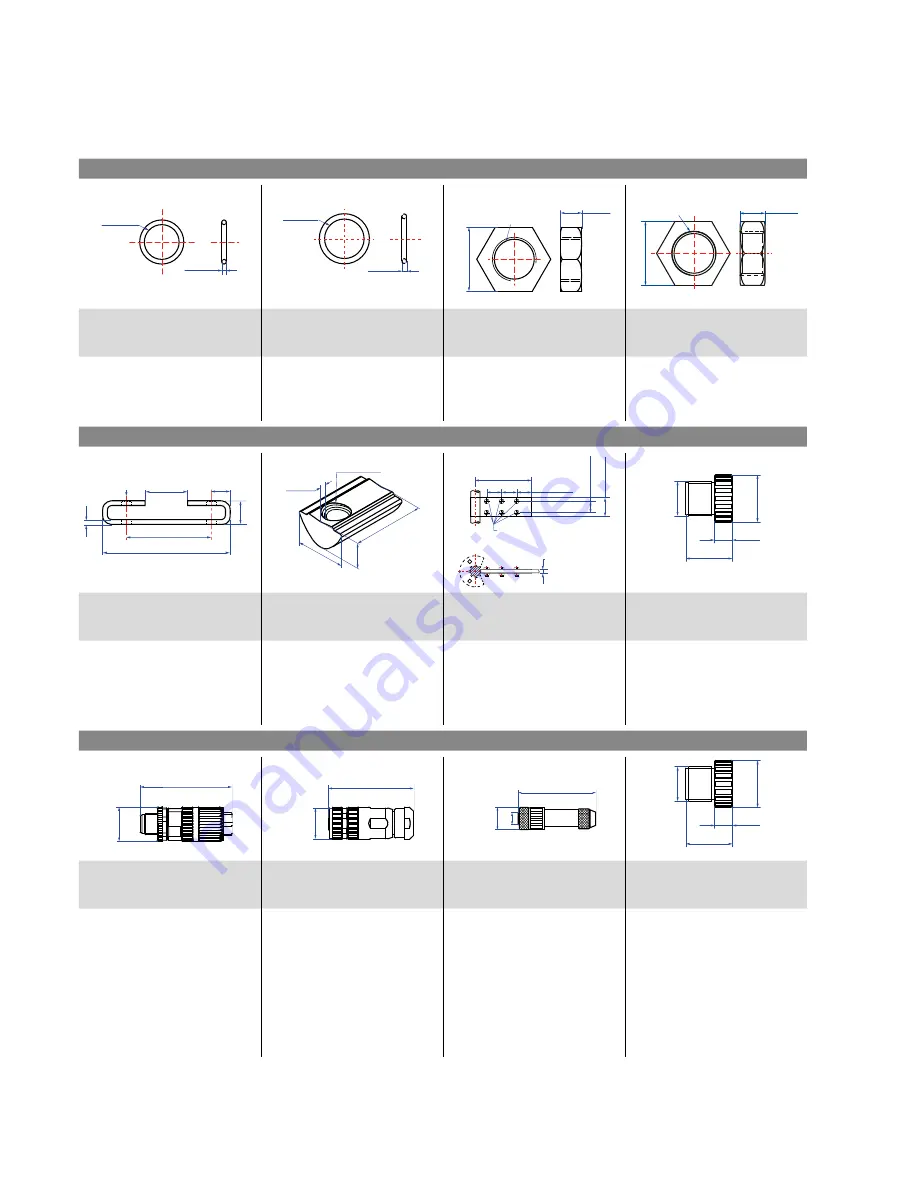
Temposonics
®
R-Series
V
EtherNet/IP™
Operation Manual
I 20 I
4/
Follow the manufacturer‘s mounting instructions
Controlling design dimensions are in millimeters and measurements in ( ) are in inches
O-rings
Mounting hardware
Ø 16.4
(Ø 0.65)
Ø 2.2
(Ø 0.09)
Ø 19.3
(Ø 0.76)
Ø 2.2
(Ø 0.09)
M18×1.5-6g
A/F 27
8.7
(0.34)
¾"-16 UNF-3A
A/F 28
11
(0.43)
O-ring for threaded fl ange
¾"-16 UNF-3A
Part no. 560 315
O-ring for threaded fl ange
M22×1.5-6g
Part no. 561 337
Hex jam nut M18×1.5-6g
Part no. 500 018
Hex jam nut ¾"-16 UNF-3A
Part no. 500 015
Material: Fluoroelastomer
Durometer: 75 ± 5 Shore A
Operating temperature:
−40…+204 °C (−40…+400 °F)
Material: FPM
Durometer: 75 Shore A
Operating temperature:
−20…+200 °C (−6…+392 °F)
Material: Steel, zinc, plated
Material: Zinc plated with nylon insert
Mounting hardware
Accessory for M12 cable connector
4 Holes
Ø 5.3 (Ø 0.21) 28 (1.1)
9 (0.35)
50 (1.97)
2 (0.08)
68 (2.68)
9 (0.35)
Mounting clamp width
:
14.6 (0.57)
4
(0.16)
11.5
(0.45)
4.5
(1.8)
8
(0.31)
M5 thread
20 (0.79)
60 (2.36)
16 (0.63)
12 (0.47)
3.2 (0.13)
Ø 3.2 (Ø 0.13)
M3 fastening screws (6×)
M12
Ø 16 (Ø 0.63)
16
(0.63)
6
(0.24)
Mounting clamp
Part no. 400 802
T-nut
Part no. 401 602
Fixing clip for rod with Ø 10 mm
Part no. 561 481
M12 connector end cap
Part no. 370 537
Material: Stainless steel (AISI 304)
Fastening torque for M5 screw: 4.5 Nm Application: Used to secure sensor
rods (Ø 10 mm (Ø 0.39 in.)) when
