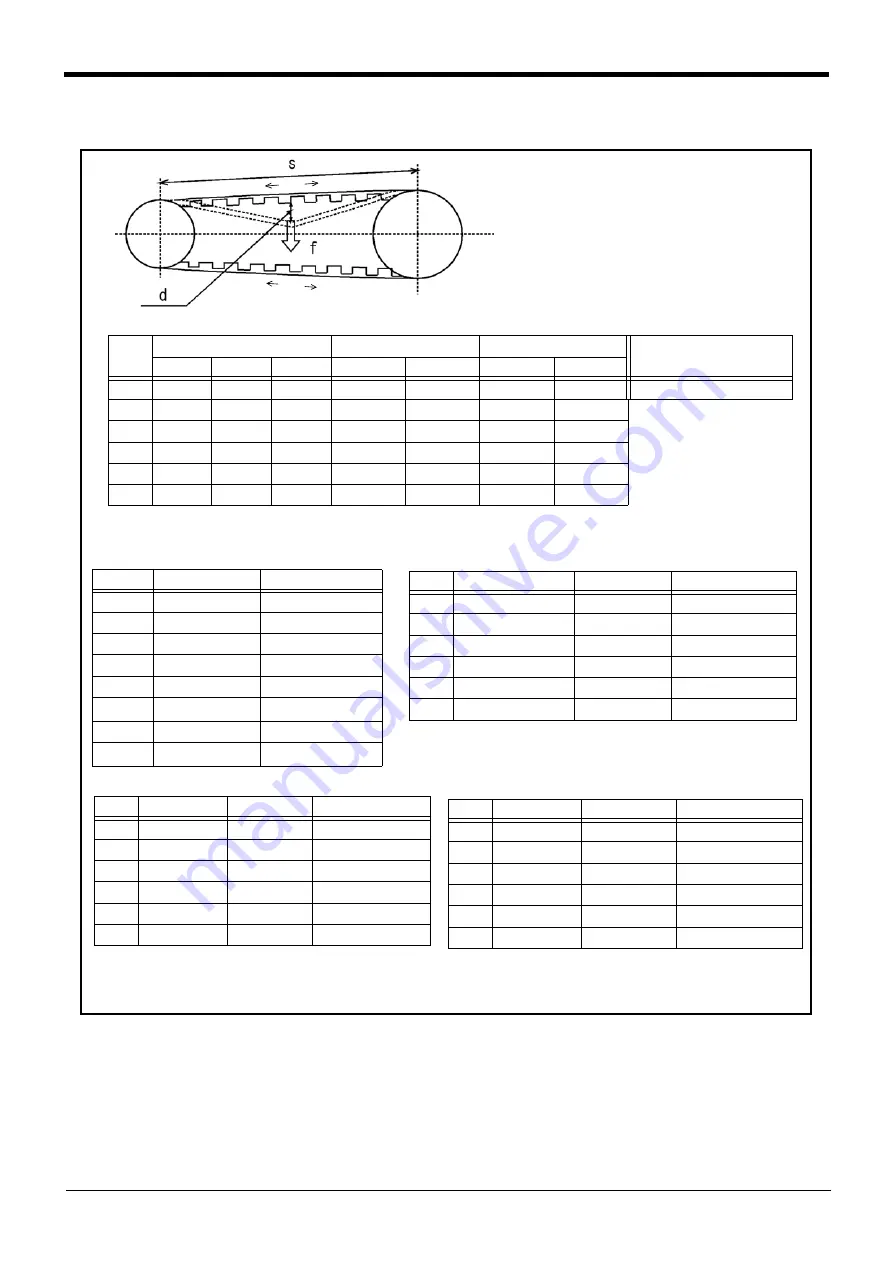
Maintenance and inspection procedures
(8) Timing belt tension
Fig.5-13 : Belt tension
The timing belt can satisfactorily convey the drive and keep a durable force only when it has an adequate tension.
The belt tension should not be too tight or too loose. Instead, it should be adjusted to a degree that elasticity is
felt when the belt is pressed with the thumb. If the belt tension is too weak, the belt loosening side will vibrate. On
the other hand, if the belt tension is too strong, a sharp sound will be heard and the belt tension side will vibrate.
The detailed adjustment (tension) is shown in
.
Check and adjust with the belt pressing force f and the slack amount d between span s.
T
T
T
T
f : Pressing force
s : Span
d : Slack
T : Tension
■ Belt specification
Axis
Belt type
Span : s (mm)
J1
210-3GT-6
61
J2
324-3GT-6
88
J3
303-3GT-6
103
J4
186-3GT-4
52
J5
336-3GT-4
131
J5(brake)
174-3GT-4
42
J6
345-3GT-4
131
J5(brake)
174-3GT-4
42
■ Inspection
Axis
Tension
: T (N)
Slack : d (mm)
Pressing force : f (N)
J1
14.7 ~ 43
1.0
1.0 ~ 2.9
J2
14.7 ~ 43
1.4
1.0 ~ 2.9
J3
14.7 ~ 43
1.6
1.0 ~ 2.9
J4
10 ~ 30
0.8
0.7 ~ 2
J5
10 ~ 30
2.0
0.7 ~ 2
J6
10 ~ 30
2.0
0.7 ~ 2
■ Exchange (New article installation)
Axis
Tension : T (N)
Slack : d (mm)
Pressing force : f (N)
J1
40
1.0
2.7
J2
40
1.4
2.7
J3
40
1.6
2.7
J4
28
0.8
1.9
J5
28
2.0
1.9
J6
28
2.0
1.9
■ The preset value and adjustment value in the sound wave type belt tension gauge
The sound wave type belt tension gauge of the standard
Maker:Gates Unitta Asia Company, Type:U-505
Axis
Preset value
Tension: Used belt (N)
Tension: New belt (N)
Force of pulling the
motor plate
note 1)
wait
width
span
Minimum
Maximum
Minimum
Maximum
J1
2.5
6
61
26
32
37
43
31(N) ~ 39(N)
J2
2.5
6
88
26
32
37
43
Note 1) The force when pulling the
motor plate for belt adjustment of
the J1 axis is shown.
J3
2.5
6
103
26
32
37
43
J4
2.5
4
52
18
22
26
30
J5
2.5
4
131
18
22
26
30
J6
2.5
4
131
18
22
26
30
■ Adjustment
Axis
Tension : T (N) Slack : d (mm) Pressing force : f (N)
J1
29
1.0
1.9
J2
29
1.4
1.9
J3
29
1.6
1.9
J4
20
0.8
1.3
J5
20
2.0
1.3
J6
20
2.0
1.3
<Note>
The tension of brake timing belt of the J5 and the J6 axis is automatically adjusted by the work of spring
installed in the motor plate.
Содержание RV-2F Series
Страница 1: ...Mitsubishi Industrial Robot RV 2F Series INSTRUCTION MANUAL ROBOT ARM SETUP MAINTENANCE BFP A8904 C...
Страница 2: ......
Страница 110: ...Appendix 101 Configuration flag 6Appendix...