change in heat load, the
microprocessor quickly drives the valves to the new settings and refrigerant flow soon settles at the proper level.
The controller sets the valve drives based primarily upon data received from RTD's (resistance temperature devices)
located about the circuit. The drawing shows RTD's at the discharge line leading from the recirculating pump, at the
return line leading to the reservoir, between the condenser and receiver and at the compressor inlet. The controller reads
these and other sensors constantly and sets the refrigerant valves accordingly.
Thus refrigerant flow is truly proportioned, allowing continuous compressor operation without the normal addition of
pressure-actuated hot gas bypass valves. All other refrigeration circuit components are used as in conventional systems.
All permanent copper joints in the refrigeration circuit are brazed for extra strength. Much of the circuitry is insulated to
eliminate cooling capacity loss and unpredictable operation due to drafts or fluctuating ambient air conditions.
RECIRCULATION
This system is designed to recirculate deionized water. It is not designed to recirculate solutions of automotive antifreeze.
Approximately 50 gallons are required to fill the 44 gallon polypropylene reservoir and associated plumbing. The
reservoir is fitted with two level sensors; one level sensor drives a FILL TANK alarm at the main panel, indicating
coolant level has dropped somewhat. The second sensor, the TANK EMPTY sensor, is connected to the safety interlock
loop and shuts the system down if tripped.
By using the data from the in-line turbine flow meter, the microprocessor will engage the Flow-OK relay at the selected
GPM. The output of the relay is wired to a connector located on the rear panel of the unit, labeled "Flow OK", which can
be used to drive an external alarm. Further description of this is provided in the
Installation
chapter.
The system is equipped with a deionizing filter; water flow through the filter is controlled by the microprocessor to
maintain the water resistivity to between 300K and 500K ohms. The control algorithm will turn on the DI flow solenoid
below 300K
Ω
and turn it off above 500K
Ω
. Bypass flow through this filter is restricted to 0.5 GPM.