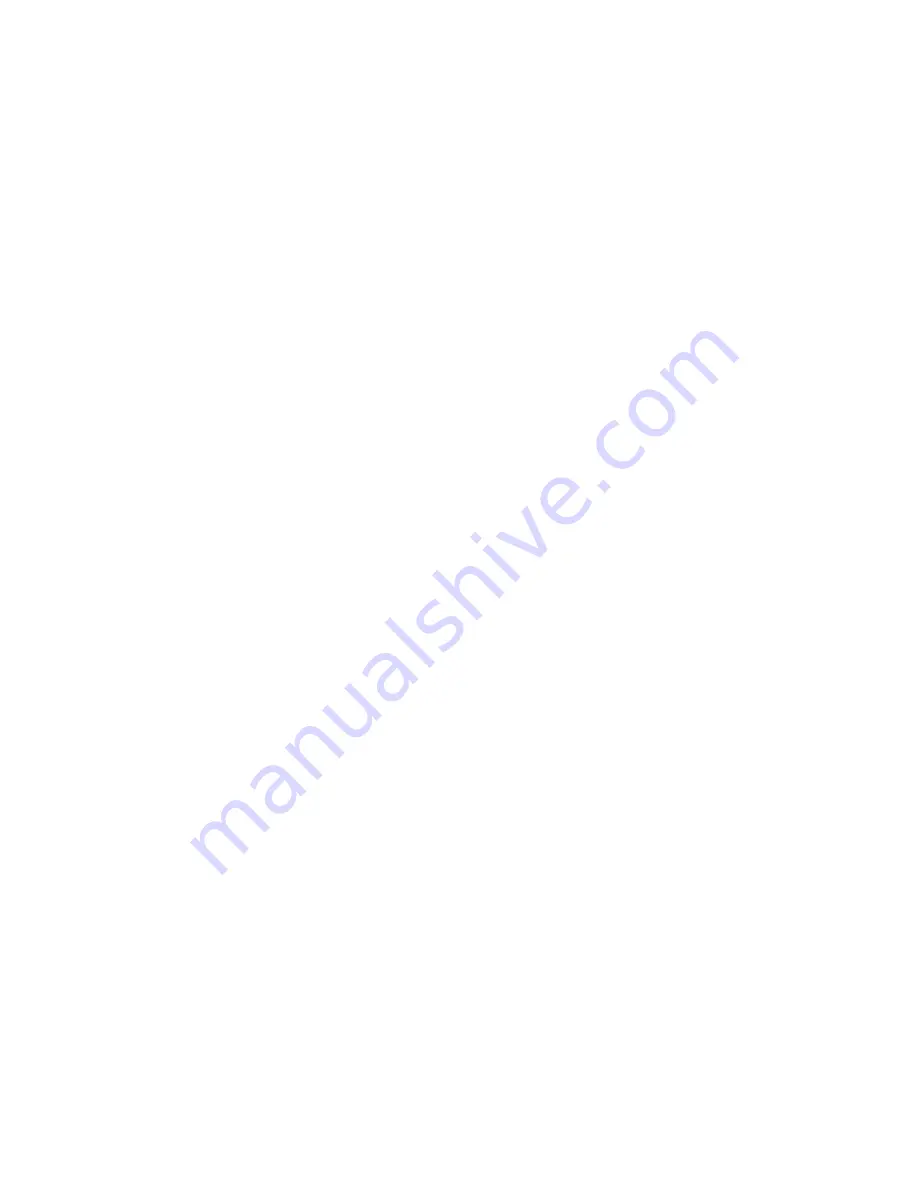
Seite 17
Congratulations on your new FunCub XL!
You will need the following tools to build the model:
•
2 x Zacki Elapor
# 85 2727
•
Hot-glue gun
•
Cross-point screwdrivers, large and small
•
Balsa knife
•
Pointed-nose pliers
•
Allen key, 1.5 mm A/F
•
6 mm A/F open-ended spanner
•
10 mm A/F open-ended spanner
•
13 mm A/F open-ended spanner
•
Additional items required if you intend to install the POWER-MUL-
TIlight:
•
2 M6 plug
# 8 5213
•
2 M6 sockets
# 8 5214
•
Soldering iron
•
Solder
Before starting construction:
Please check that the kit contents are complete by comparing
the parts supplied with the Parts List on page 31
Figs.
01 & 02
1. Preparing the fuselage shells, installing the servos (KIT)
Locate the pre-assembled M-Frame
30
and glue it in the right-hand
fuselage shell
5
using Zacki. Now glue the M-Frame fl oats support
31
, the two clip hinges “A”
71
, the Canopy Lock clip
73
and the
aero-tow coupling
75
in the appropriate positions.
Figs. 03 + 04
Glue the second Canopy Lock clip
73
in the left-hand fuselage
shell
4
in the same way.
Centre the elevator servo (HiTec HS-225BB
# 11 2225
) from your
transmitter
, then fi x the output lever on the servo output shaft.