using an U-magnet or block magnet
Material: Brass, non-magnetic
Female connectors M12 should be
covered by this protective cap
Material: Brass nickel-plated
Ingress protection: IP67 (correctly fi tted)
Fastening torque: 0.39…0.49 Nm
Cable connectors
4
Cables
52
(2.05)
Ø 19.5 (Ø 0.77)
53
(2.09)
Ø 20
(Ø 0.79
)
43
(1.7)
Ø
12
(Ø
0.47)
M8
M12
Ø 16 (Ø 0.63)
16
(0.63)
6
(0.24)
M12 D-coded male connector
(4 pin), straight
Part no. 370 523
M12 A-coded female connector
(5 pin), straight
Part no. 370 677
M8 female connector (4 pin), straight
Part no. 370 504
M12 connector end cap
Part no. 370 537
Material: Zinc nickel-plated
Termination: Insulation-displacement
Cable Ø: 5.5…7.2 mm (0.2…0.28 in.)
Wire: 24 AWG – 22 AWG
Operating temperature:
−25…+85 °C (−13…+185 °F)
Ingress protection: IP65 / IP67
(correctly fi tted)
Fastening torque: 0.6 Nm
Material: GD-Zn, Ni
Termination: Screw
Contact insert: CuZn
Cable Ø: 4…8 mm (0.16…0.31 in.)
Wire: 1.5 mm²
Operating temperature:
−30…+85 °C (−22…+185 °F)
Ingress protection: IP67 (correctly fi tted)
Fastening torque: 0.6 Nm
Material: CuZn nickel plated
Termination: Solder
Cable Ø: 3.5…5 mm (0.14…0.28 in.)
Wire: 0.25 mm
2
Operating temperature:
−40…+85 °C (−40…+185 °F)
Ingress protection: IP67 (correctly fi tted)
Fastening torque: 0.5 Nm
Female connectors M12 should be
covered by this protective cap
Material: Brass nickel-plated
Ingress protection: IP67 (correctly fi tted)
Fastening torque: 0.39…0.49 Nm