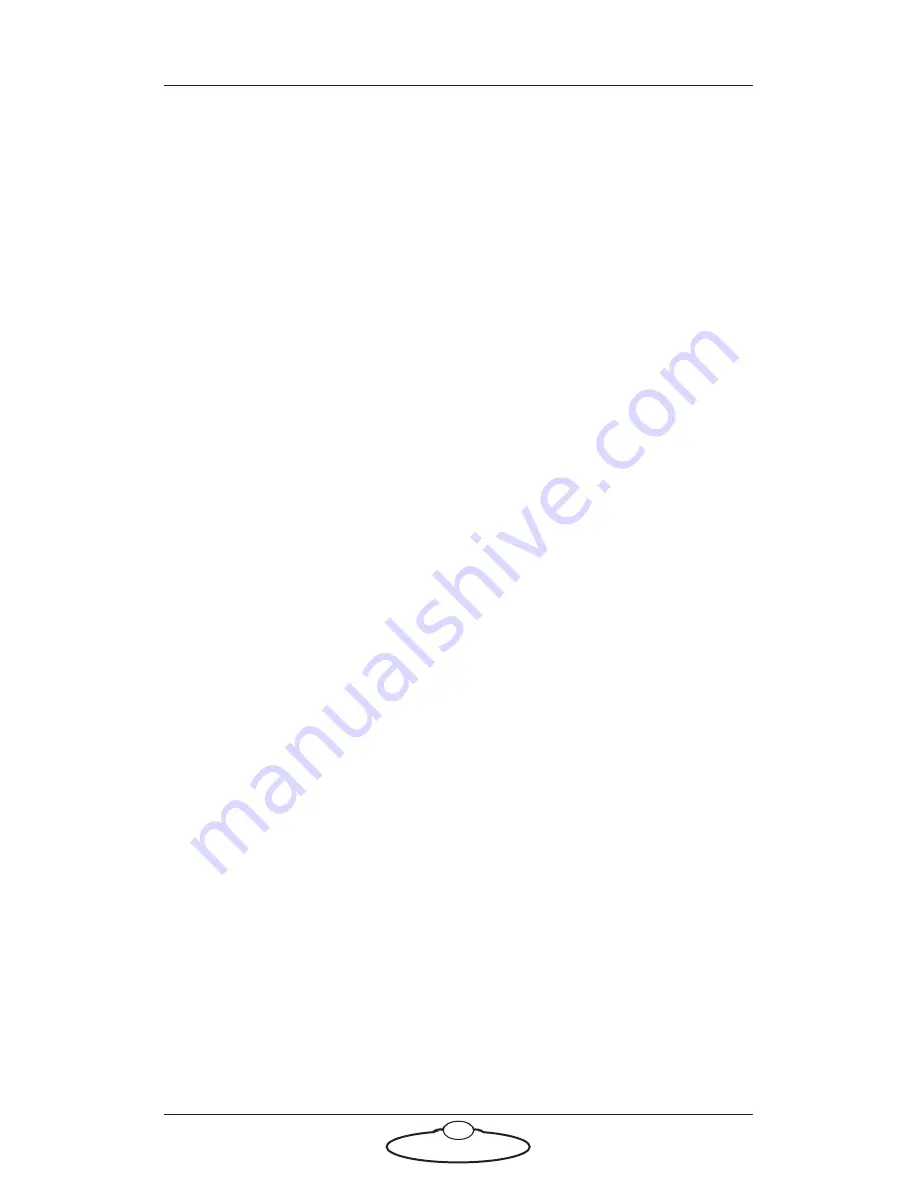
SFH-50 Quick Start Guide
25
1-8.
#1 - #8
connectors for the
PAN
(#1),
TILT
(#2), and
ROLL
(#3)
stepper motors in the head. The extra numbered connectors are for
auxiliary stepper motors. For pin-out information see
Stepper motor
connector
on page 26.
9.
POWER 18-36V
connector, for power input for the head. For
pin-out information see
Power 18-36 Volts connector
on page 26.
10.
DATA
(on a Quad-box) or
SERIAL
(on an Octo-box) connector.
This is a Serial RS232 connector, for updating the firmware in the
Quad-box or Octo-box. For pin-out information see
Serial RS232
connector
on page 26.
11.
TRIGGER
connector, for a bi-directional trigger signal between the
head and camera. For pin-out information see
Trigger connector
on
page 27.
12.
DATA IN
DataLink In (Up Link) connector for controlling the head
using a DataLink connection, as an alternative to an Ethernet
connection. You connect this to a device that is further up the
DataLink daisy-chain, such as one of the following:
The
DATA OUT
(or
DOWN LINK
) connector on a controller
such as the MSA-20 Handwheels or Large Format Panel (LFP).
The
RIG/HEAD
connector on an RT-12 interface box which is
in turn connected to a PC running Flair Motion Control
Software.
For pin-out information see
Data In connector
on page 27.
13.
DATA OUT
DataLink Out (Down Link) connector for connecting
additional devices on the DataLink network. This is not normally
used, as the Octo-box on the head is usually at the end of the
DataLink daisy-chain. For pin-out information see
Data Out
connector
on page 27.
14.
ETHERNET
RJ45 connector for controlling the head using an
Ethernet network connection, as an alternative to a DataLink
connection.
Содержание SFH-50
Страница 1: ...Quick Start Guide Document version SFH50 QSG 20150811 Part number MRMC 1166 00 SFH 50 HEAD ...
Страница 4: ...SFH 50 Quick Start Guide iv Appendix 3 Specifications 33 ...
Страница 10: ...SFH 50 Quick Start Guide 6 SFH 50 with Roll Ring Mounting rods LCM Zoom LCM Focus ...
Страница 38: ...SFH 50 Quick Start Guide 34 SFH 50 with Roll Ring 130 53 25 25 40 192 25 25 27 25 max 305 480 455 ...
Страница 39: ...SFH 50 Quick Start Guide 35 188 215 116 Roll Ring inner diameter Platform width Roll Ring platform length ...