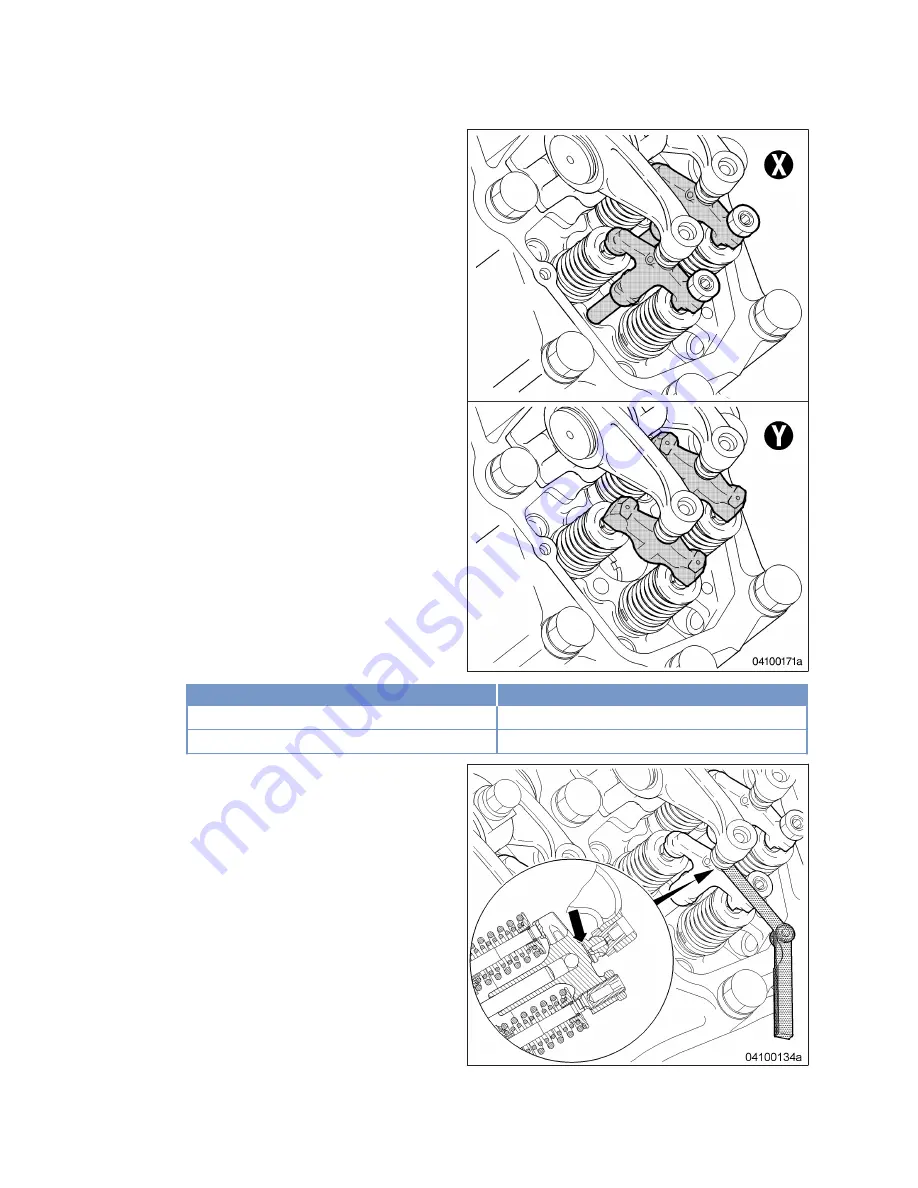
Checking valve bridge balance
Fig.
Component
X
Guided valve bridge
Y
Flying valve bridge
Note:
Not applicable for engines with flying valve
bridge.
1.
Prior to adjusting valve clearance, check
valve bridge balance on all valve bridges.
2.
Use feeler gage to determine clearance be-
tween valve bridge and rocker arm.
80 | Valve Drive | M015565/03E 2016-02
TIM-ID: 0000004352 - 006