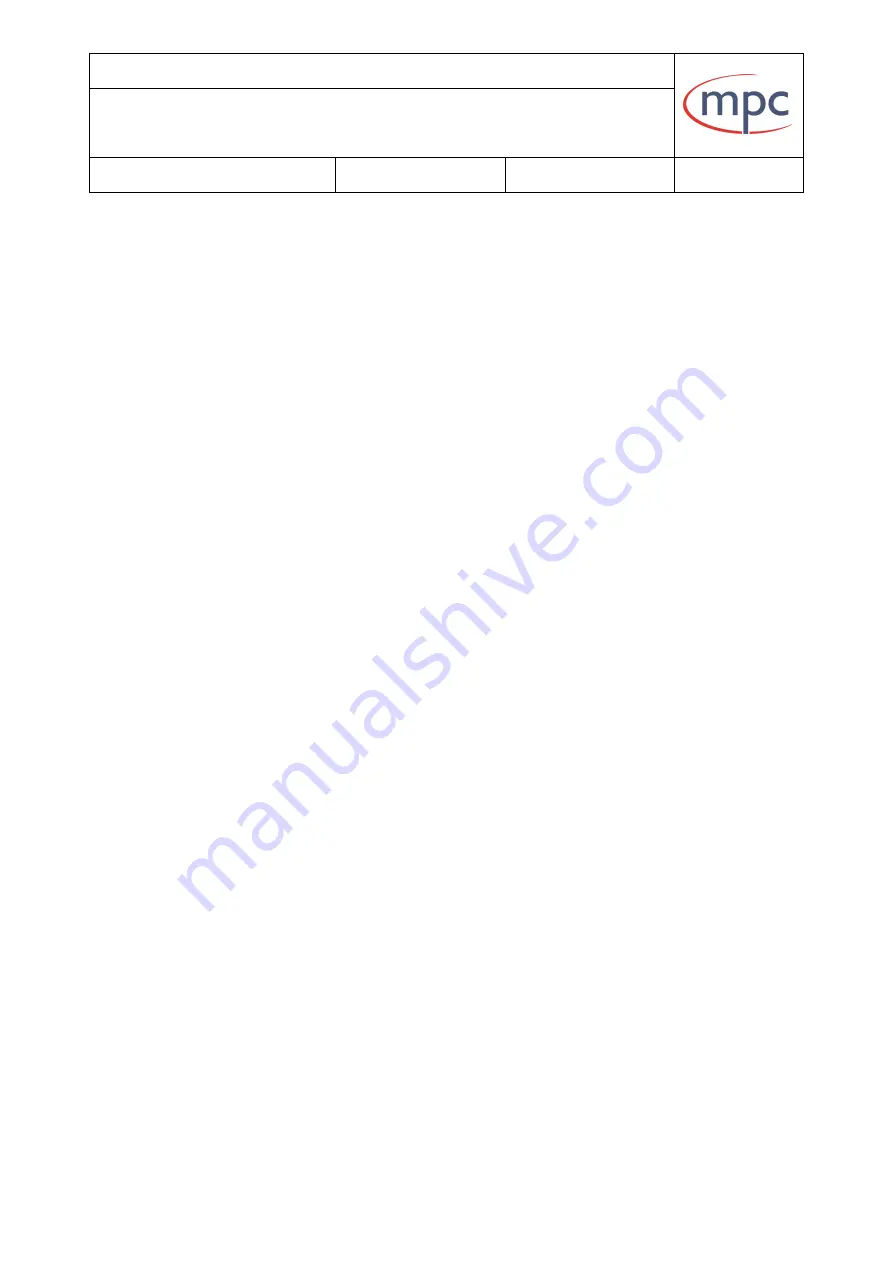
MESSTEC Power Converter GmbH
Operating Manual
TEC Controller
Document: 10100920OM
Revision: 1.1
Date: 10.10.2019
Page 9/71
This is the reason, MPC TEC-Controllers are designed for uncompromising low output current
ripple, even though this is associated with higher complexity. The result is clear: Full performance
of the Peltier element due to unconstrained maximum temperature difference operation. The
resulting cooling system setup has therefore high efficiency and is cost effective.
PWM based TEC-Controllers are small and on its own, may have slightly higher efficiency.
However the performance of the Peltier element operated in this way is really bad. In the best
case, the Peltier element can create a maximum temperature difference of 50% compared to DC
operation. Usually it is even less. Therefore it is required to provide larger Peltier elements, a
larger power supply and larger heatsink and blower equipment. The resulting cooling system
setup has therefore low efficiency and on the whole is not really cost effective.
Signal processing for the temperature sensor is optimized for RTD (Resistance Tempera-
ture Detector) sensors. RTDs are passive devices as, Platinum, Nickel, NTC or Silicone
sensors. In any case, active or integrated circuit sensors are not appropriate. Two and
four wire connection is possible. Use four wire cabling with shield for high precision
demands. The type of sensor can be selected conveniently by PC-Software. It is also
possible to define an application specific RTD sensor.
The design of the sensor signal processing circuit ensures very high precision and virtu-
ally no drift errors. There is no need for calibration. Signal processing for the temperature
sensor has open-sensor and short-circuit detection. In either case, the TEC-Controller
goes into error mode and will be disabled.
For TEC-Controller operation, there are 3 sorts of control signals and corresponding sig-
nal processing available:
analog input, with associated reference voltage output (5 V)
digital input
digital output
The TEC-Controller has no analog outputs.
There are two analog inputs available, one to give the HW-setpoint, second input is for
future use. Dependent on the actual configuration (PC-software), the temperature set-
point can be determined by an analog control voltage (0 V to 5 V) feed to the HW-set-
point input. With default settings, the analog control voltage results in a temperature set-
point of 0 °C to 50 °C, i.e. 1,5 V input voltage creates a temperature setpoint of 15 °C.
The analog control voltage can be externally generated and made available in various
ways. For easy operation with minimal wiring effort, there is also an internal potentio-
meter available. The analog input for the HW-setpoint can be configured extensively
(see: Configuration in Detail).
Depending on the actual configuration, the temperature setpoint can also be adjusted
directly in the GUI of the PC-software. Then no wiring of the analog HW-setpoint input is
necessary at all.
Note:
Highest control accuracy will be achieved in the SW SETPOINT MODE.
There are two digital inputs available: HW-ENABLE and HW-RESET. Both digital inputs
can be independently configured (PC-software) as low- or high-active. Default setting is
low-active. With the input HW-ENABLE activated, the TEC-Controller's power stage and