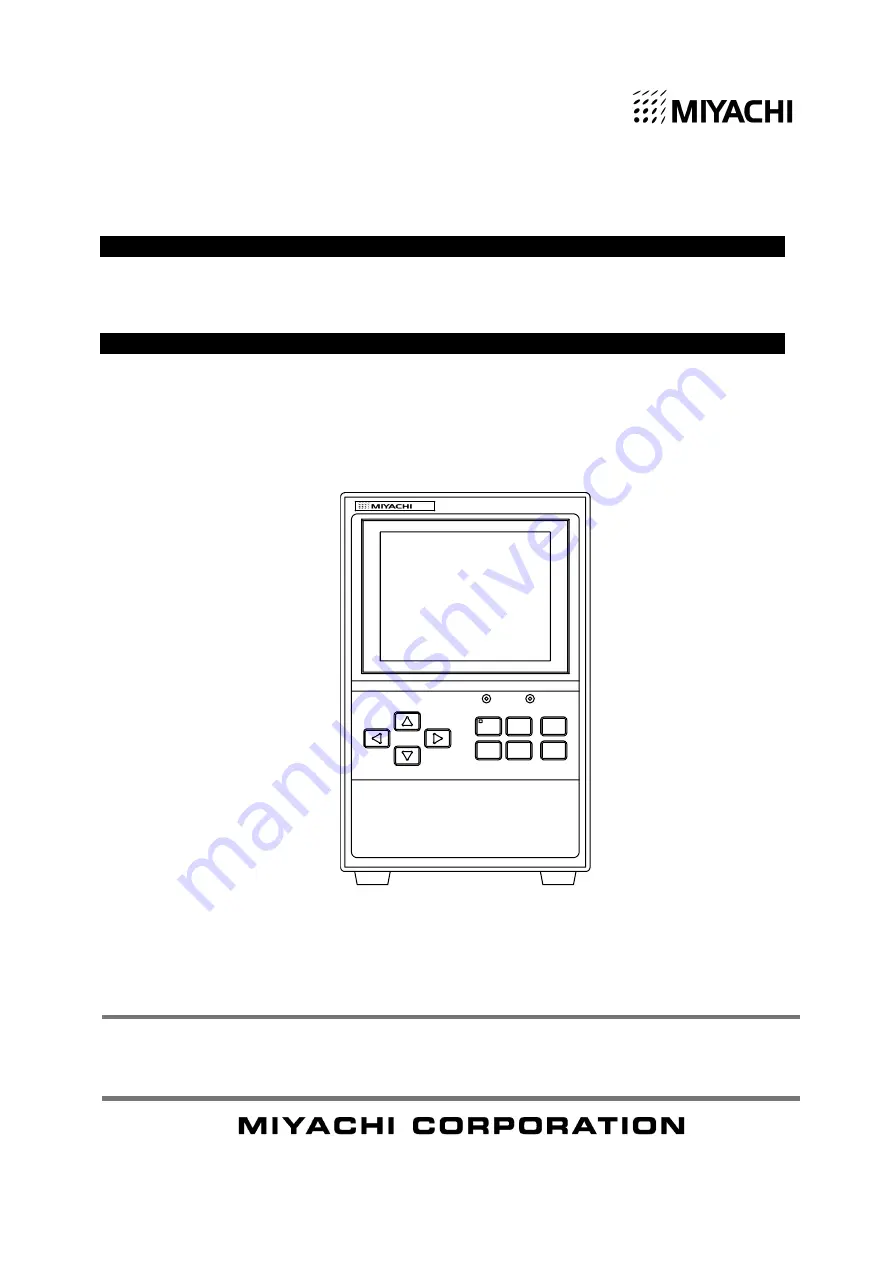
INVERTER-TYPE WELDING POWER SUPPLY
IPB-5000A
OPERATION MANUAL
Thank you for purchasing the
Miyachi Inverter-type Welding Power Supply
IPB-5000A
.
・
For correct use, read this operation manual carefully.
・
After reading, save it in a proper place where you can easily access to.
J03M0756E-05
P O W E R
S TA R T
IP B - 50 0 0 A
CURSOR
WELD
MENU
RESET
ENTER
+
-
WELDING POWER SUPPLY
Содержание IPB-5000A
Страница 119: ......