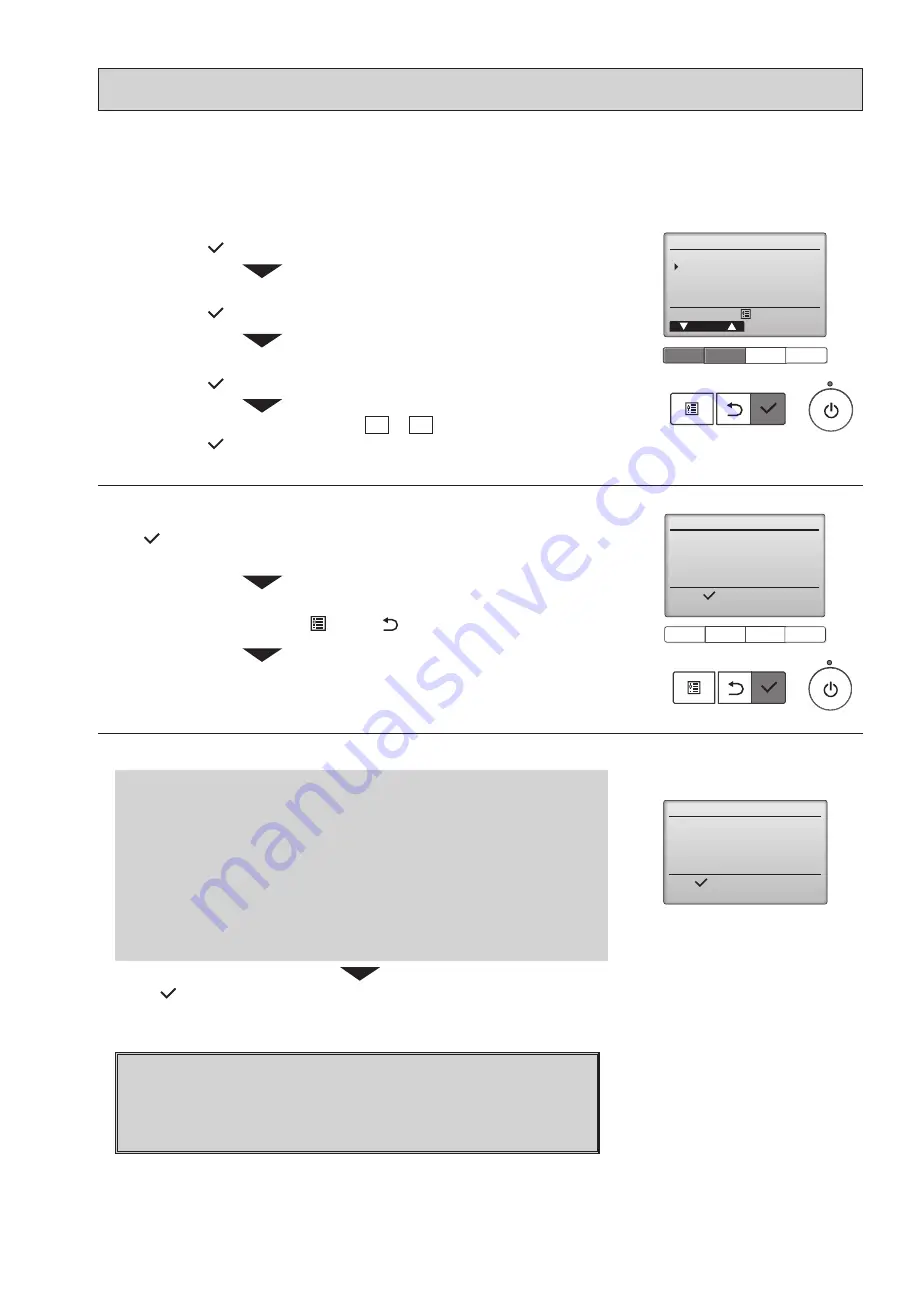
56
57
TCH067
Diagnosis
Cursor
Service menu:
Self check
Remote controller check
If operations cannot be completed with the remote controller, diagnose the remote controller with this function.
Remote controller check
:
OK
Exit
2.
Select ˝Remote controller check˝ from
the Diagnosis menu, and press
the [ ] button to start the remote controller check and see the check
results.
To cancel the remote controller check and exit the ˝Remote controller
check˝
menu screen, press the [
] or the [ ] button.
The remote controller will not reboot itself.
Check the remote controller display and see if anything is displayed
(including lines). Nothing will appear on the remote controller display if
the correct voltage (8.5–12 VDC) is not supplied to the remote control-
ler. If this is the case, check the remote controller wiring and indoor
units.
OK:
No problems are found with the remote controller. Check other parts
for problems.
E3, 6832: There is noise on the transmission line, or the indoor unit or another
remote controller is faulty. Check the transmission line and the other
remote controllers.
NG (ALL0, ALL1): Send-receive circuit fault. The remote controller needs replac-
ing.
ERC:
The number of data errors is the discrepancy between the number of bits
in the data transmitted from the remote controller and that of the data
that was actually transmitted over the transmission line. If data errors are
found, check the transmission line for external noise interference.
Remote controller check results screen
If the [ ] button is pressed after the remote controller check results are dis-
played, remote controller check will end, and the remote controller will automati-
cally reboot itself.
13-9. REMOTE CONTROLLER CHECK
3.
F1
F2
F3
F4
Select ˝
Remote controller check
˝ with the
F1 or F2 button,
and press the [ ] button.
1.
Select ˝
Service
˝ from the Main menu,
and press the [ ] button.
Select ˝
Check
˝ from the Service menu,
and press the [ ] button.
Select ˝
Diagnosis
˝ from the Check menu,
and press the [ ] button.
F1
F2
F3
F4
Remote controller check
Begin:
Start checking?
TCH067.indd 57
TCH067.indd 57
29/9/2564 13:36:50
29/9/2564 13:36:50