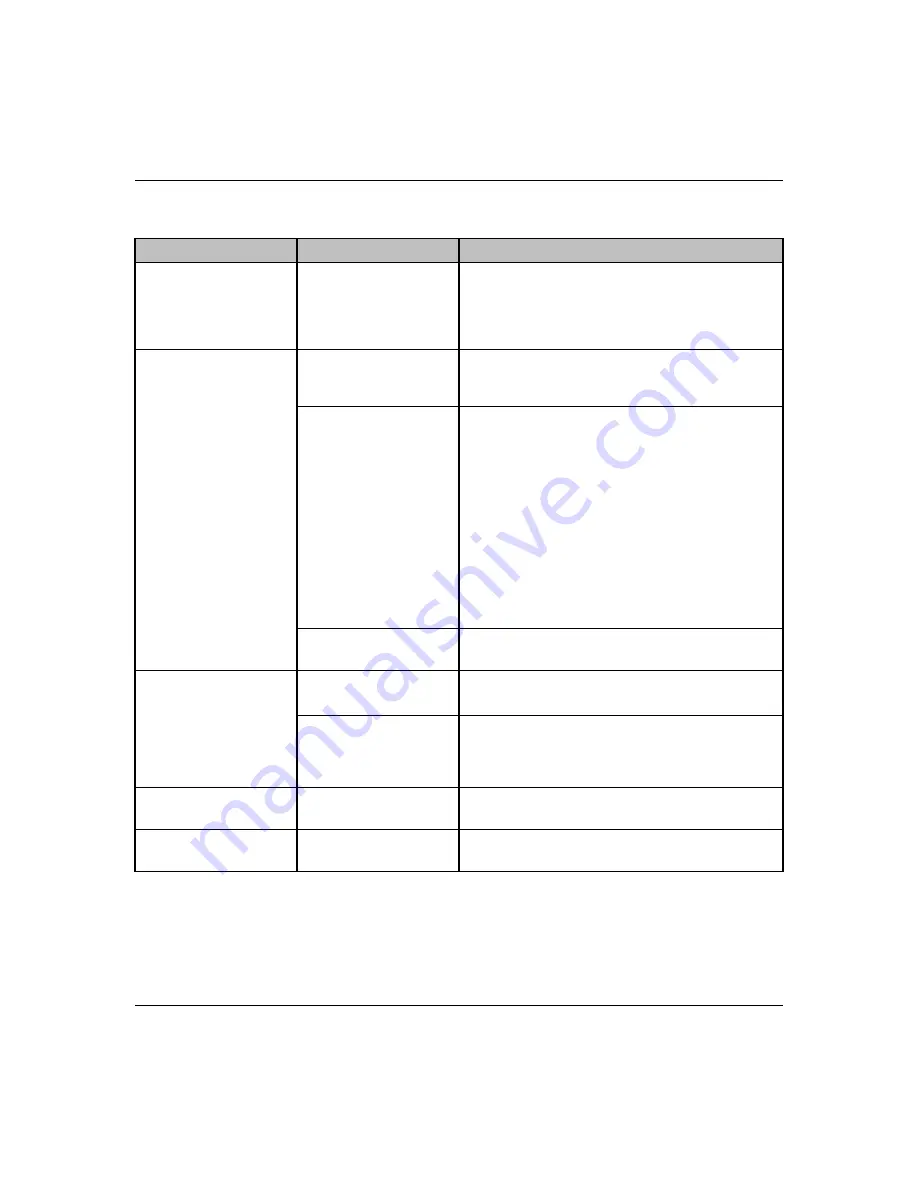
Troubleshooting
Series 203 Variable Leak Valve Installation and Operating Instructions
7
Symptoms, Causes, and Remedies
Symptom
Cause
Remedy
Leak has only on or off
properties. Does not give
smooth continuous control.
A liquid film on the sealing
surfaces produced by
allowing moist or vapor
laden gases to flow through
the Leak.
A brief vacuum bakeout at 200 to 300 ° C for a few hours.
Leak will not seal.
Insufficient thrust, clutch
slips before seal is attained.
Remove the driver handle and tighten the clutch set screw.
After the Leak is sealed, adjust the clutch to slip about 10
counter numbers below the sealed position.
Insufficient thrust, driver
dirty.
Remove the driver. Remove the clutch. Remove the
retaining rings holding the drive shaft bearings in place.
Remove the bearings and the worm shaft. The drive screw
worm gear assembly should now be carefully unscrewed.
Clean the drive screw threads with a solvent such as
chlorothene. Do not allow the drive screw worm gear
assembly to come in contact with heat. Clean the worm. Do
not clean the bearings. Relubricate the
contact surfaces of the worm and gear and drive screw with
molybdenum disulfide. Reassemble. Remove the retracting
screw. Loosen the set screw in the aluminum bushing and
rotate one-eighth turn. Tighten set screw and replace the
retracting screw. Test the valve for control. Repeat as
necessary until smooth action is obtained.
Sealing surfaces
contaminated.
Replace Leak Valve body. Glass particles, lint, metal chips
and dust cannot usually be removed.
Leak momentarily opens or
closes in reverse reaction to
the turning of the driver
handle.
Misalignment of Driver
Assembly and Leak Valve.
Re-attach the Driver and Leak Valve, tighten the mounting
screws evenly.
Driver Assembly parts out of
alignment.
Remove the retracting screw. Loosen the set screw in the
aluminum bushing and rotate one-eighth turn. Tighten set
screw and replace the retracting screw. Test the valve for
control. Repeat as necessary until smooth action is obtained.
Body mounting screws stick
after bakeout.
Lubrication has evaporated.
Place drops of penetrating oil on each screw and let soak for
10 minutes.
Retracting screw strips out
of nosepiece.
Retracting screw not
properly seated.
Always make certain retracting screw is completely engaged
before operating valve.
Содержание Granville-Phillips 203 Series
Страница 2: ......
Страница 4: ......
Страница 6: ...ii Series 203 Variable Leak Valve Installation and Operating Instructions...
Страница 15: ......