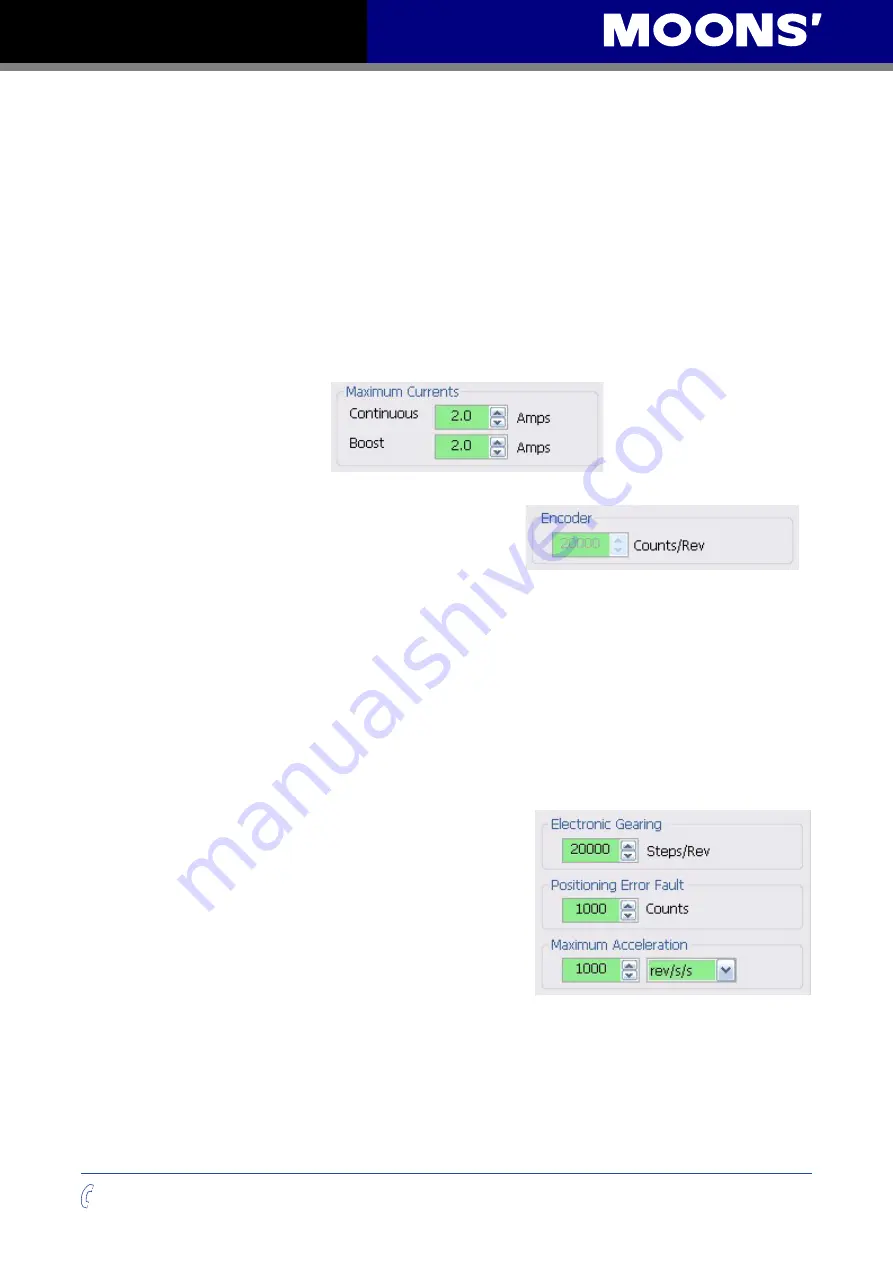
23
Rev. 1.0
0006302011
SSM23C User Manual
+86-400-820-9661
4.2 Basic Configuration
The default control modes for the SSM23C integrated step servo is SCL mode.
There are total 5 sets of parameters, 4 of them need to be configured.
4.2.1 Maximum Currents
Continuous - The current that can be sustained indefinitely.
Boost - An SSM drive can provide a momentary current boost. This allows for greater acceleration
rates than would otherwise be possible. To assure reliable motor operation, the drive automatically
ramps the current down after one second so that the average current does not exceed the motor’s
rating.
4.2.2 Encoder
Encoder resolution is fixed at 20000 counts/rev.
4.2.3 Electronic Gearing
Genarally, we recommend using the default setting 20000 steps/rev. With Electronic Gearing drive
response to incoming step pulses can be adjusted. This is very useful when a step motor drive
is being replaced with a step-servo system, as the SSM can have the same number of steps/
revolution as the stepper. For example, SSM23C can be programmed to operate at 200 steps/rev,
like a full step drive. If the system is working in degrees, the drive can be programmed to operate
at 36,000 steps/rev resulting in an even number of steps (100) per degree.
4.2.4 Positioning Error Fault
Positioning error is the difference, in encoder counts,
between the actual position and the commanded position
of the motor. A small amount of positioning error is a
normal part of a step-servo system. In the event of a
broken wire, a failed sensor, the motor encounting a
physical obstruction, or operator error, a position error
fault limit can prevent damage to the system. Anytime the
position error (as reported by the encoder) exceeds this set
limit, the drive is disabled and a fault alarm occurs.
The fault limit can be set as low as 10 encoder counts,
or as high as 32000. During initial tuning of the system, this value should be set high so that the
drive doesn’t shut down while the tuning parameters are being adjusted. Once the drive is properly
tuned and the expected amount of error during normal operation is known, an appropriate fault
limit can be set. For example, with QuickTuner’s oscilloscope function set to plot position error,
sample moves using the maximum speed and acceleration planned for use in an application
should be executed. If the maximum position error is 50 counts, the fault limit could safely be set
at 100.