The lever should point left when the inscription on the servo label
is the right way up (legible). Fit the retaining screw. Connect the
servo to the 600 mm extension lead
(# 8 5032)
, and apply a little
adhesive tape around the connectors to prevent the plug working
loose in fl ight. Fit the elevator servo in the opening in the right-
hand fuselage shell
5
, with the cable facing forward, and secure
it with hot-melt glue at both mounting lugs.
Fig. 05
Install the rudder servo (HiTec HS-225BB
# 11 2225
) as described
for the elevator servo - but with the output lever facing in the op-
posite direction. Connect it to a 600 mm extension lead
(# 8 5032)
and secure it with tape, then glue the servo in the opening in the
left-hand fuselage shell
4
.
Fig. 06
2. Joining the fuselage shells, attaching the external parts
(KIT)
Before joining the fuselage shells
4 + 5
permanently, fi t them to-
gether “dry” (without glue), and check that everything fi ts correctly.
When you are satisfi ed, apply Zacki to the joint surfaces of one
fuselage shell, and glue the two mouldings together.
Figs. 07 + 08
Now glue the dummy air outlets
24 + 25
, the upper cowl fairings
26 + 27
and the fuselage facing ribs “L”
76
and “R”
77
in the
positions shown.
Figs. 09 + 10
Invert (turn over) the fuselage and glue the “rear” exhaust fairing
29
to the underside of the fuselage. Glue the cargo door supports
“A”
32
and “B”
33
in place, followed by the tailwheel support
56
.
Figs. 11 + 12
3. Completing the cowl and canopy (KIT)
Take the moulded cowl
7
and glue the “front” exhaust fairing
28
to the underside using Zacki.
Figs. 13 + 14
The cowl is fi xed to the fuselage using magnets. Glue three of
the magnets
34
in the moulded-in recesses in the cowl
7
, and
the remaining three to the recesses in the front of the fuselage.
!CAUTION!:
it is important to fi t the magnets the right way round,
i.e. the pairs of magnets which come into contact with each other
must attract - not repel! Do not place the cowl on the fuselage until
the glue has set hard!
Figs. 15 - 17
Now glue the two Canopy Lock lugs
74
in the moulded slots in
the canopy
6
using Zacki.
Fig. 18
4. Installing the motor (KIT)
Screw the metal cruciform motor mount to the motor using the four
cross-head screws supplied. Apply a drop of thread-lock fl uid to
each screw, and tighten them fi rmly.
Fig. 19
Remove the cowl from the fuselage before installing the motor.
This is the procedure: place the plastic cruciform motor mount
131
between the metal cruciform mount (attached to the motor) and the
motor bulkhead (part of the M-Frame). Fix the motor assembly in
place using the four M3 x 12 mm retaining screws
132
and 3 mm
I.D. washers
133
. The cowl can now be replaced on the fuselage.
Figs. 20 + 21
5. Installing the main undercarriage (KIT+RR)
First fi x the angle strut brackets
36
to the underside of the main
undercarriage unit
35
using two M3 x 6 mm cross-head screws
37
on each side. The fi rst main wheel
39
can now be attached to the
main undercarriage unit using the axle
40
(M6 x 45 mm machine
screw) and one M6 self-locking nut
41
on each side. Ensure that
the wheel is still free to rotate smoothly when you have tightened
the nuts. Repeat the procedure on the other side of the main
undercarriage.
Fig. 22
When the undercarriage is complete, fi x the assembly to the
M-Frame using four M3 x 20 mm retaining screws
42
. Note that
the strut retaining brackets must be at the rear (towards the tail)!
Fig. 23
6. Installing the tailwheel unit (KIT+RR)
The fi rst step in assembling the tailwheel unit
47
is to slip the lower
bush
48
through the hole from the underside. Fit the upper bush
46
on top, and glue these parts together with a little Zacki. The
tailwheel spigot
49
can now be slipped through the bush from the
underside. The spigot is secured with the steering lever
44
: fi t
an
M3 x 6 mm cross-head screw
45
in the shaft driver
43
which fi ts
in the steering lever
44
. Ensure that the screw engages on the
machined area of the spigot.
The bottom end of the spigot is bored and threaded M3. Fit the
tailwheel yoke
50
on the spigot, engaging the square section in
the hole, and fi t an M3 x 10 mm cross-head screw
55
and a 3 mm
I.D. washer
54
to secure it. Tighten the screw fi rmly.
Now fi t the tailwheel
51
and tailwheel shaft
52
(M2 x 22 mm)
between the wheel and the tailwheel bracket, together with two
M2.5 nuts
38
(as spacers), and secure the wheel with the M2
self-locking nut
53
.
Fig. 24
Содержание FUNCUB XL
Страница 33: ...Seite 33 pic 15 pic 16 pic 13 pic 17 pic 11 pic 14 pic 12 32 33 56 29 7 28 34 34 34 34 34 34 pic 18 74 74 6...
Страница 40: ...Seite 40 pic 71 pic 72 pic 74 pic 69 pic 73 pic 67 pic 70 pic 68 22 34 34 34 34 34 129 20 122 121...
Страница 42: ...Seite 42 pic 85 pic 86 105 85mm Battery RX ESC red LED white LED red LED pic 83 pic 84 80 80...